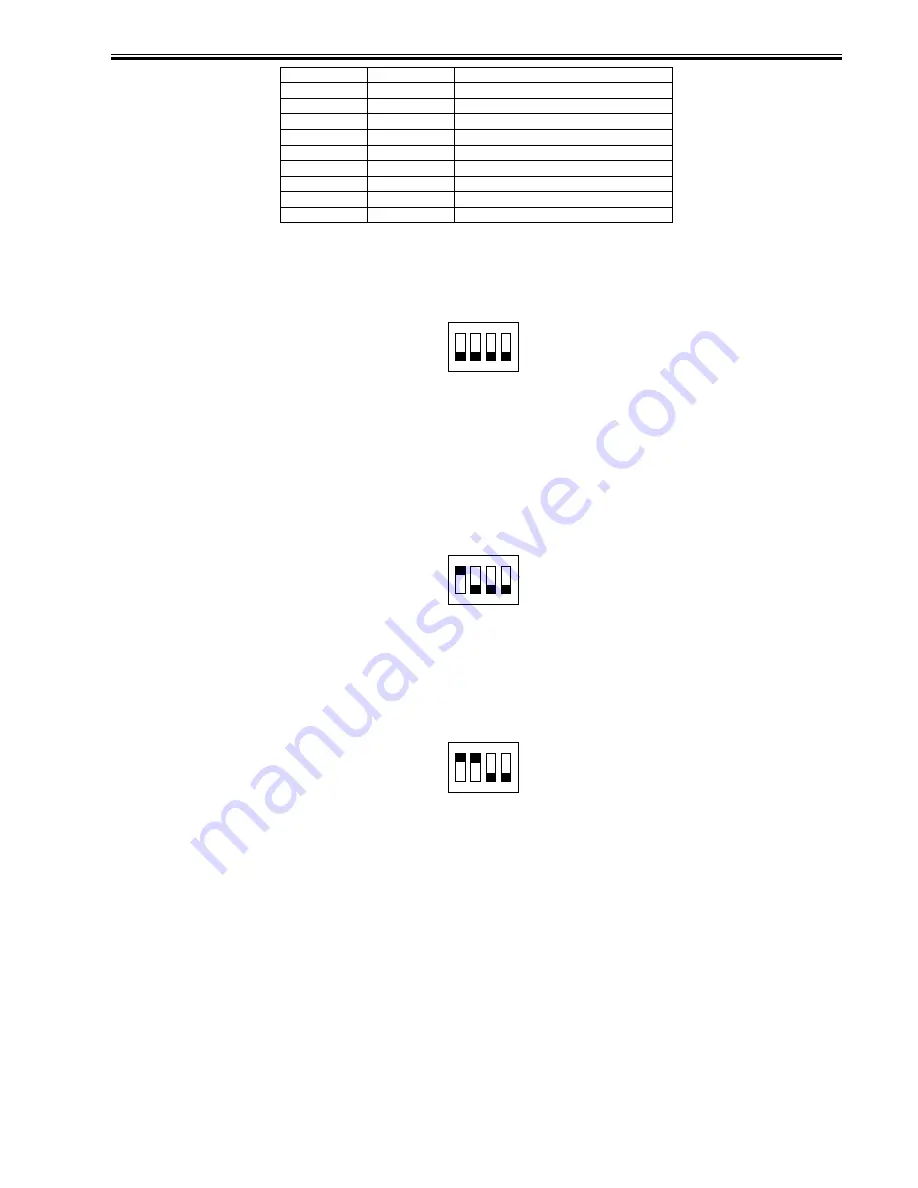
Chapter 3
9
3.2.3 Functions of the DIP Switch
0010-1713
The DipSW (SW1) function of the finisher controller PCB is as follows.
- After setting the DipSW (SW1), the check item is changed in order each time the PushSW (SW2) is pressed.
- Turn OFF all bits of the DipSW (SW1) after checking.
1.Checking operation of the stack tray unit
F-3-4
Points to check:
1) Initial operation of the stack tray is executed.
(*1) Operation differs depending on initial status
2) Initial operation of the option tray is executed. (When the option tray is attached.)
(*1) Operation differs depending on initial status
3) The stack tray moves to the bottom position (standby position at the time of replacing the offset roller).
(*1) Initial operation of the tray
- When the tray stops at the home position: The tray moves down by 20mm. Then, the tray moves back to the home position with a press of the PushSW (SW2).
- When the tray stops at other than the home position: The tray moves to the home position.
2.Non-paper aging
F-3-5
Points to check:
1) The stack tray moves to the home position, and initial operations of the stack delivery slider and offset roller are executed.
2) After the feeder motor is driven in the feeding direction, copying is executed with the following conditions: Shift mode, 2 sheets in A4 size, 4 sets (8 copies in
total)
3) The copying operation ends.
3.Checking operation of the feeder unit
F-3-6
Points to check:
1) The pickup solenoid is turned ON.
(*1) Operation differs depending on initial status
2) The feeder motor is driven at 137mm/s in the feeding direction.
3) The speed of the feeder motor is increased to 230mm/s.
4) The speed of the feeder motor is increased to 600mm/s.
5) The feeder motor is driven by 50mm in the feeding direction, and stops.
6) The feeder motor is driven by 40mm in the backward direction, and stops.
7) The feeder motor is driven at 230mm/s in the backward direction.
8) The feeder motor stops.
9) The pickup solenoid is turned OFF.
10) Shutter closing operation (When the option tray is set.)
11)Shutter opening operation (When the option tray is set.)
(*1) When the option tray is attached.
- The shutter is closed: The steps to open the shutter are performed.
- The shutter is opened: The stack delivery slider moves to the tray switching position.
After either of the action above, the step 1) is performed.
(*1) When the option tray is not attached.
- The stack delivery slider moves to the tray switching position.
After the action above, the step 1) is performed.
4.Checking operation of the adjustment unit
J908
M3
stack feed motor
J909
M4
offset motor
J910
SL1
paper retainer solenoid
J911
SL2
offset solenoid
J912
-
stapler
J913
M5
stapler motor
J914
-
front cover safety switch
J915
-
option tray
J916
CL1
shutter clutch
J917
PI15
shutter open/closed sensor
ON
1
2
3
4
ON
1
2
3
4
ON
1
2
3
4
Summary of Contents for Finisher-U1
Page 1: ...Sep 14 2005 Portable Manual Finisher Sorter DeliveryTray Finisher U1 ...
Page 2: ......
Page 6: ......
Page 8: ......
Page 10: ......
Page 22: ......
Page 23: ...Sep 14 2005 ...
Page 24: ......