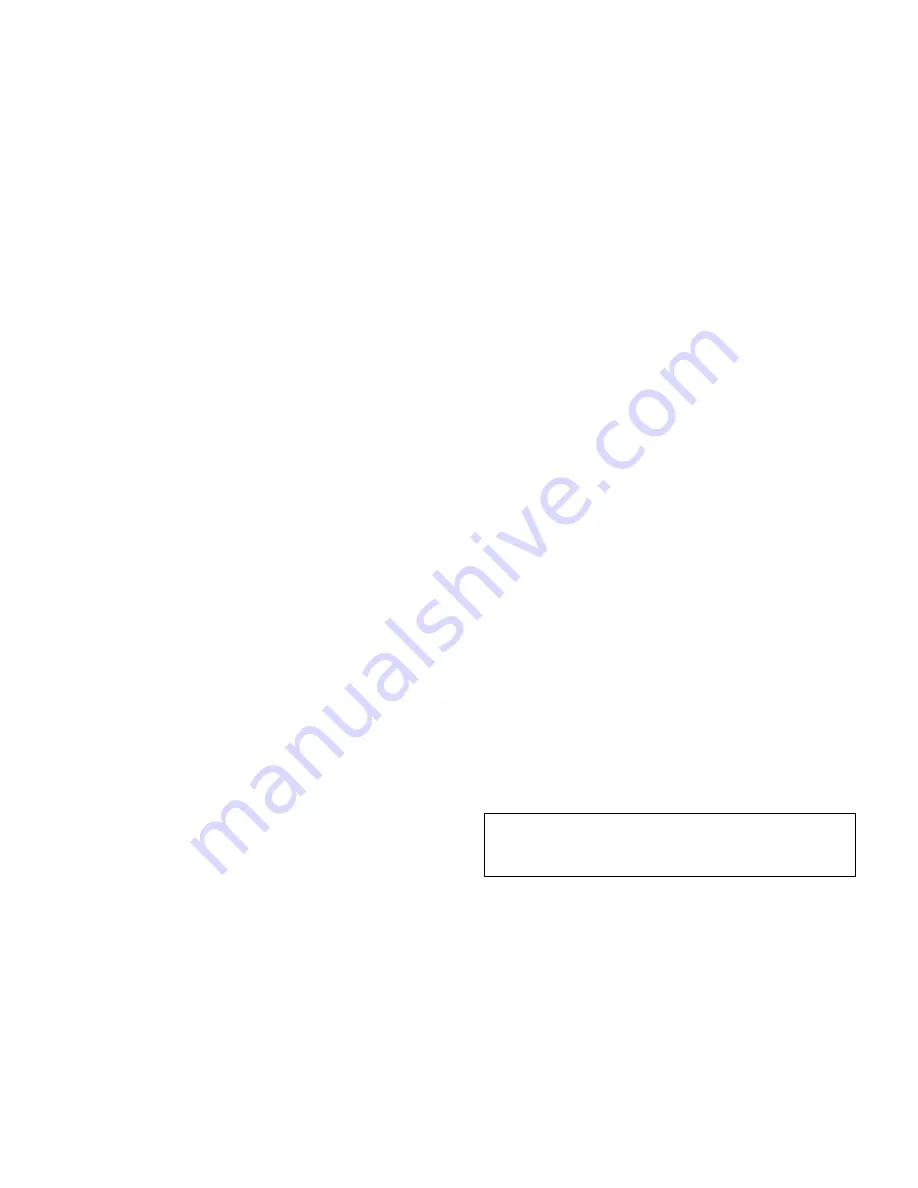
51
pump will run for a period of time until the programmed
delta T between inlet and outlet is reached, after the
temperature set point is satisfied. This will remove any
residual heat from the combustion chamber before turning
the pump off. See wiring diagram shipped with the unit.
11.5
SUMMARY
a) Typical Boiler Installations
General Plumbing Rules
1
Check all local codes.
2
For serviceability of boiler, always install
unions.
3
Always pipe pressure relief valve to an open
drain.
4
Locate system air vents at highest point of
system.
5
Expansion tank must be installed near the
boiler and on the suction side of the system
pump.
6
Support all water piping.
b) Placing the Boiler in Operation
Pre-Start Check List
1
Review the location of the boiler, clearances
from combustible surfaces and available service
clearances.
