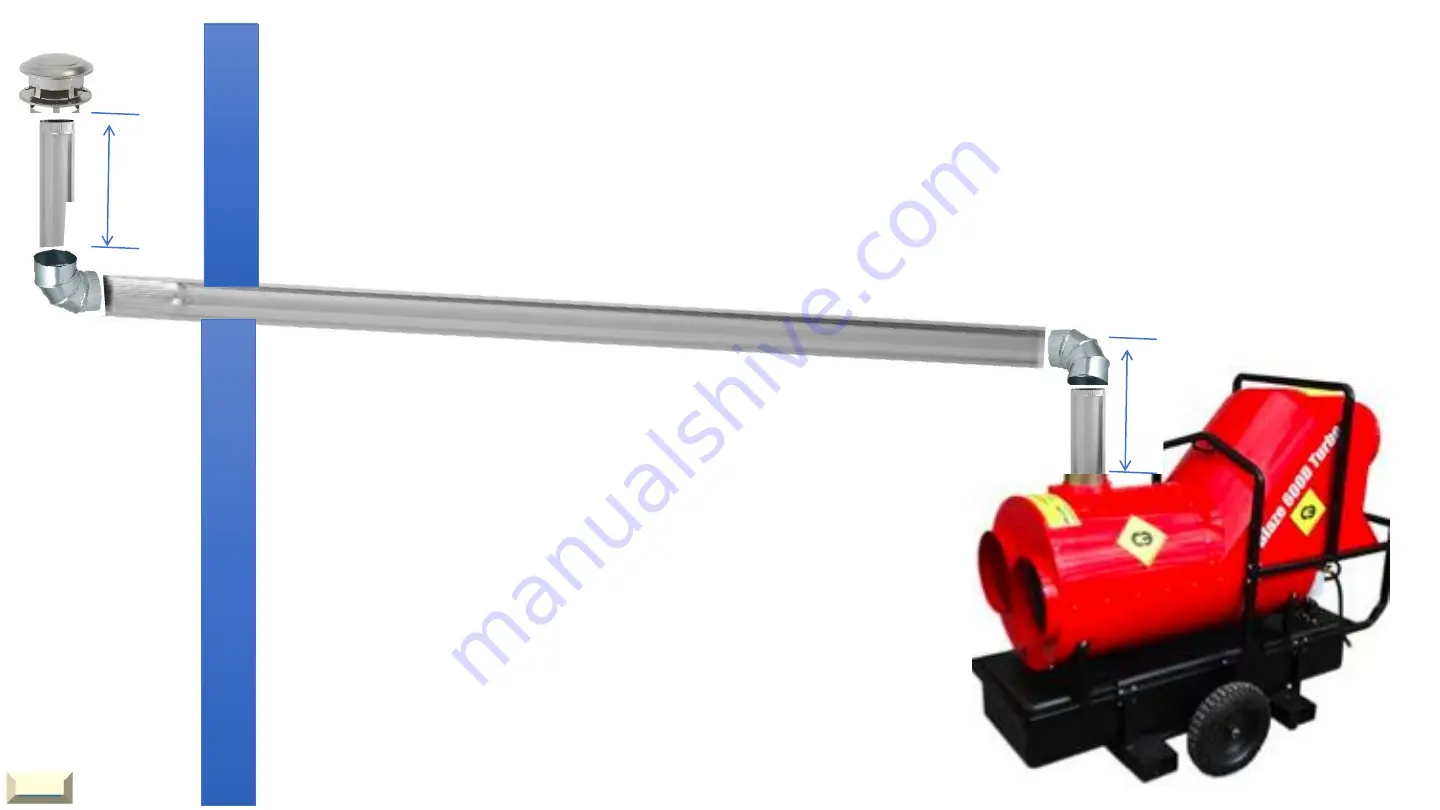
36”
Best practices for venting when heater is located inside a building
•
Avoid using as many 90-degree elbows as possible
•
Venting runs should be as short as possible
•
Vertical rise minimum 3 feet, 5 feet is better outside the building.
•
Always install a rain cap.
•
Never decrease diameter of flue piping.
•
Horizontal runs ¼” per foot rise.
•
Make sure all piping is properly secured.
•
Make sure there is no negative pressure inside
the building where the heater is placed.
➢
Note:
where the vent pipe passes through
a combustible wall a fire proof thimble
must be used.
40
36”