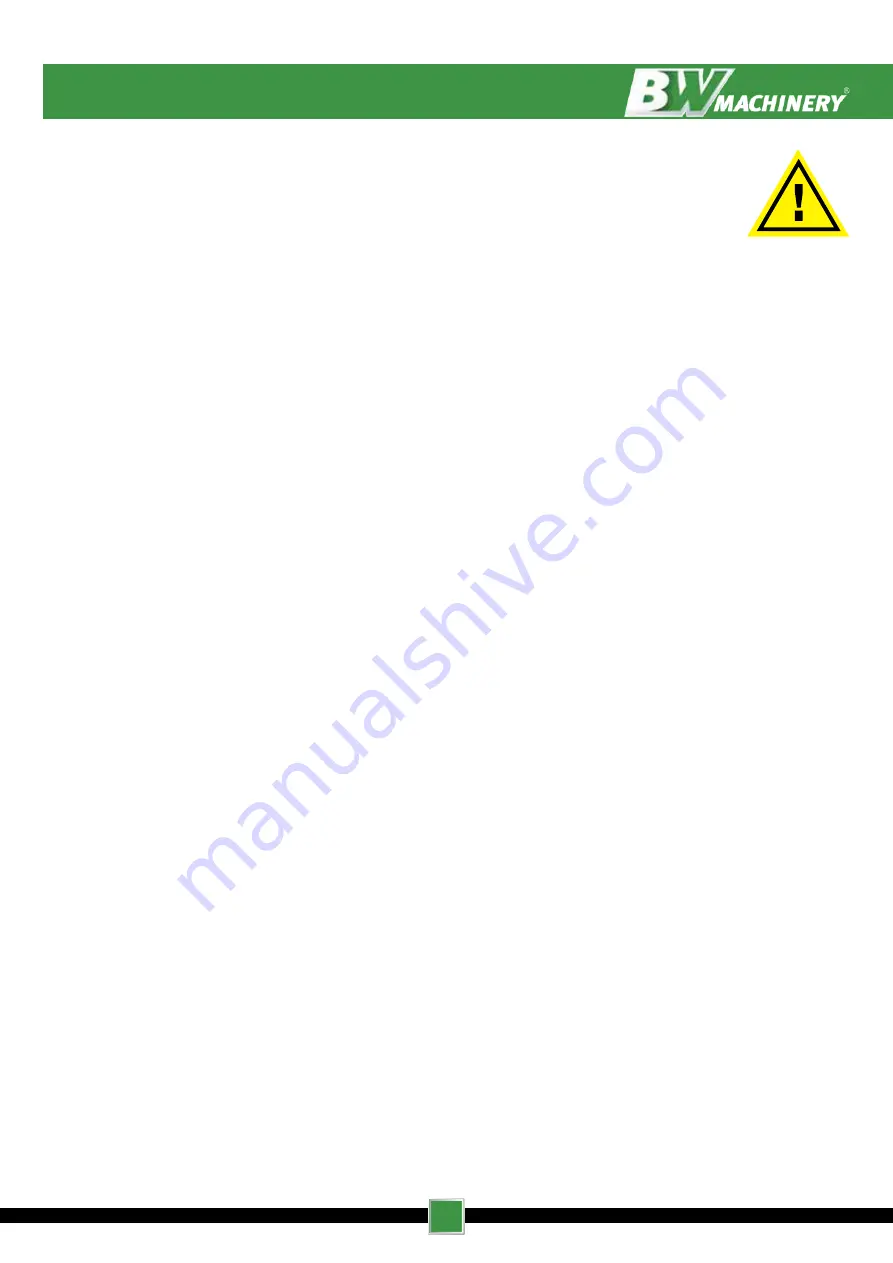
7
WARNING
REPAIRS AND MAINTENANCE
DO NOT operate the log splitter when it is in poor mechanical condition or in
need of repair. Frequently check that all nuts, bolts, screws, hydraulic fittings and
hose clamps are tight�
DO NOT alter the log splitter in any manner� Any alteration will void the warranty
and could cause the log splitter to be unsafe to operate� Perform all recommended
maintenance procedures before using the log splitter� Replace all damaged or
worn parts immediately�
DO NOT tamper with the engine to run it at excessive speeds� The maximum
engine speed is preset by the manufacturer and is within safety limits� See Briggs
& Stratton engine manual�
Remove the spark plug wire before performing any service or repair on the log
splitter�
Always check the level of hydraulic oil and engine oil before operation.
Replacement parts must meet manufacturer’s specifications.
HYDRAULIC SAFETY
The hydraulic system of the log splitter requires careful inspection along
with the mechanical parts� Be sure to replace frayed, kinked, cracked or
otherwise damaged hydraulic hoses or hydraulic components�
Check for hydraulic fluid leaks by passing a piece of paper or cardboard underneath or over the
area of the leak� Do not check for leaks with your hand. Fluid escaping from the smallest hole,
under pressure, can have enough force to penetrate the skin causing serious injury or death.
Seek professional medical attention immediately if injured by escaping hydraulic fluid.
Serious infection or reaction can develop if medical treatment is not administered immediately�
Relieve all pressure by shutting off the engine and moving the valve control handle back and forth
should it become necessary to loosen or remove any hydraulic fitting.
DO NOT remove the cap from the hydraulic tank or reservoir while the log splitter is running� The
tank could contain hot oil under pressure which could result in serious injury.
DO NOT adjust the hydraulic valve� The pressure relief valve on the log splitter is preset at the
factory� Only a qualified service technician should perform this adjustment.
Safety Information
Summary of Contents for BWMLS30
Page 27: ...27 Notes...