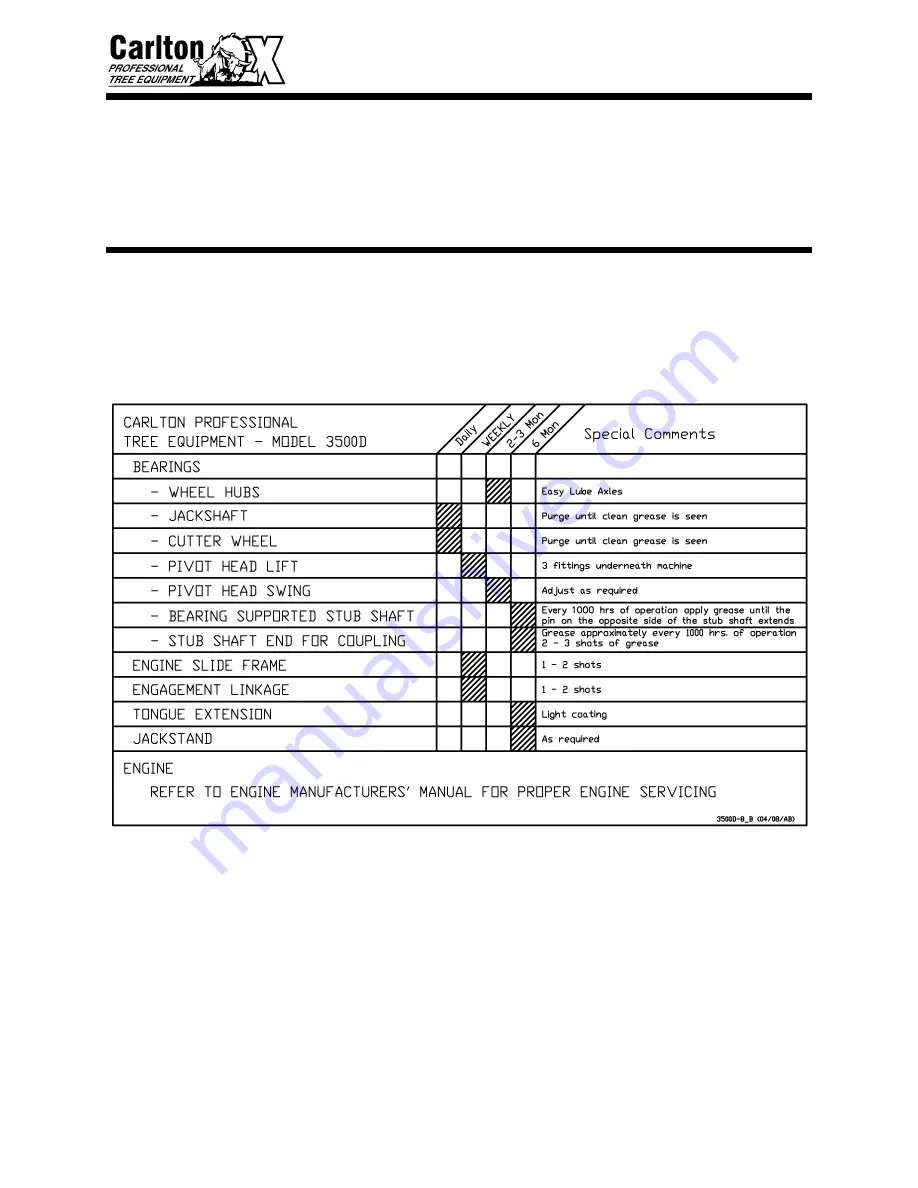
3500D LUBRICATION SCHEDULE
27
•
The model 3500D, as well as all of our
machines, is built to be a rugged performer.
Your new machine is sturdy and our design
goals are simplicity and reliability.
•
A regularly scheduled maintenance
program will pay big dividends in machine
life, performance and avoided downtime.
Lubrication
Schedule
•
USE TEXACO
®
STARPLEX II GREASE.
Summary of Contents for 3500D
Page 2: ......
Page 4: ......
Page 5: ...3500D SAFETY ALERT...
Page 6: ......
Page 7: ...3500D SAFETY ALERT...
Page 8: ......
Page 9: ...3500D SAFETY ALERT...
Page 10: ......
Page 11: ...3500D SAFETY ALERT...
Page 12: ......
Page 13: ...3500D SAFETY ALERT...
Page 14: ......
Page 16: ......
Page 18: ......
Page 20: ......
Page 22: ......
Page 27: ...3500D MACHINE SPECIFICATIONS 5...
Page 52: ...3500D MACHINE WIRING 30 STANDARD WIRING DIAGRAM...
Page 53: ...3500D MACHINE WIRING 31 REMOTE WIRING DIAGRAM...
Page 54: ...3500D MACHINE WIRING 32 REMOTE BOX WIRING...
Page 58: ...3500D LIGHTS BRAKES ASSEMBLY 36 TRAILER LIGHTS BRAKES WIRING...
Page 75: ...3500D SERVICING BELTS 53 Replacing Poly Chain Belt...
Page 91: ...3500D HYDRAULIC ASSEMBLY 69 REMOTE CONTROL HYDRAULIC ASSEMBLY...
Page 94: ...3500D HYDRAULIC ASSEMBLY 72 SWING OUT CONTROLS HYDRAULIC ASSEMBLY...
Page 100: ...3500D FRAME ASSEMBLY 78 BASE FRAME ASSEMBLY...
Page 102: ...3500D FRAME ASSEMBLY 80 REMOTE BOX ASSEMBLY...
Page 105: ...3500D PIVOT ASSEMBLY 83...
Page 112: ...3500D CUTTER WHEEL ASSEMBLY 90...
Page 114: ......
Page 115: ......
Page 116: ......
Page 117: ......
Page 118: ......
Page 119: ......
Page 120: ......
Page 121: ......
Page 122: ......
Page 123: ......
Page 124: ......
Page 125: ......
Page 126: ......
Page 127: ......
Page 128: ......
Page 129: ......