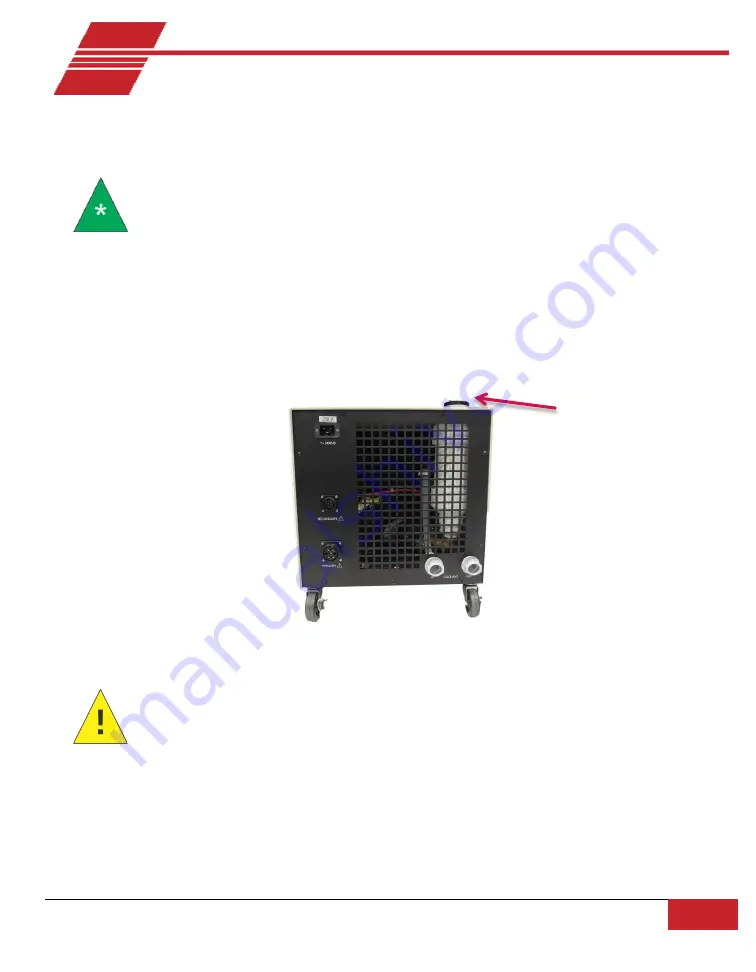
CANNON Instrument Company | TE-BBR System Preparation & Maintenance
19
TE-BBR System Preparation & Maintenance
Note:
Complete the TE-BBR assembly before beginning procedures in this
section.
Fill the Air/Water Heat Exchanger
Obtain a supply of quality ethylene glycol (automotive antifreeze) and mix it with water in a ratio of
30 percent ethylene glycol to 70 percent water. After the Exchanger tubing connections are secured
(see section Tubing Connections), pour the mixture into the reservoir opening on the top of the
Air/Water Heat Exchanger until it is full (approximately 1-2 liters). Refer to Figure 13.
Figure 13: Air/Water Heat Exchanger Reservoir
Caution:
Replace water/anitfreeze mixture annually to ensure reliable
performance and prevention of corrosion of internal components. Ethylene
glycol is a toxic substance. Use proper safety measures when handling. Follow
appropriate (M)SDS procedures.
Do not use "environmentally friendly” alternatives to ethylene glycol (such as polyethylene glycol) in
the heat exchanger. Such products can coagulate under colder conditions and damage the TE-BBR
circulation system.
Reservoir
Summary of Contents for TE-BBR
Page 1: ...Instruction Operation Manual 44 0991 Thermo Electric Bending Beam Rheometer TE BBR ...
Page 2: ......
Page 10: ......
Page 11: ......
Page 44: ...CANNON Instrument Company Software Menu Options 33 Figure 17 Toolbar Options ...
Page 47: ...36 TE BBR Instruction and Operation Manual Figure 18 Mold Specimen Diagram ...
Page 70: ...CANNON Instrument Company Troubleshooting 59 Figure 25 Diagram A new Figure 26 Diagram B old ...
Page 85: ...74 TE BBR Instruction and Operation Manual Figure 31 Graph View ...