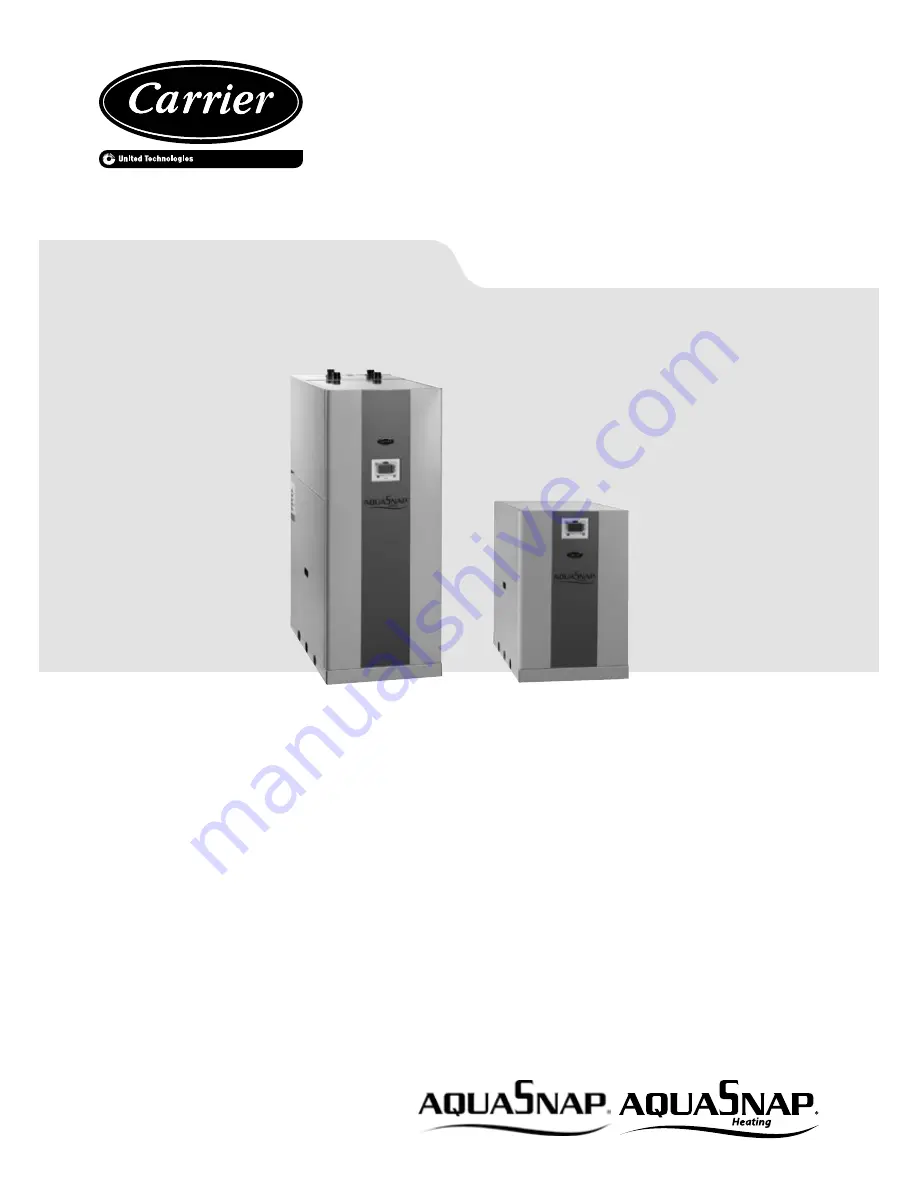
I N S T A L L A T I O N , O P E R A T I O N A N D
M A I N T E N A N C E I N S T R U C T I O N S
Water-Cooled/Condenserless
Liquid Chillers/Water-Sourced Heat Pumps
with or without Integrated Hydronic Module
61WG/30WG/30GA 020-090
Original document
Nominal cooling capacity 25-95 kW
Nominal heating capacity 29-117 kW
Unit with optional hydronic module
Standard unit
PRO-DIALOG
Summary of Contents for 30WG 020
Page 55: ...55 ...