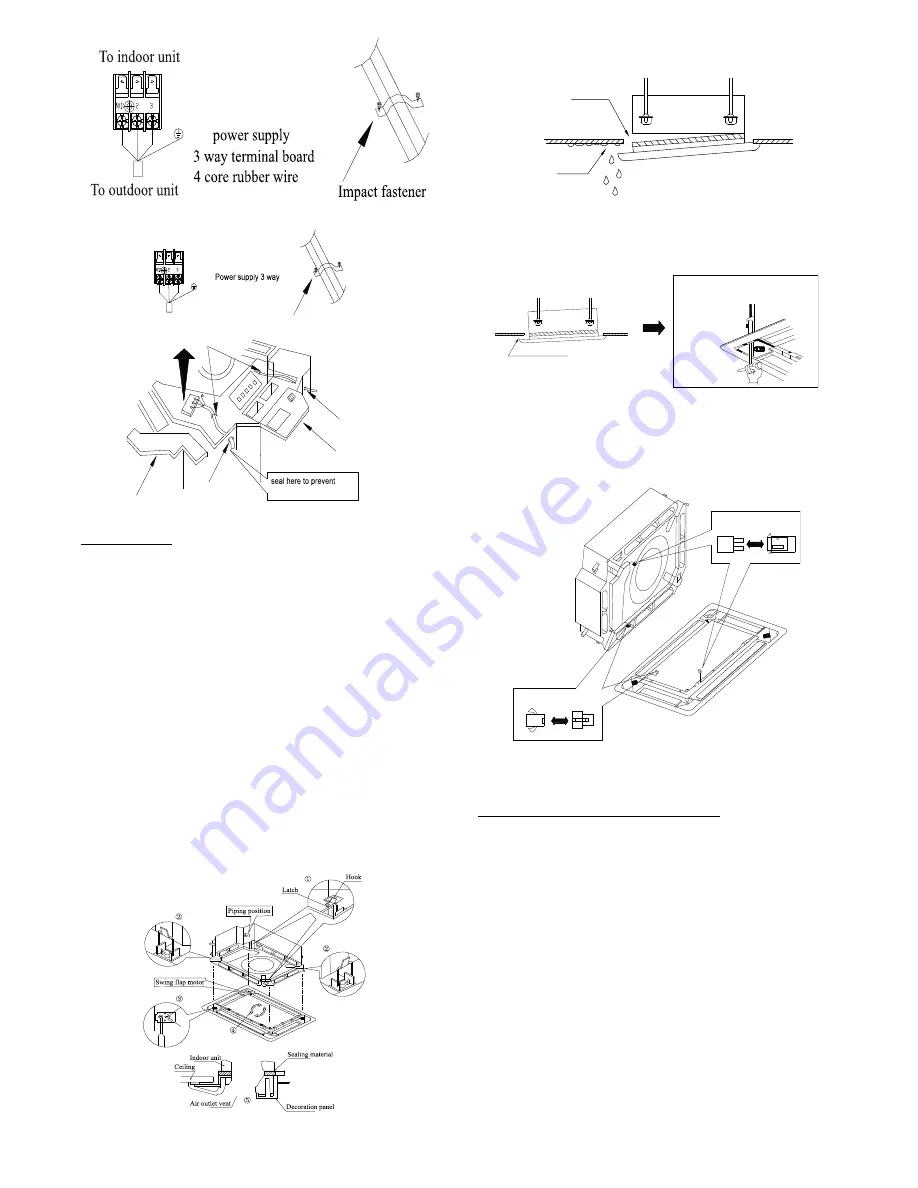
30
Fig. 40 – Power cord
To indoor unit
To indoor unit
Impact fastener
Electric box cover(1)
Cable-cross loop
Cable-cross loop
water leakage
Electric box cover(2)
terminal board 4 core
rubber wire
Fig. 41 – Power Supply
Install the panel
1 Set the panel to the indoor unit body by matching the position
of the panel’s swing flap motor to the panel’s piping position
to the indoor unit’s piping position (see Fig. 42).
2 Install the panel.
(1.) Install the panel on the indoor unit temporarily. When
installing, hang the latch on the hook located on the
opposite side of the swing flap on the panel of the
indoor unit (two positions).
(2.) Hang the remaining 2 latches to the hooks on the sides
of the indoor unit. Be careful not to let the swing motor
lead wire get caught in the sealing material.
(3.) Screw the 4 hexagon head screws under the latches in
about 3/5 in. (15 mm) and the panel should rise.
(4.) Adjust the panel by turning it toward the direction
pointed by the arrow (see Fig. 42) so the adjust board
connects well to the ceiling.
(5.) Tighten the screws until the thickness of the sealing
material between the panel and the indoor unit is
reduced to 5−8mm.
1/5 in to 1/3 in (5 mm to 8 mm)
Fig. 42 – Panel Installation
NOTE:
(1.) Improper screwing of the screws may cause issues (see Fig. 43).
Air leak
Air leak from ceiling
Water condensatation, water drop
Fig. 43 – Example of Improper Screwing Issue
(2.) If a gap still exists between the ceiling and decoration panel
after tightening the screws, re−adjust the height of the indoor
unit (see Fig. 44).
If the raising lever and drain hose are
not affect, can adjust the height of
indoor unit by the hole on the corner
of panel.
Gaps are not allowed
Fig. 44 – Improper Screwing
IMPORTANT:
After securing, ensure there is no gap between
the ceiling and the panel.
(3.) Wiring of the decoration panel (Fig. 45). Connect the joints
for the swing flap motor lead wire (at 2 places) onto the panel.
At body
At pane
At body
At pane
Fig. 45 – Connect Joints
Wireless Remote Control Installation
Mounting Bracket (if installed on the wall)
1 Use the two screws supplied with remote controller to attach
the Mounting Bracket to the wall in a location selected by
customer and within operating range.
2 Install batteries in the Remote Controller.
3 Place the Remote Controller in the remote control Mounting
Bracket.
NOTE: For remote control operation, refer to the unit Owner’s
Manual. The wireless remote should pointed to the wired controller
to receive the signal.
Wired Remote Controller (shipped with the unit)
For setup instructions, refer to the wired controller installation
manual. Connect the 4−core wire shipped with the unit to CN9 on
the indoor board and CN1 on the wired controller board.