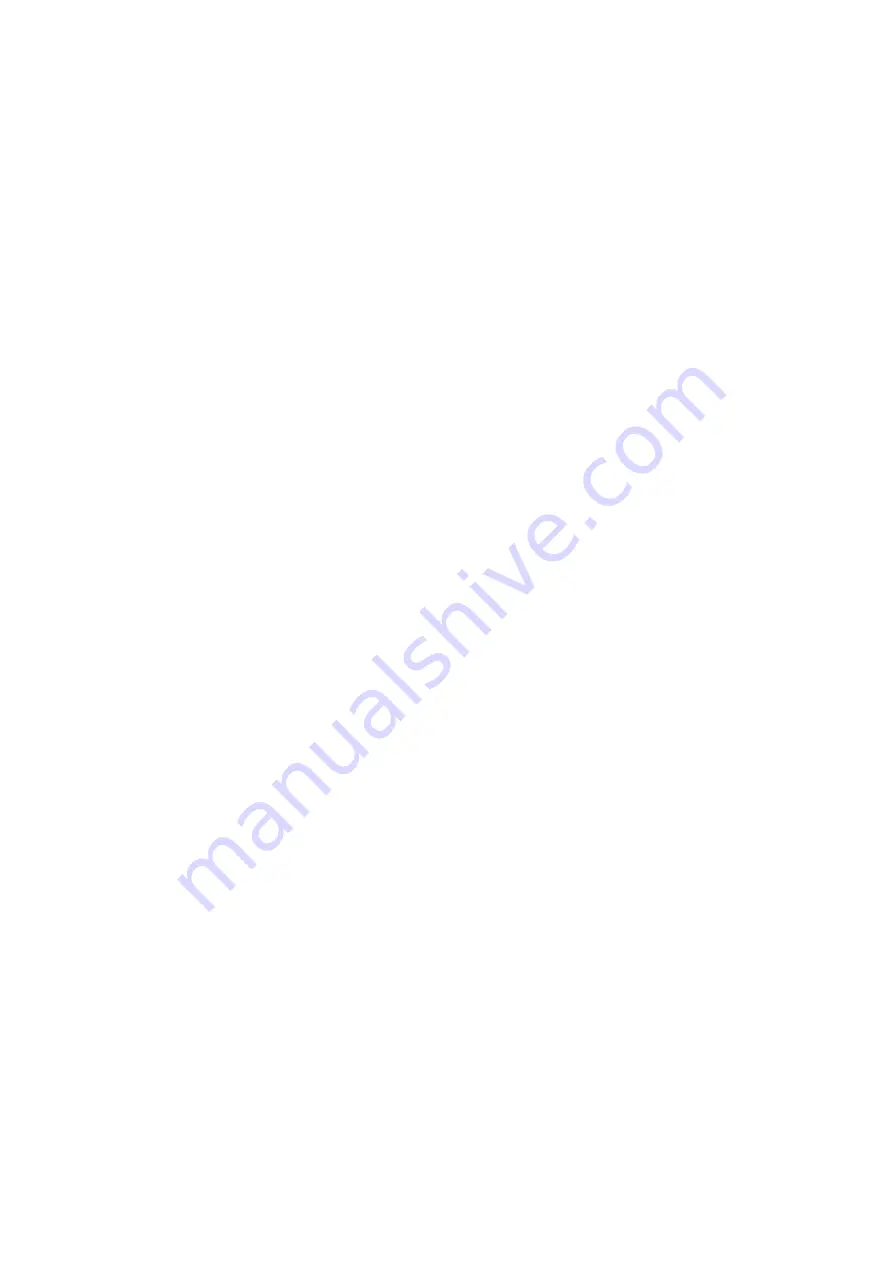
1
iP4300
SIMPLIFIED SERVICE MANUAL
1. PRODUCT LIST
2. PRODUCT SPECIFICATIONS
3. ERROR DISPLAY
4. REPAIR
5. SERVICE MODE
6. EXTERNAL VIEW / PARTS LIST
7. TROUBLESHOOTING FLOWCHART
8. SPECIAL NOTES ON SERVICING
9. PRODUCT TECHNICAL INFORMATION
APPENDIX 1: SERVICE TEST PRINT
APPENDIX 2: EEPROM INFORMATION PRINT
QY8-13BA-000
Rev. 00
July 25, 2006
Canon Inc.
Summary of Contents for Pixma iP4300 Series
Page 13: ...13 ...
Page 23: ...FIGURE 1 PRINTER PRINT HEAD ...
Page 25: ...FIGURE 2 AC ADAPTER ...
Page 27: ...FIGURE 3 OPERATION PANEL UNIT MAIN CASE UNIT ...
Page 29: ...FIGURE 4 BOTTOM CASE UNIT INK ABSORBER ...
Page 31: ...FIGURE 5 LOGIC BOARD ASS Y ...
Page 32: ...FIGURE KEY No PART NUMBER RANK QTY DESCRIPTION REMARKS 5 1 QM3 1266 000 1 LOGIC BOARD ASS Y ...
Page 33: ...FIGURE 6 SHEET FEED UNIT ...
Page 35: ...FIGURE 7 CARRIAGE UNIT ...
Page 37: ...FIGURE 8 PLATEN UNIT ...
Page 39: ...FIGURE 9 PURGE UNIT ...
Page 41: ...FIGURE 10 PAPER FEED CARRIAGE LIFT PART ...
Page 43: ...FIGURE 11 OPTION CONSUMABLES ...
Page 45: ...FIGURE 12 TOOL ...