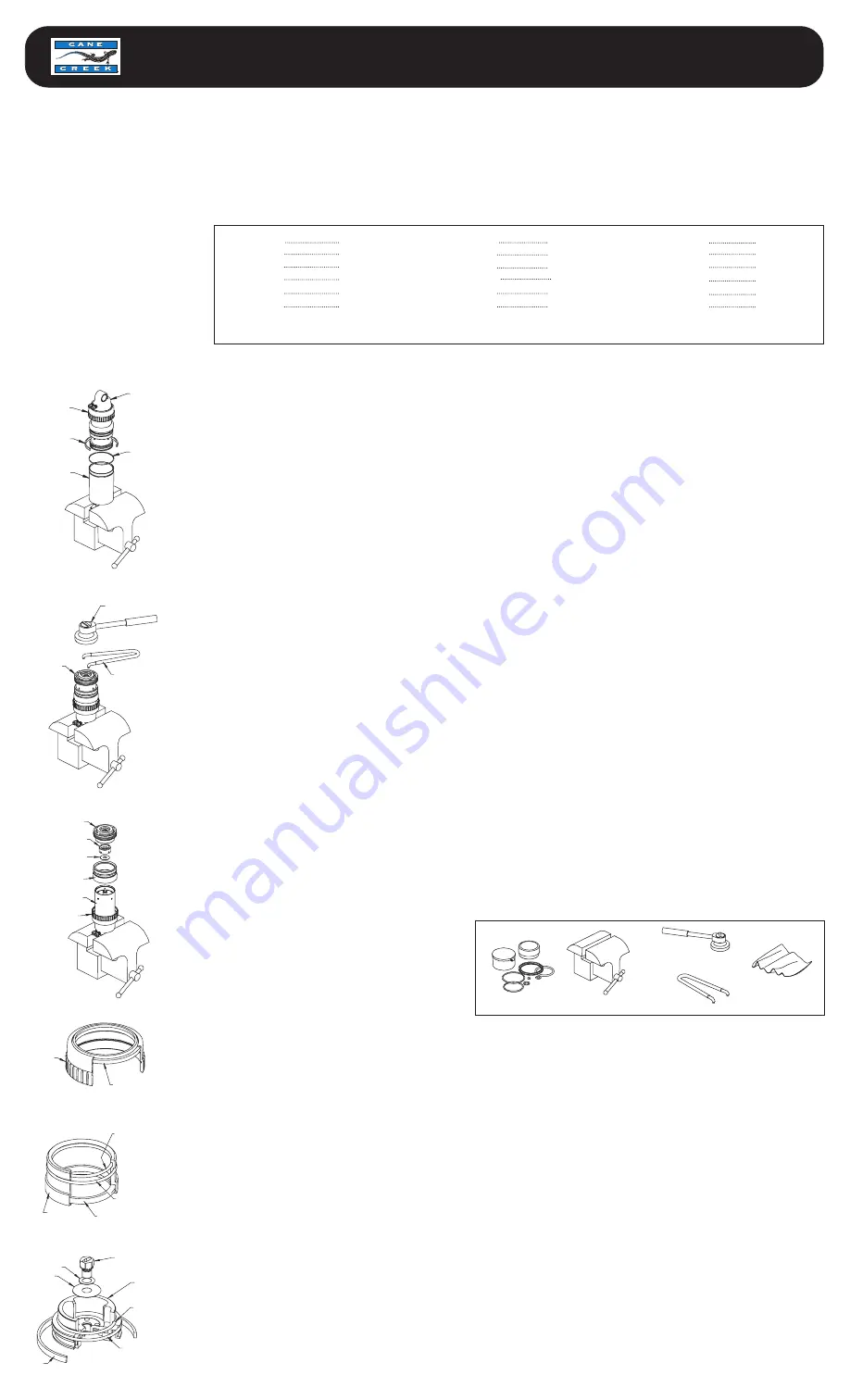
AD-12 Shock Instructions
Rider’s Weight
Shock Pressure
Rider’s Weight
Shock Pressure
Rider’s Weight
Shock Pressure
lbs. (kilos)
psi (bars*)
lbs. (kilos)
psi (bars*)
lbs. (kilos)
psi (bars*)
100 (45)
110 (7.6)
150 (68)
160 (11.0)
200 (91)
210 (14.5)
110 (50)
120 (8.3)
160 (73)
170 (11.7)
210 (95)
220 (15.2)
120 (54)
130 (9.0)
170 (77)
180 (12.4)
220 (100)
230 (15.9)
130 (59)
140 (9.7)
180 (82)
190 (13.1)
230 (104)
240 (16.5)
140 (64)
150 (10.3)
190 (86)
200 (13.8)
240 (109)
250 (17.2)
* 100 kPa = 1 bar
The Cane Creek AD-12 rear shock is a combined spring and damper system for rear suspension mountain bikes. The shock utilizes pressur-
ized air as both the springing and damping medium. The unit is typically filled with air to a pressure between 70 and 250 psi (4.8 - 17.2 bar),
depending on the weight and preferences of the rider as well as the design of the bicycle suspension. The springing system is like a
conventional air spring, where the spring force is generated by reducing the volume of the pressurized air chamber, thereby increasing its
internal pressure. The damping forces are generated by flowing the pressurized air into and out of several internal chambers through
valves as the shock is compressed and extended. On the AD-12, this valving can be tuned precisely by simply turning the two adjuster
knobs near the end of the
shock. The system also
incorporates a negative
spring air chamber which
assists the initial travel and
provides very smooth
performance.