2
Review Part 2 Venting. Ensure that all vent
components are fabricated from the correct
category of materials with adequate clearance
from combustibles.
3
Ensure that the boiler condensate drain and all
vent system condensate drains are properly
routed to an acceptable floor drain or
neutralization system.
4
Review the vent termination point for proper
location and clearances.
5
Ensure that proper volumes of combustion and
ventilation air are provided to the mechanical
room. If a separate combustion air pipe is used,
ensure that it is properly sized, sealed and
terminated.
6
Review the water piping from the boiler to the
system. The boiler must be installed in a
primary/ secondary piping system. Review the
diameter and equivalent length of the installed
piping to and from the boiler to ensure proper
flow.
7
Ensure that a properly sized primary system
pump is installed with an expansion tank.
8
Check system pressure. Ensure a minimum of
30 PSIG with the system hot and not more than
90% of the rated pressure of the relief valve.
9
Review the installed gas piping from the meter
to the boiler. Ensure that the gas pipe, meter
and any regulators are adequately sized.
10 Review the field wiring and electrical service for
both the boiler controls and pump. Ensure that
the electrical service(s) is adequately sized.
Boiler Set-Up
1
Ensure that the boiler and piping system are
full of water. Bleed all air from the pump
housing and secondary loop.
2
Check system for any water leaks.
3
Check system for installation of glycol or
water treatment where required. Where glycol
has been used to maintain the temperature
rise across the appliance confirm that the
recommended flow for pure water has been
increased by 15% and the head loss by 20%.
4
Turn on power to the primary system pump
and the appliance secondary pump and verify
operation.
Boiler Operational Checks
1
Turn the boiler main power switch to the “ON”
position.
2
Verify operation of the Fuji and Diagnostic
Display.
3
Program the adjustable points.
4
Turn the switch to the “ON” position to start
boiler operation.
5
Push the resets for low water level, high water
temperature and flame failure.
6
Install a manometer on the gas supply to the
boiler and verify minimum gas supply
pressure as the burner fires at 100% of rated
input.
7
Verify operation of safeties as necessary (low
water cut-off, high limit, gas pressure, etc.).
Boiler Operation
1
Appliance should begin the start-up process
for the sequence of operation.
2
The boiler will fire down to 20% for
condensing and near-condensing appliances
and 35% for non-condensing appliances on
initial start-up and adjust input as required to
meet system demand.
3
Ensure that inlet water temperature does not
fall below 115°F (46°C) for non-condensing
and 130
o
F (55
o
C) for condensing and near-
condensing.
4
Based on system demand, the appliance will
modulate accordingly.
5
As system demand is satisfied, the burner will
cycle off and the combustion air fan will
decelerate at a pre-programmed rate before
the appliance shuts down.
11.6
DOMESTIC HOT WATER HEATER
Hot water heaters are designed for installation with a
storage tank. The operation of the properly sized circulating
pump, the piping between the tank and heater and the
control of water velocity, as explained below, are important
for correct operation of your hot water heater.
11.7
WATER VELOCITY CONTROL
To ensure proper velocity through the heat exchanger(s), it
is necessary to select the proper pump. Temperature rise
at full fire will be an indication of flow. This must be done
on initial installation and periodically rechecked.
Excessive lime/scale build-up in the heat exchanger tubes
is a result of restricted flow and too little velocity in the
tubes. Excessive pitting or erosion in the tube is caused by
high water flow and too much velocity through the tubes.
Care should be taken to maintain required water velocity
based on water condition as follows:
11.8
TEMPERATURE RISE AT FULL FIRING
RATE
1
The pump must run continuously when the burner is
firing.
2
With the pump running and the burner in the water
heater or hot water supply boiler in the off cycle, the
Return/Inlet temperature and Supply/Outlet
Summary of Contents for DynaFlame DFW501
Page 2: ......
Page 12: ...7 Table 4 Appliance Dimensions and Specifications Table 5 Vent Sizes for a Single Appliance...
Page 58: ...53 PART 12 EXPLODED VIEW...
Page 59: ...54...
Page 60: ...55...
Page 66: ...61 PART 13 ELECTRICAL DIAGRAMS...
Page 67: ...62...
Page 68: ...63 Camus DynaFlame PCB Electrical Ladder Diagram...