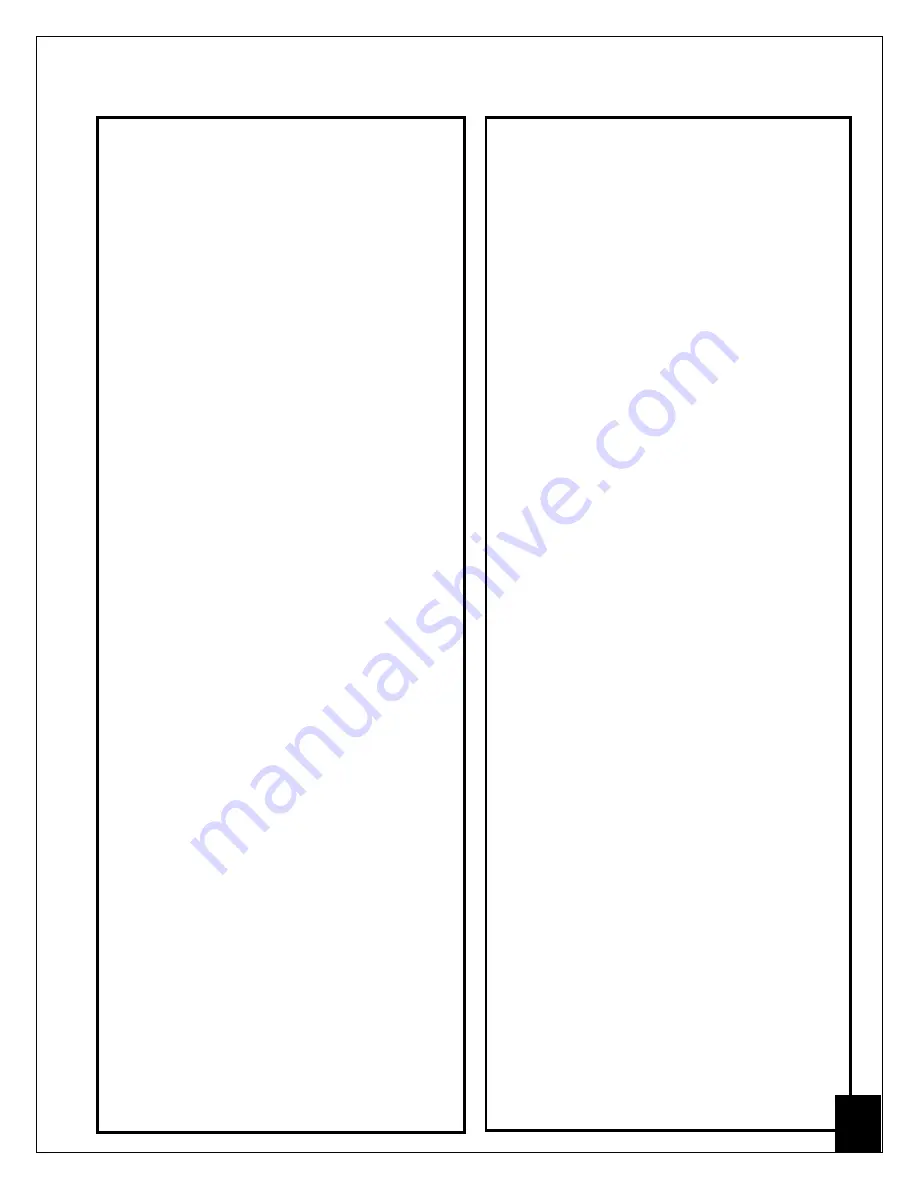
3.2 Connection Information
Refer to the following connection diagrams
for appropriate model:
•
For Model BRC702-E0C, –EBC, -E00 and
-EB0 refer to Connection Diagram D11379
•
For Models BRC702-000 and -0B0 refer to
Connection Diagram D11380
•
For Models BRC705-000 and -0B0, refer
to Connection Diagram D11382
•
For Models BRC705-E0C, –EBC, -E00
and -EB0, refer to Connection Diagram
D11381
Wiring Precautions
WARNING!
Although the Blazer
®
IV Control Circuits
are isolated, high voltage potentials can be
present between earth or chassis ground
and any point in the circuit depending on
what the control circuit is connected to. All
test instruments should be isolated from
ground to prevent damage to the instrument
or control.
•
Ground the control only at GND position
on TB-1.
•
Use shielded cable for all speed pot,
tachometer, encoder, forward run, reverse
run, forward jog, reverse jog, ramp stop,
emergency stop and special wiring.
Connect the shield to circuit common at the
control end only. The shield should not be
connected to ground at either end.
Connecting the shield to ground may result
in noise problems. These wires should be
routed away from all A. C. power,
armature, field, and relay coil wiring.
•
Any relays, contactors, motor starters,
solenoids, etc. located in close proximity to
or on the same A. C. line as the Blazer
®
IV
control should have a transient suppression
device in parallel with the coil to minimize
interference with the control.
3.3 Terminal Connections
L1 and L2 (A. C. Line Connections):
These
terminals are used for the A. C. line input.
For Models BRC702, either 115 VAC or
230 VAC input can be connected to terminals
TB1-1 and TB1–2. If 115 VAC is to be used
as input, place J2, J3, J4 & J5 in the 115V
position. If 230 VAC is to be used as input,
place J2, J3, J4 & J5 in the 230V position.
For Models BRC705, only 230 VAC may
be used, and there are no jumpers to set.
Connect the line to terminal lugs L1 and L2.
A1 and A2 (Armature Connections):
Motor
lead A1 connects to terminal A1 and motor
lead A2 connects to terminal A2. When the
drive is engaged in the forward direction, these
connections will produce CCW motor rotation
when viewed from the commutator end. The
armature leads should be switched if reverse
rotation is desired.
F1 and F2 (Field Connections):
Motor field
lead F1 connects to terminal F1 and motor
field lead F2 connects to terminal F2. There is
no connection required to these terminals when
a permanent magnet type motor is used.
TB2 – 1 through 7 (External Logic Control
Connections):
These connections are provided
so that a remote station or PLC can be used to
control the drive. The Ramp Stop terminal can
be programmed to accept a NO (active high)
signal or a NC (active low) signal. Signals
provided to any of these terminals can be
momentary or maintained signal.
TB2 – 1: Emergency Stop
TB2 – 2: Ramp Stop
TB2 – 3: Run Forward
TB2 – 4: Run Reverse
TB2 – 5: Jog Forward
TB2 – 6: Jog Reverse
TB2 – 7: +15 VDC (logic power)
6
Summary of Contents for BLAZER IV
Page 18: ...Prints 7 17 ...
Page 19: ...18 ...
Page 20: ...19 ...
Page 21: ...20 ...
Page 22: ...21 ...
Page 23: ...22 ...
Page 24: ...23 ...
Page 25: ...24 ...
Page 26: ...25 ...
Page 27: ...26 ...
Page 28: ...27 ...
Page 29: ...28 ...
Page 30: ...29 ...
Page 31: ...30 ...
Page 32: ...31 ...
Page 33: ...32 ...
Page 34: ...33 ...
Page 35: ...34 ...
Page 36: ...35 ...
Page 37: ...36 ...
Page 38: ...37 ...
Page 39: ...38 ...
Page 40: ...Notes 39 ...