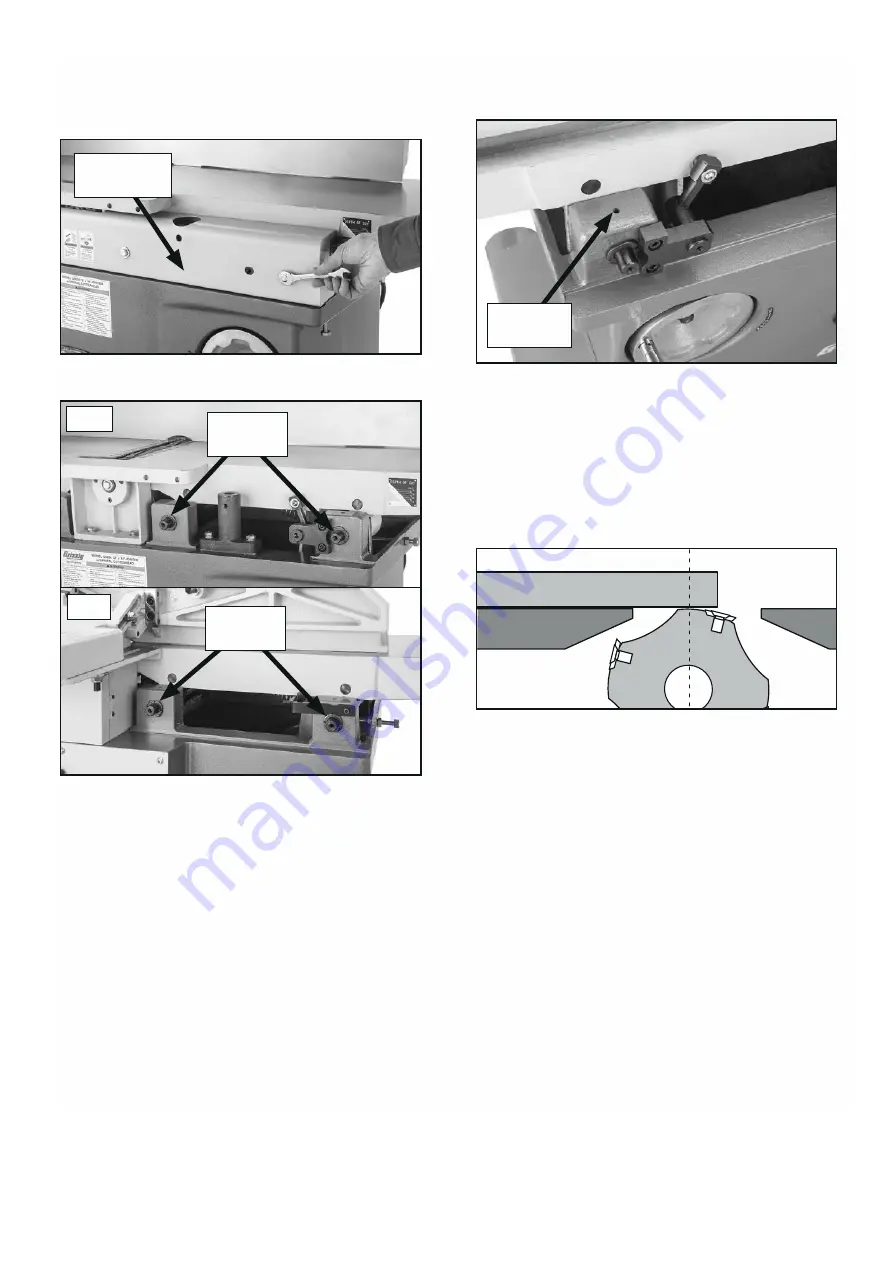
Pg.39
Model G0834 (Mfd. Since 12/17)
-41-
4.
Remove front and rear table covers to
expose eccentric bushings, as shown in
Figures 54–55
.
5.
Loosen set screw on each eccentric bushing
(see
Figure 56
).
Figure 56.
Location of eccentric bushing set
screw.
Figure 54.
Removing front table cover.
Front Table
Cover
Straightedge
Outfeed Table
Figure 57.
Adjusting outfeed table even with
cutterhead body.
Figure 55.
Locations of front and rear eccentric
bushings.
Eccentric
Bushings
Front
Rear
Eccentric
Bushings
6.
Place straightedge on outfeed table so it
hangs over cutterhead, rotate motor pulley so
straightedge is between inserts, then lower
outfeed table until straightedge just touches
cutterhead body, as shown in
Figure 57
.
Set Screw
(1 of 4)