Setup and Adjustments:
The springing and damping characteristics of the AD-12 shock are controlled by air pressure. The air pressure
is set based on the weight of the rider and the desired performance characteristics. Pressure is controlled with
a standard shock pump, which should be capable of over 200 psi (13.8 bar) and have a pressure gauge. The
shock should be inflated as indicated on the following chart. After some riding, this initial pressure setting can
be adjusted up or down to suit the rider’s preferences. Reduced pressure will provide a smoother, more “plush”
ride, but with a greater tendency to bottomout. Increased pressure will give a firmer ride with somewhat
quicker rebound. The adjuster knobs, located on the small end of the shock, provide independent control of
the compression and rebound damping characteristics. As indicated on the shock’s decal, turning the knobs
clockwise will increase the damping. Increased compression damping will decrease the shock’s travel
in reaction to a bump. Decreasing the compression damping will make the shock “softer” and more likely to
use the full stroke in absorbing a hit. By increasing the rebound damping, the shock will extend more slowly
after compressing, while decreasing this damping will make it rebound quickly. If you feel increased resistance
to turning an adjuster knob, you have reached the end of the adjustment range (these knobs are fully ex-
tended when four lines are visible under the head). Forcefully turning the knob farther will cause damage.
ATTENTION: Use a metal cap with seal to prevent leakage of air from the valve. Inflate or deflate shock
only while it is installed on the bike.
Recommended Pressure Settings:
In general, the shock should initially be pressurized according to the table below. Some bikes require much
different settings and the bike’s owners manual should be consulted if your bike came with an AD-12 as
original equipment.
Recommended Maintenance:
Proper care for the AD-12 rear shock includes checking the pressure periodically (some air will be lost when-
ever the pressure is checked), keeping the shaft and exposed wiper seal clean, and occasionally lubricating the
seals. Lubricating the seals is a fairly simple process requiring only a few simple tools, and is recommended
after approximately 200 hours of use.
Servicing the AD-12:
Section A: Shock Disassembly and Seal Replacement
For periodic maintenance or if the shock is not
holding pressure, it can be disassembled and
serviced easily. If the shock is losing pressure,
apply soapy water to the exterior of the shock
prior to disassembly. Bubbles will indicate a
leak’s location. We recommend ordering a seal
kit before opening the shock. The kit contains
the seals and grease required to properly
rebuild the shock. Call a Cane Creek technical service representative at 800-234-2725.
1. Deflate the shock and clamp the valve end of the shock in a soft-jawed vice, being careful not to damage
the shock’s eyelet (Figure 1).
2. Unscrew the lock ring in the middle of the shock. DO NOT USE TOOLS (pliers, vice grips, etc.) Wrapping a
cloth or large rubber band around the ring will improve your grip.
3. Carefully pull the piston shaft out of the large cylinder. The glide ring (Figure 6) will fall off the piston as it
exits the large cylinder. Prevent contamination of the seals by keeping all parts
clean and free of dirt. DO NOT remove the black and silver adjustment screws. Doing so will damage the
internal mechanism of the shock.
4. Clamp the piston shaft eyelet in the vice, and use a spanner wrench or socket wrench with special spanner
head (available from Cane Creek) to unscrew and remove the piston (Figure 2). Be careful not to lose the
compression cylinder and compression shim (Figure 3).
5. Now remove the seal bushing from the piston shaft by sliding it off the open end of the shaft (Figure 3). The
lock ring can also be removed and the rod wiper can be replaced (Figure 4).
6. Remove seals shown in Figure 5 and 6 (be very careful not to scratch the seal grooves while removing the
seals). Wipe all the surfaces using a clean lint-free cloth (Do not use solvent). Liberally apply Cane Creek De-
friction Lube to the seal grooves and the new seals. Install the seals as shown in Figure 5 and 6. Note: The
AD0303 seal is slightly harder than the AD0108.
7. In order to modify the shock’s volume set-up, or if the “soapy water” test revealed a leak around the bushing
(AD0127) on the piston shaft eyelet, then the volume adjustment plate must be removed. This is described in
or
Soft-jawed
Vice
3mm Spanner
Wrench
Lint-free
Cloth
Seal Kit
Socket Wrench
With Spanner
Required Tools:
piston
shaft
lock
ring
large
cylinder
wire
ring
Figure 1
glide
ring
spanner
wrench
piston
Figure 2
socket wren
spanner
or
piston
compression
cylinder
compression
shim
seal
bushing
piston
shaft
lock
ring
Figure 3
lock
ng
rod wiper
Figure 4
quad seal
AD0301
o-ring seal
AD0108
o-ring seal
AD0108
Figure 5
seal
bushing
o-ring
seal
AD0303
o-ring
seal
AD0302
valve
screw
washer
valve
shim
piston
glide
ring
Figure 6