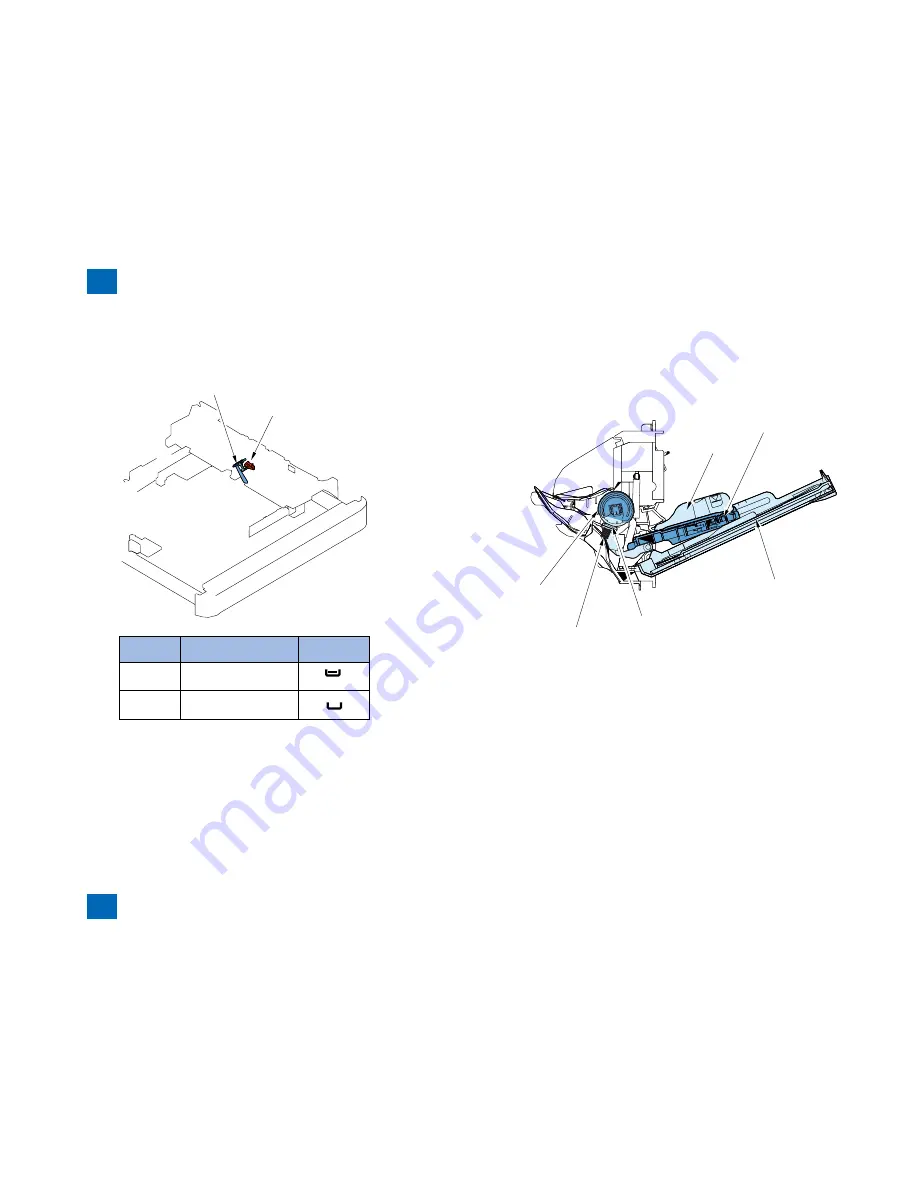
2
2
2-67
2-67
Technology > Pickup Feed System > Controls > Multi-Purpose Pickup Assembly
Technology > Pickup Feed System > Controls > Multi-Purpose Pickup Assembly
Paper level sensor
This machine does not have the paper level sensor in the cassette.
This machine has the cassette 1 paper sensor (S2) to detect the paper.
Cassette 1 Paper Sensor (S2)
Flag
Cassette
paper sensor
Paper level
Display
OFF
paper presence
ON
paper absent
●
F-2-95
F-2-95
T-2-38
T-2-38
Multi-Purpose Pickup Assembly
Overview
The paper in the tray of the manual feed pickup unit is forced against the manual feed pickup
roller by the work of the pickup guide plate, and only a single sheet
of paper is separated and moved into the machine by the work of the manual feed pickup
roller and the separation pad.
Side guide
Pickup guide plate
Manual feed pickup tray
Separation pad
Pressure spring
Manual feed
pickup roller
Paper Presence Detection
The paper presence is detected by the Multi-Purpose Tray Paper Presence Sensor.
When the paper absence is detected, if there is the same size & same type paper exists in
other cassette, auto cassette change is executed.
Paper Size Detection
This machine does not have the paper size detection detection function. The user must set
the size of the paper in the multi manual feed tray using the operation panel, or the user must
register a fixed size in the user mode.Image masking area is regulated based on the result of
paper width detection so that the image to be reproduced does not beyond the paper width.
■
●
●
●
F-2-96
F-2-96
Summary of Contents for imageRUNNER 2520
Page 1: ...9 8 7 6 5 4 3 2 1 imageRUNNER 2530 2525 2520 Series Service Manual ...
Page 4: ...Blank Page ...
Page 16: ...1 1 Product Overview Product Overview Product Lineup Feature Specifications Name of Parts ...
Page 111: ...3 3 Periodical Service Periodical Service Consumable Parts and Cleaning Parts ...
Page 159: ...5 5 Adjustment Adjustment Outline Adjustment when replacing parts Image position adjustment ...
Page 166: ...6 6 Troubleshooting Troubleshooting Upgrading Targets and Procedure ...
Page 171: ...7 7 Error Code Error Code Overview Error Code Jam Code Alarm Code ...
Page 186: ...8 8 Service Mode Service Mode Outline Details of Service Mode ...
Page 321: ...Service Tools General Circuit Diagram Appendix ...