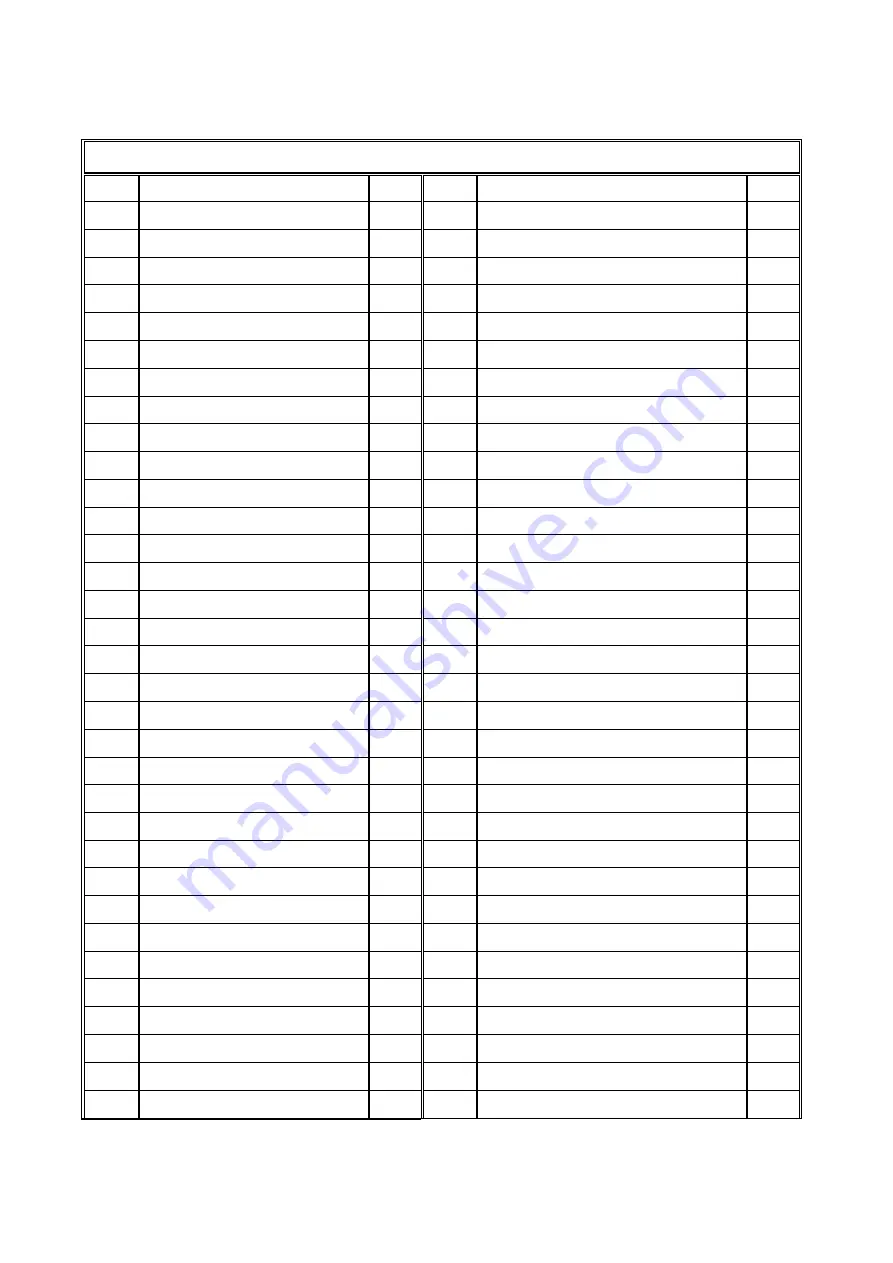
23
PART LIST
303S RIP SAW 3/3
NO
PART NAME
Q’TY
NO
PART NAME
Q’TY
501
Slide seat press board
1
534
Bearing nut(left thread)
2
502
Block
1
535
Roller
2
503
Feeding roller seat
1
536
Side roller seat
2
504
Safety guard(outfeed)
1
537
Oil nozzle (straight)
2
505
Hinge
1
538
Roller seat (big)
1
506
Dust hood
1
539
Roller shaft (long)
1
507
Pin
1
540
Roller (big)
1
508
Spaced ring
4
541
Spring plate shaft seat
2
509
Connecting rod
2
542
Spring plate
22
510
Guard plate
1
543
Spring plate (short)
2
511
Lobe knob
1
544
Spring plate shaft
1
512
Bearing 696
3
545
Spring plate buffer
1
513
Lifting nut
1
546
Steel ball
1
514
L handle
1
547
Spring
1
515
Index
1
548
Anti-kickback rocker arm
1
516
Pressure block
1
549
Anti-kickback rocker arm handle
1
517
Slide seat press board
1
518
Spring fixing nut
6
519
Spring (short)
2
520
Bearing fixing nut
2
521
Bearing 6204
4
522
Roller
1
523
Bearing nut
2
524
Rear roller seat
1
525
Roller shaft (long)
1
526
Oil nozzle
2
527
Spindle
4
528
Side roller seat
2
529
Spring (long)
4
530
Roller shaft (short)
4
531
Roller (small)
2
532
Bearing 6202
8
533
Bearing nut (right thread)
2
Summary of Contents for 303S
Page 8: ...5 SOCKET FOR LASER There is a socket for a laser mounted on the electric cabinet s upper ...
Page 16: ...13 WIRING DIAGRAM 1 ...
Page 17: ...14 WIRING DIAGRAM 2 ...
Page 18: ...15 DIAGRAM PART LIST ...
Page 19: ...16 ...
Page 20: ...17 ...
Page 21: ...18 ...
Page 22: ...19 ...