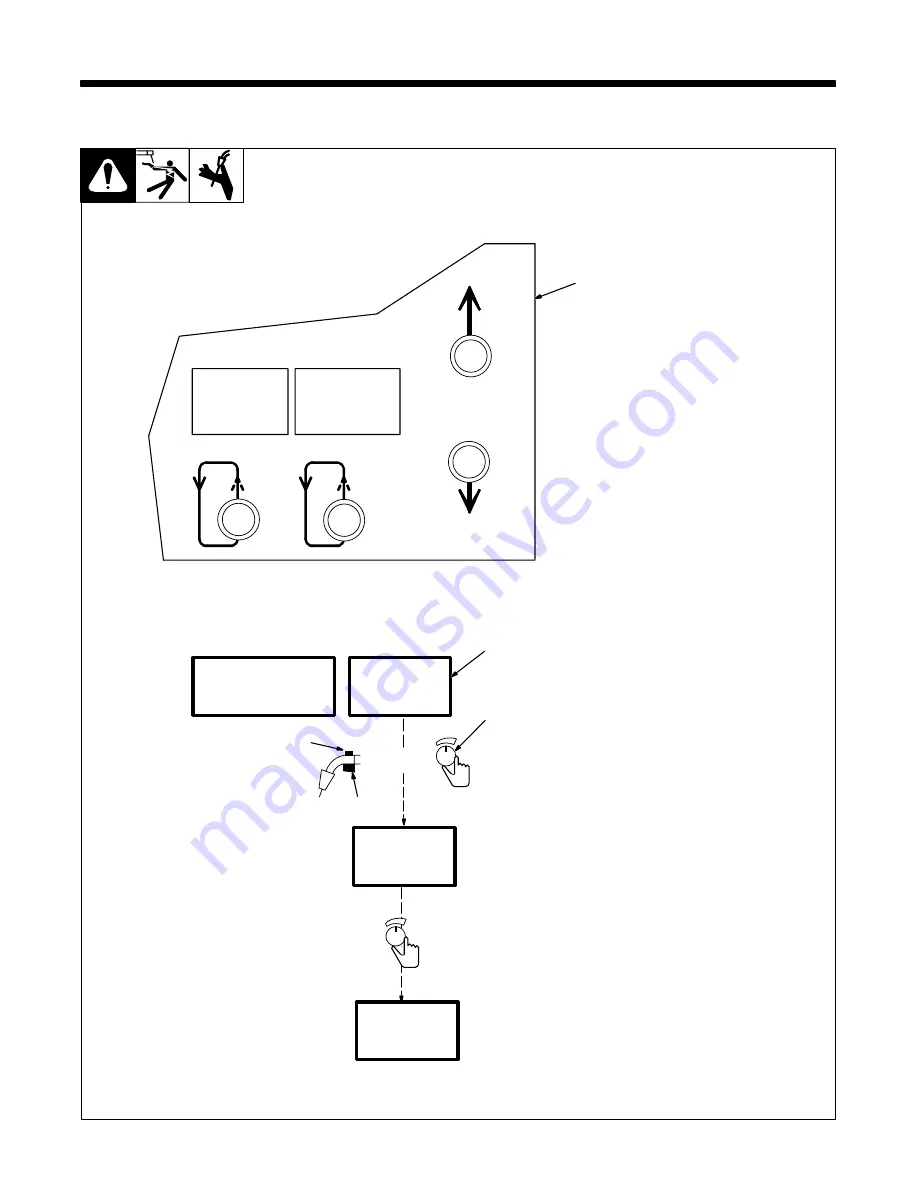
OM-1587 Page 21
SECTION 7 – SETTING DUAL SCHEDULE PARAMETERS
7-1.
Selecting Dual Schedule Pair
Dual Schedule is used with two
consecutive weld programs 1 & 2,
3 & 4, 5 & 6, or 7 & 8. Any program
type (MIG, Adaptive Pulse, or
Pulse) can be combined in dual
schedule.
1
Side Panel Display
Use side panel to turn feature on.
See Menu Guide for detailed
programming steps.
2
Front Panel Display
Press front panel parameter select
button to select program number.
3
Front Panel Display Control
4
Dual Schedule Switch (See
Section 7-2)
.
Switch type is set in System
Setup.
5
Welding Gun Trigger
Selecting dual schedule program A
or B is done by using Display Con-
trol, dual schedule switch, or gun
trigger (depending on system
setup).
When program B is active, turn
Display Control one click clockwise
to select another pair of dual sched-
ule programs.
.
Programs can be rearranged in
desired order using the data
card. See Section 8.
P r o c e s s
S e q u e n c e
> D u a l S chd
C a r d
> P r g
1 & 2
O n
2
1 8 . 0 V
2 0 0
I P M
> P r g
1
D u a l
A
> P r g
2
D u a l
B
> P r g
3
D u a l
A
4
3
5
Or
Display
Control
Display
Control
1
Summary of Contents for C-D64M
Page 2: ......
Page 20: ...OM 1587 Page 16 Notes ...
Page 44: ...OM 1587 Page 40 SECTION 15 ELECTRICAL DIAGRAM Figure 15 1 Circuit Diagram ...
Page 45: ...OM 1587 Page 41 SD 184 796 B ...