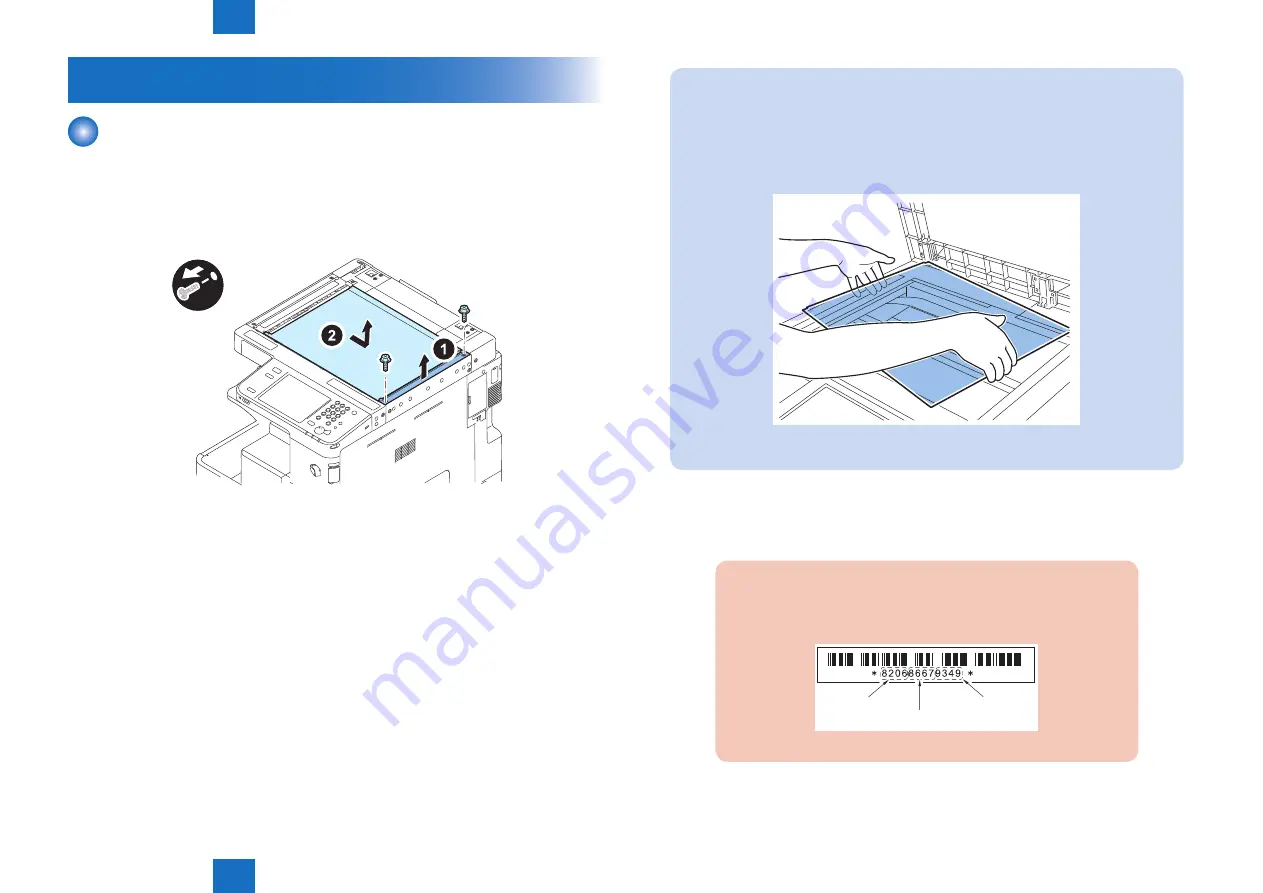
4
4
4-4
4-4
Parts Replacement and Cleaning Procedure > Original Exposure System (Reader) > Removing the Platen Glass
Parts Replacement and Cleaning Procedure > Original Exposure System (Reader) > Removing the Platen Glass
Original Exposure System (Reader)
Removing the Platen Glass
<Procedure>
1) Open the platen cover (platen board cover/ADF).
2) Remove the glass retainer.
• 2 screws
x2
F-4-7
NOTE:
When removing the platen glass, take care not to touch the following parts with your
fingers:
• Glass surface
• Standard white plate
Soils on these parts may cause white/black lines on images.
If they are soiled, clean them with a lint-free paper moistened with alcohol.
F-4-8
<Processing after replacing the parts>
Take the action stated below in the service mode.
CAUTION:
Be sure to make the white plate data adjustment before ADF white
level adjustment.
W-PLT-X
W-PLT-Y
W-PLT-Z
F-4-9
1. Enter the value indicated on the platen glass in the following service mode:
(Lv.1) COPIER> ADJUST> CCD> W-PLT-X/Y/Z (Input of standard white plate data)