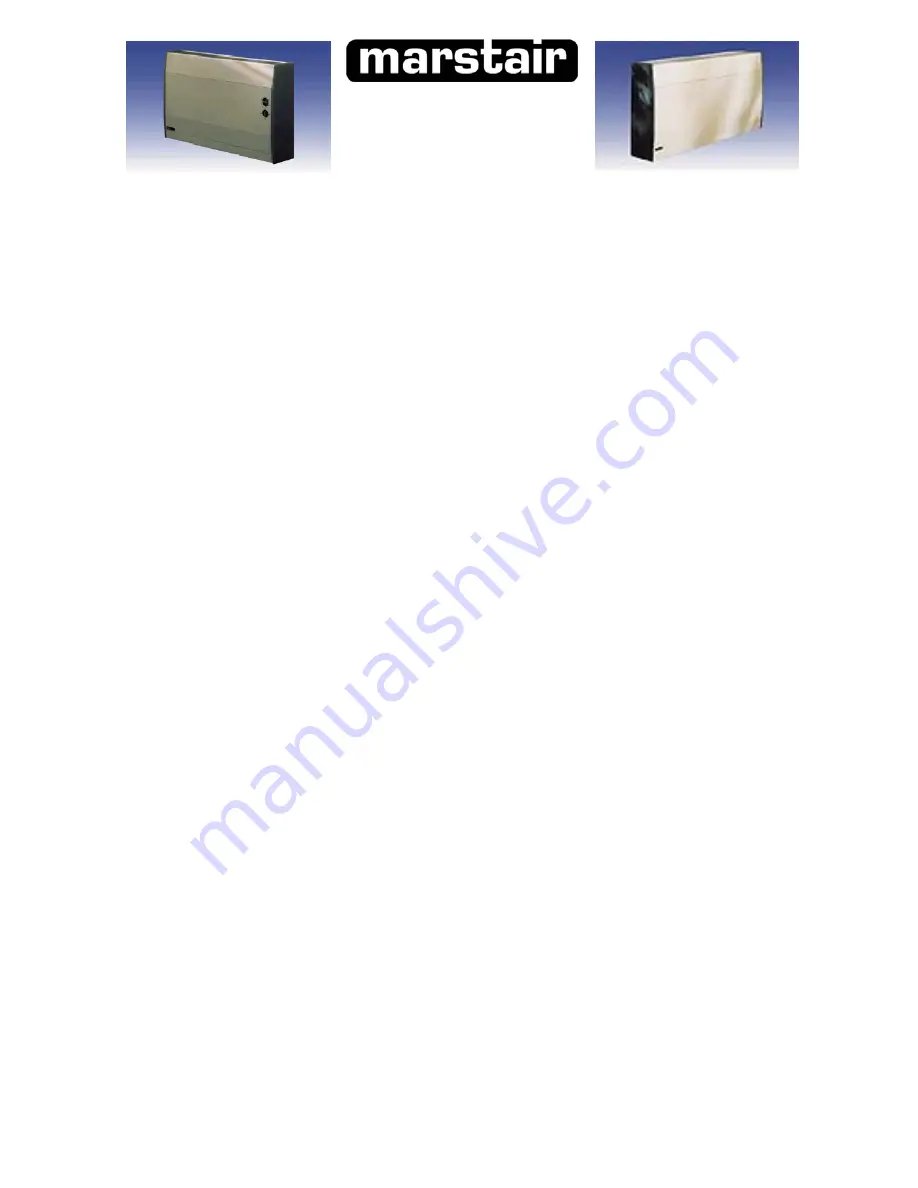
-1-
TECHNICAL MANUAL
for HL/HLR WALL MOUNTED
SPLIT SYSTEMS
(with CEILING MOUNTED OPTION)
This manual provides technical and installation information for
HL/HLR WALL MOUNTED
split systems comprising:
INDOOR UNIT
526 series
HL
527 series
HLR
MATCHED WITH
550 series MCU or MCU+ condensing units
551 series MHPUE heat pump units.
INDEX
PAGE
GENERAL
Part numbers, dimensions and weights
2 - 3
Unit features/accessories
3
SELECTION
Unit combinations, performance data
4
Airflows, sound pressure levels
5
ELECTRICAL
Electrical data, recommended fuse sizes
6 - 7
UNIT
HL/HLR
8
INSTALLATION
MCU(+) and MHPUE units
9 - 10
Pipework, restrictors
10 - 12
Condensate removal, air deflection
12
HLR remote controller
13
Electrical connections
14
HLR conversion to air conditioner mode
14
Evacuating and charging
15
WIRING
HL/HLR units
16
DIAGRAMS
MCU(+)
17 - 18
MHPUE
19 - 20
Interconnection
21 - 23
OPERATION
HL/HLR
24 - 25
MAINTENANCE
User maintenance
25
HL/HLR KITS
Ceiling mounting
26
Condensate pump
27 - 28
LPHW coil
29
De-ice thermostat
30
FAULT FINDING
All units
31
TEV Ltd.,
Armytage Road, Brighouse,
West Yorkshire. HD6 1QF, UK.
Tel: +44 (0) 1484 405600
Fax: +44 (0) 1484 405620
52708017-06
Email: [email protected]
Summary of Contents for 526 HL Series
Page 13: ... 13 ...
Page 16: ... 16 HL WIRING DIAGRAM HLR WIRING DIAGRAM ...
Page 17: ... 17 MCU WIRING DIAGRAMS 1 Phase MCU 90 3 Phase MCU 90 to 100 3 Phase MCU 130 to 165 ...
Page 18: ... 18 MCU WIRING DIAGRAMS 1 Phase MCU 90 3 Phase MCU 90 to 100 3 Phase MCU 130 to 165 ...
Page 19: ... 19 MHPUE WIRING DIAGRAMS 1 Phase MHPUE 90 3 Phase MHPUE 90 ...
Page 20: ... 20 3 Phase MHPUE 100 to 130 ...