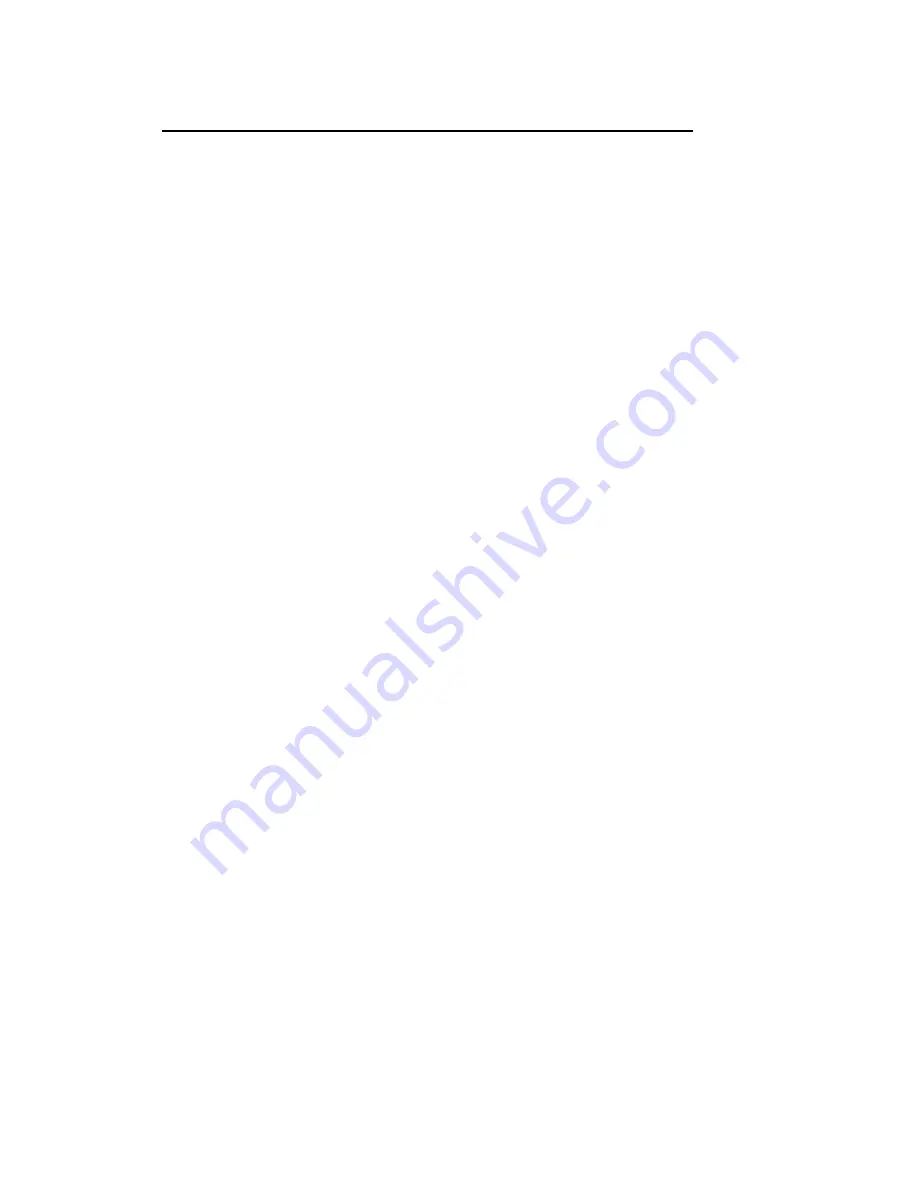
CLEAN AIR MANAGEMENT COMPANY, INC.
8224 Nieman Road
i
Lenexa, Kansas 66214 Phone: 913-831-0740 Fax: 913-831-9271
ON SITE STORAGE RECOMMENDATIONS (continued)
IX. Butterfly (Wafer Valve)
1. All limit switches, solenoids, and air cylinder ports must be capped and taped to
prevent any moisture or dirt from entering.
2. Unit can be stored outside provided it is covered with a tarp and is on a pallet or
skid to keep it out of the water and dirt and sunlight.
X.
Level Indicators
Store these items inside a cool dry area protected from rodents
XI. AC Inverters
Store these items and all other electrical controls inside a cool dry area protected
from rodents.
4-3