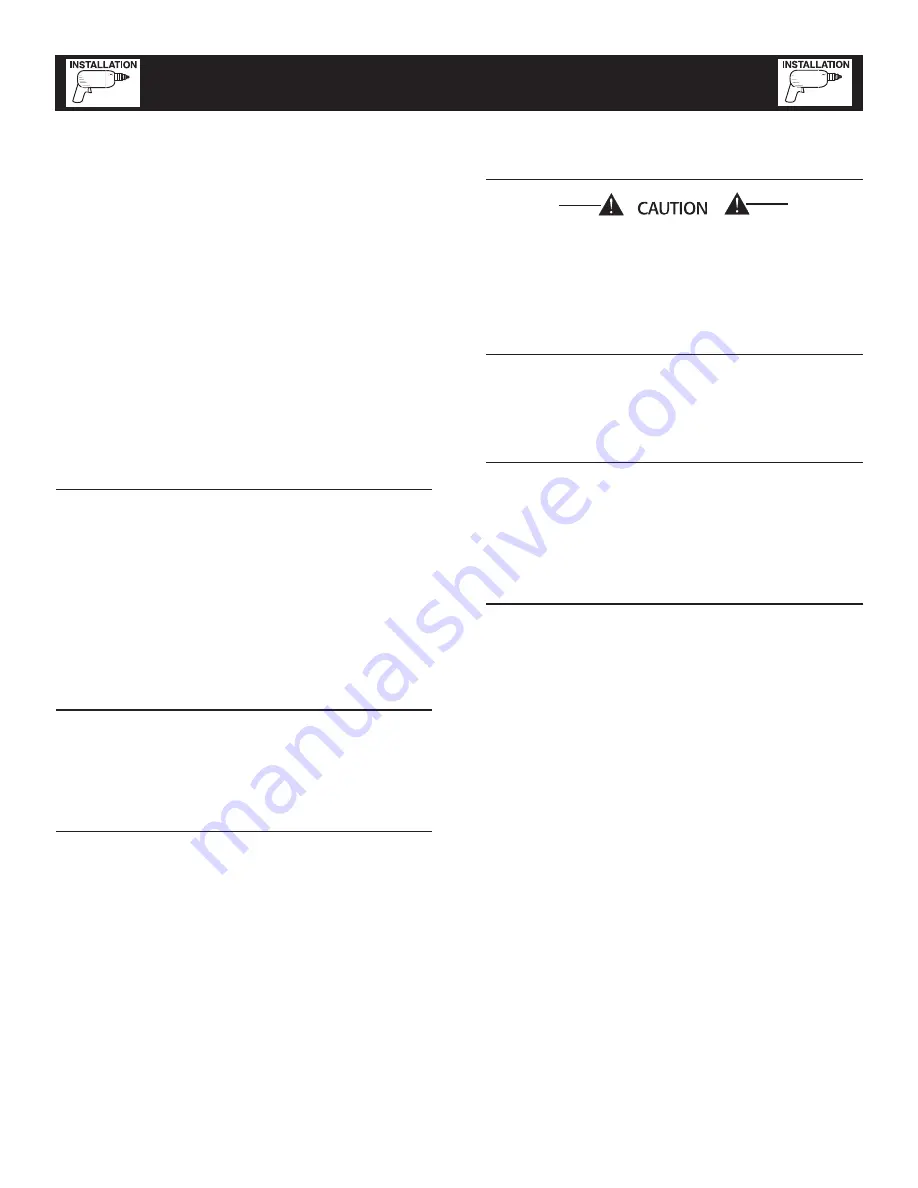
INSTALLATION
Refer to the separate “Installation Guide” supplied
with the unit.
PREPARATION BEFORE START-UP
The instructions in this section assume that the
standby generator has been properly installed, ser-
viced, tested, adjusted and otherwise prepared for
use by a competent, qualified installation contractor.
Be sure to read the “Safety Rules”, as well as all other
safety information in this manual, before attempting
to operate this (and related) equipment.
Before starting the generator for the first time, the
installer must complete the following procedures. For
follow-up maintenance information and/or service
intervals, please refer to the “Maintenance” section
and the “Service Schedule”.
TRANSFER SWITCH
If this generator is used to supply power to any elec-
trical system normally powered by an electric utility,
the National Electrical Code requires that a transfer
switch be installed. The transfer switch prevents elec-
trical backfeed between two different electrical sys-
tems. (For additional information, see the applicable
transfer switch manual for this unit.) The transfer
switch, as well as the generator and other standby
components, must be properly located and mounted
in strict compliance with applicable codes, standards
and regulations.
FUEL SYSTEM
Make sure the fuel supply system to the generator (a)
delivers the correct fuel at the correct pressure and (b)
is properly purged and leak tested according to code.
No fuel leakage is permitted. See “Specifications” for
more information.
GENERATOR SET LUBRICATION
Check the engine crankcase oil level before operating
and add oil to the proper level – the dipstick “FULL”
mark. Never operate the engine with the oil level
below the dipstick “ADD” mark. See “Specifications”
and “Engine Oil Recommendations”.
NOTE:
This engine is shipped from the manufacturer
with “break-in” oil. This oil should be changed
after 30 hours of operation.
PRIOR TO INITIAL START-UP
Prior to initially starting the generator, it must
be properly prepared for use. Any attempt to
crank or start the engine before it has been
properly serviced with the recommended types
and quantities of engine fluids (oil, coolant, fuel,
etc.) may result in an engine failure.
ENGINE COOLANT
Have the engine cooling system properly filled with
the recommended coolant mixture. Check the system
for leaks and other problems. See “Specifications”
and “Coolant” sections.
BELT TENSION
Check-the engine-fan belt tension and condition prior
to placing the unit into service and at recommended
intervals. Belt tension is correct when a force of
approximately 22 pounds (10 kg), applied midway
between pulleys, deflects the belt about 3/8- to 5/8-
inch (10 to 16 mm).
ELECTRICAL SYSTEM
Make sure the generator is properly connected to an
approved earth ground.
Make sure the generator battery is fully charged,
properly installed and interconnected, and ready for
use.
NOTE:
Battery charger must be connected to 120 VAC, 15
amp circuit to operate.
Check to ensure that there are no loose electrical con-
nections. Restrain any loose wires to keep them clear
of any moving generator set components.
INITIAL INSPECTION FOR GENSET
STARTUP
Inspect for the following.
• Freight Damage.
• Manuals present.
• Fluid Levels (Oil, coolant, battery, Gear Drive).
• Correct fuel piping.
• Adequate air flow, clearances and ventilation per
installation drawings and applicable codes.
• Correct AC and DC wire size, connections and
grounding. Control and communication wiring to/
from the transfer switch must be run in a separate
conduit from the AC power leads.
8-1
Standby Generator Sets
Installation
Install002 Rev.
C 01/07
Summary of Contents for 2.4L 35kW
Page 26: ...Standby Generator Sets Notes...
Page 27: ...Standby Generator Sets Notes...
Page 28: ...Standby Generator Sets Notes...
Page 29: ...Standby Generator Sets Notes...
Page 30: ......
Page 32: ......
Page 34: ......
Page 36: ......
Page 38: ......
Page 40: ......
Page 42: ......
Page 44: ......
Page 46: ......
Page 48: ......
Page 50: ......
Page 52: ......
Page 54: ......
Page 55: ......
Page 56: ......
Page 57: ......
Page 58: ......
Page 59: ......
Page 60: ......
Page 61: ......
Page 62: ......
Page 63: ......
Page 64: ......
Page 65: ......
Page 66: ......