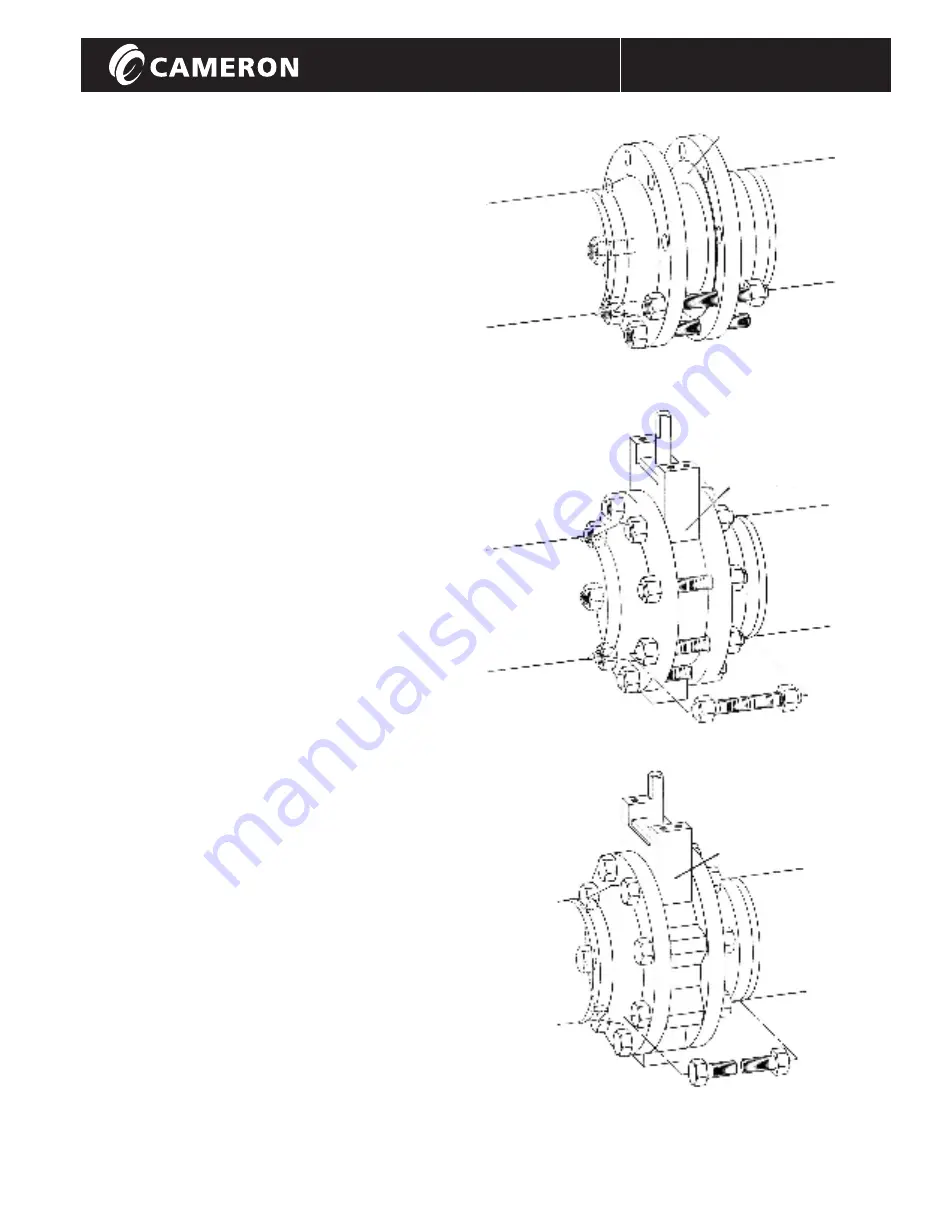
7
Installation, Operation and Maintenance Manual
D I S T R I B U T E D V A L V E S
Procedure
Raised Face
Area
Wafer Body
Lug Body
The following procedure applies to new
installation between standard ASME B16.5
pipe flanges.
When replacing a valve from an existing
installation, clean the flange faces of any
residual gasket material before starting.
Actuation should not be removed from the
valve for installations unless the actuator
must be transferred during replacement.
1.
Remove protective covers from valve.
Be sure valve is completely closed.
2.
When installing wafer body valves,
install lower flange bolts without
tightening (Figure 10). Position valve
and flange gaskets between flanges,
within the pocket formed by the flange
bolts. Install the remaining flange
bolts, taking care that the gaskets are
centered on the flange faces (Figure 11).
Note: While the WKM
MA High Performance Butterfly
Valve has bi-directional sealing
capabilities, the preferred position
is seat upstream (Figure 4).
Handle operated valves or fail close
valves should be installed seat
downstream (stem side facing flow).
3.
Lug body valves should be positioned
between the flanges with gaskets
properly centered and then the
capscrews inserted (Figure 12).
4.
Carefully check disc clearance by
placing the valve in the full open
position. Should automated valves be
difficult or impossible to cycle, check
that the raised face of the flange
matches the raised area on the valve
face.
5.
Tighten all bolts or capscrews in a
crossover or star pattern to insure
even sealing (Figures 11 and 12).
6.
Packing gland tightness is pre-tested
at the factory. Should stem leakage
occur at start-up, the gland can be
adjusted to stop the leak.
Avoid over tightening which may
result in excessive operating torque
or premature packing wear.
DynaCentric
Figure 10
Figure 11
Figure 12
WKM-MA-HPBV-IOM