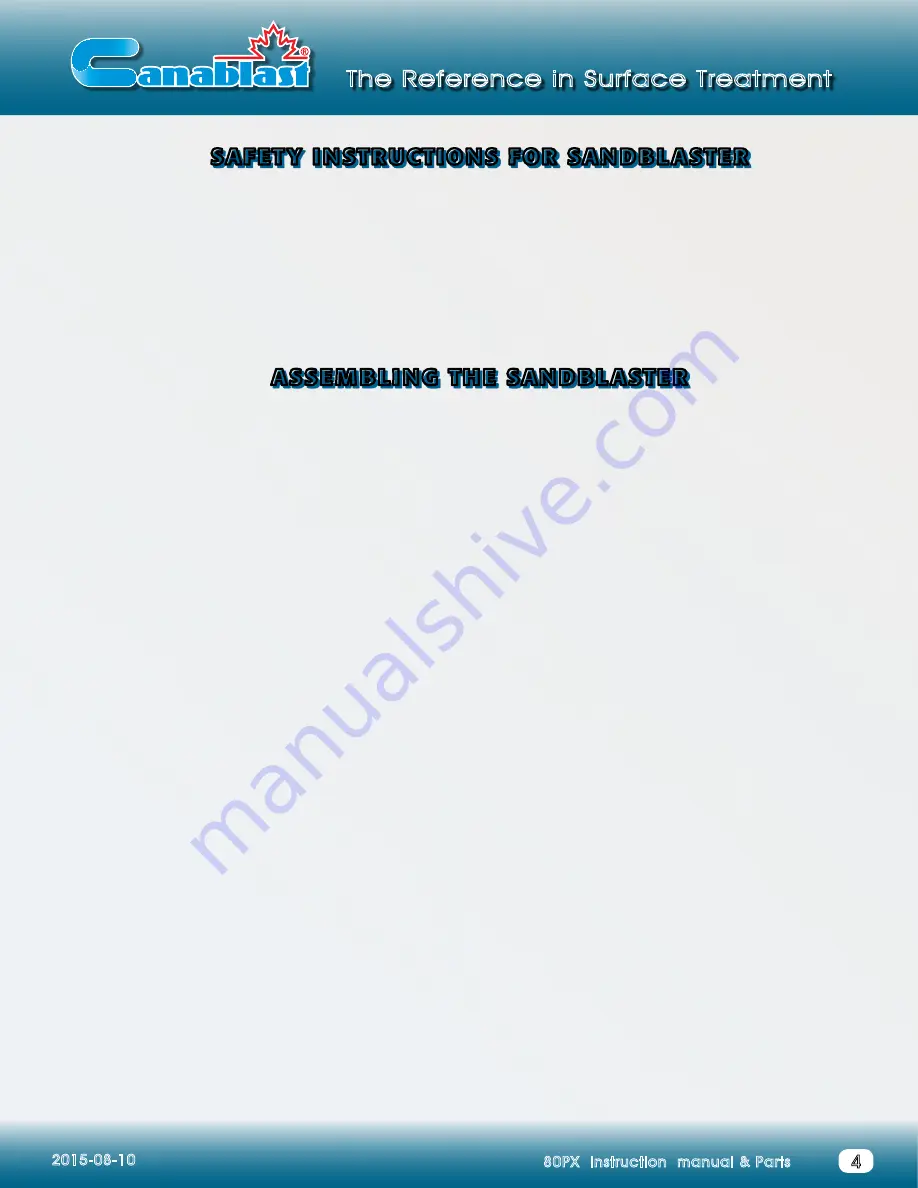
4
2015-08-10
The Reference in Surface Treatment
80PX Instruction manual & Parts
1. BEFORE OPENING THE TANK,
release the air pressure on the sand tank. To do this, turn off the air
supply valve (14), to release pressure in the line. Ensure that the tank pressure gauge (05) reads zero,
then open the tank.
2. MAINTAIN CORRECT AIR PRESSURE.
Pressure should not exceed 125 PSI. If it does, the safety valve
(06), is supposed to release the excess pressure. If this doesn’t happen, stop all work immediately, and
use the air compressor to reduce the excess pressure. Do not investigate the sandblaster’s pressure
problem until the pressure gauge (05) reads zero.
1. Refer to the drawing for step 1, to assemble the intake manifold (08). First, attach the pressure gauge
(05) to the top intake manifold, turning the gauge so that is can be seen across the top of the tank.
Next, attach the throttling valve (18) to the bottom of the manifold. Attach the nipple connector (7A),
to the throttling valve. Attach the joint pipe (07), to the manifold.
2. Refer to the drawing for step 2, to assemble the water trap filter (12). Two nipple connectors (07)
are screwed into each side of the filter. On one side, attach the air supply valve (14), to the nipple
connector (7), and then attach the male/female connector (15), to the other side of the air supply valve.
When you’re ready to operate the sandblaster, the air hose from the compressor will fasten to the male/
female connector (15).
3. Place the tank (03) on a table with the four clips up. Refer to the drawing for step 3. Screw the water
trap filter (12) and its parts into the hole at the side of the intake manifold. Then screw the open end of
the joint pipe (07) with intake manifold (08) and pressure gauge (05) attached into the threaded hole
on the side of the filler pipe on top of the tank. Again, be sure that the manifold and gauge are vertical.
4. Refer to the drawing for step 4, assembly of the sand outlet valve into the hole at the bottom of the
tank. Attach four parts, in order: Nipple connector (07), sand metering valve (18), nipple connector
(07) and the sand outlet pipe (19).
5. Refer to the drawing for step 5, for connecting the sand metering valve assembly (step 4). Slide the
two hose clamps (26), over each end of the sand hose (25). Press one end of the hose over the nipple
on the sand outlet pipe (19), and the other end over the nozzle coupling (27). Both hose ends should
be firmly seated on the nipples. Slide the hose clamps along the hose to each nipple and tighten the
clamps very firmly. They have to resist the force of 65 to 125 PSI.
6. Fasten the handlebars (02) to the tank using pan screws (11) and washers (10) and hex nuts (09). Note:
keep the handle curve ends upward.
7. Install the axle foots (20) on the tank using the screws (16). Locate the axle (23) and slide it through the
holes in the slides of the axle foots (20). Place one wheel (22) at each end of the axle and fasten them
into place with cotter pins (24) and washer (21).
8. 8. Insert the fixed foot (17) onto fitting on bottom of the tank near the edge. Use your last cotter pin
(24) to hold the foot to the tank.
9. 9. Before beginning operations, go back over each connection, double checking to ensure that all tight
and properly sealed.
SAFETY I NSTRUCTIONS FOR SAN DBLASTER
ASSEM BLI NG TH E SAN DBLASTER