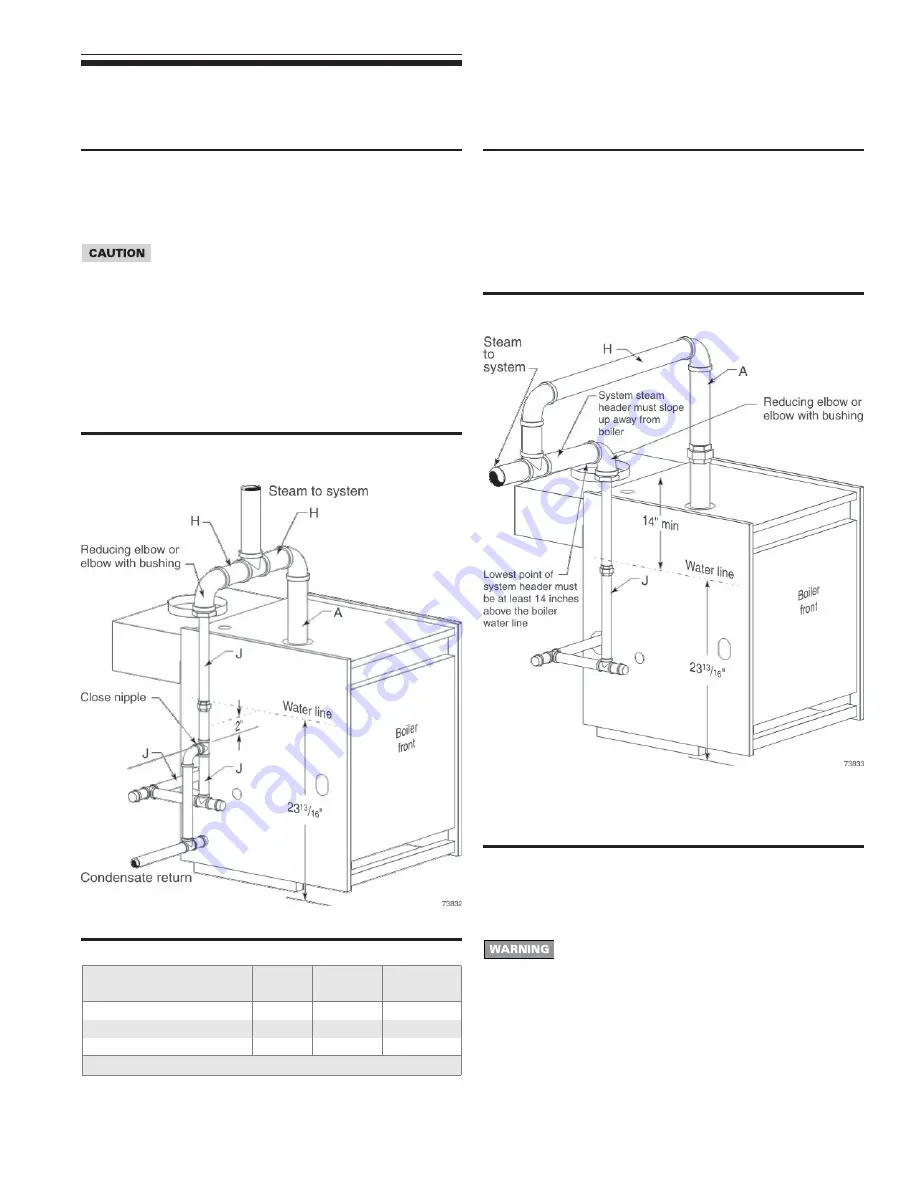
GSA
Gas-Fired Steam Boilers –
Boiler Manual
9
Part Number 550-110-738/0703
General
3
Install piping
1.
Pipe before installing controls. Connect return piping after jacket
is attached. Connect supply piping before or after jacket is
attached.
Failure to properly pipe the boiler may result in
improper operation and damage to the boiler or
building.
2. See Figure 5 and Table 5. Pipe exactly as shown. Satisfactory
operation of a steam heating system depends on adequate
condensate return to boiler to maintain a steady water level.
Avoid adding raw makeup water. Where condensate return is
not adequate, install low water cutoff/pump control, condensate
receiver and condensate boiler feed pump. Refer to Table 7,
page 10, for sizing. See page 7, Table 4, for tapping locations.
Table 5
Recommended pipe sizing
Boiler model number
Riser (A) Header (H)
see Note
Equalizer (J)
GSA-075 and GSA-100
2"
2"
1½"
GSA-125 through GSA-175
2½"
2 ½"
1½"
GSA-200 and GSA-250
3"
3"
1½"
Note
: 24" minimum from waterline to header.
Figure 5
Recommended piping, piping for parallel-
flow systems only.
Connecting to counterflow piping
Apply the recommended piping in Figures 4 through 7 only when
connecting to a parallel-flow system. When connecting to a
counterflow system, the boiler steam supply must connect into the
top of the counterflow system header, as shown in Figure 6.
Figure 6
Connection to counterflow steam piping
Relief valve
Install relief valve in tapping on top of boiler. See Table 4, page 7,
for control tapping locations. See the tag attached to the relief valve
for manufacturer’s instructions.
Follow the steps below to avoid potential severe
personal injury, death or substantial property damage.
• When installing the relief valve, ensure that all
connections, including the valve inlet, are clean and
free from any foreign matter.
• Mount the relief valve only in the vertical position,
directly connected to the tapping designated in the
manual on top of the boiler.
• Use pipe compound sparingly, or tape, on external
threads only.
• Do not use a pipe wrench! Use proper type and size
wrench on wrench pads only.