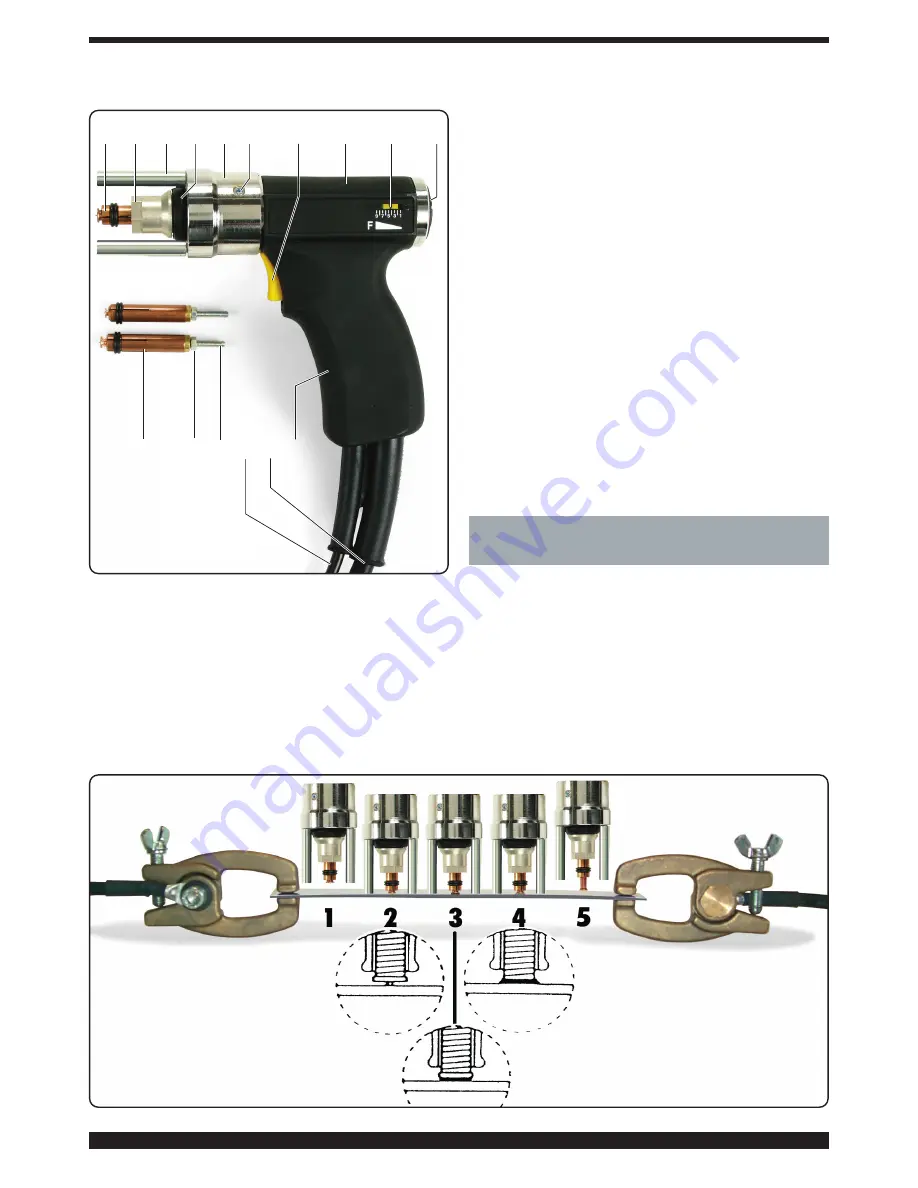
9
3.2
GUN DESCRIPTION
K-
Gun body
L-
Grip
M-
Control cable
N-
Welding current cable
O-
Welding command button (works only with the gun
pressed against the sheet metal)
P-
Force setting indicator
Q-
Force adjustment screw (increases when turned clock
wise)
R-
Ring to hold spacer Z
S-
Clamp locking ring-nut
T
- Safety bellows
U-
Holding screws for ring R
V-
Screw to adjust stud bolt protrusion
W-
Holding nut.
X-
Stud bolt gripping clamp
Y-
Screw
Z-
Spacer
3.2.1 Preparing the gun
Always use high-quality pins with contact point start-up for
capacitor discharge welding, which comply with standards
and are made of a metal compatible with the welding to be
done.
Having selected the stud bolt to be welded for type, diame-
ter, length and material, use and adjust the clamp according
to the corresponding diameter.
Insert the stud bolt in the clamp
X
so that it is firmly held in
place by the four springs.
Adjust the protrusion of the stud bolt from the front of the
clamp to 0.8 ÷ 1.2 mm using the screw
V
, then tighten with the
nut
W
(figure 2).
Insert the clamp
X
into the chuck of the gun (fig. 2), press
until you feel it rest all the way down, and tighten the nut S
using the 17-mm hexagon wrench provided.
4
OPERATING PRINCIPLE OF WELDING
THREADED STUD BOLTS WITH CONTACT
POINT START-UP
(Fig. 3)
The stud bolt is inserted in the clamp X (phase 1), then posi-
tioned and pressed with its start-up contact directly against
the surface of the sheet metal to be welded (phase 2). The
spring of the gun presses the stud bolt against the metal, the
start command begins sending current which melts the
start-up contact, and the electrical arc is propagated along
the entire surface of the stud bolt (phase 4) pushed against
the metal surface. The molten metal solidifies, thereby weld-
ing the stud bolt (phase 5).
X
X
W V M N L
S
Z
T
R U
O
K
P
Q
Fig. 2
Fig. 3