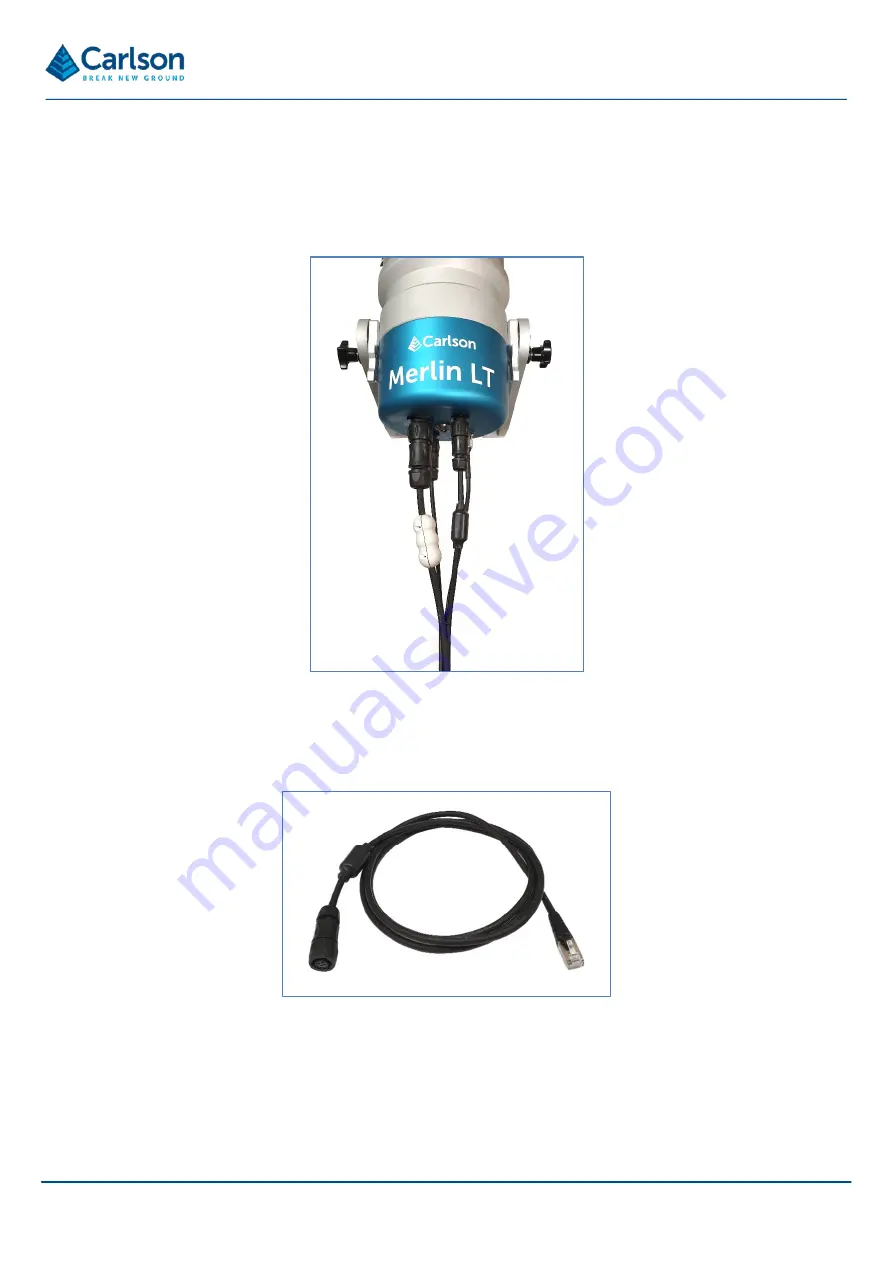
P a g e |
11
3.2 Cables
All supplied cables must be connected and correctly interfaced for the Merlin LT to run fully optimised operations.
When secured to the back of the Merlin LT, each connection is protected against the environment.
3.2.1 Ethernet cable
The Ethernet cable provides communication between the Merlin LT and the vessel’s main PC running navigation
software.
The Cat 6 Ethernet cable attaches to the back of the Merlin LT with a four-pin female Souriau connector. The
standard RJ45 connector connects to the PC.
Figure 5 All cables connected to the Merlin LT
Figure 6 Ethernet cable