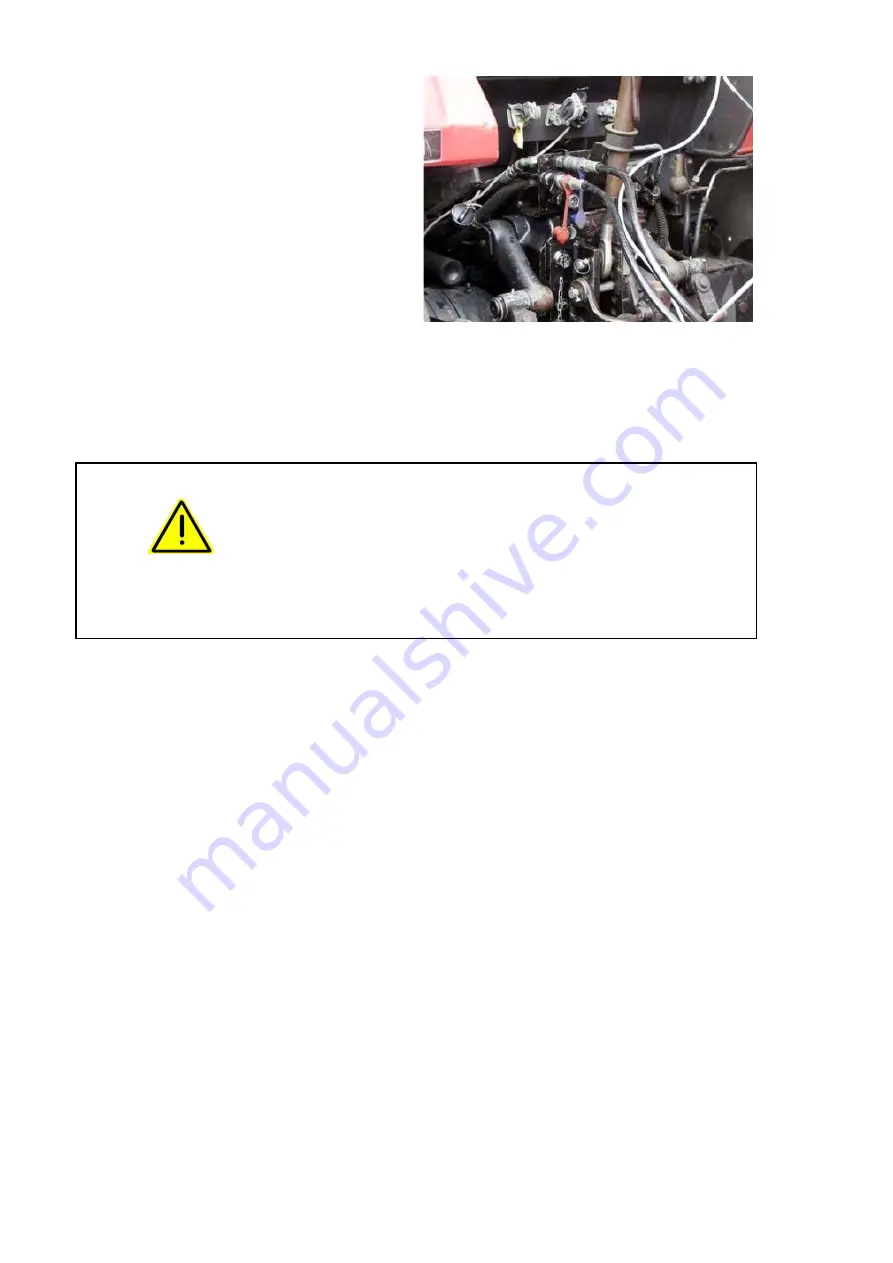
1. Always set the actuator levers / switches
on the tractor's control unit to the float
(neutral) position.
2. Remove the dust caps from the hydraulic
plugs and the hydraulic sockets.
3. If necessary, clean the hydraulic plugs of
the hydraulic hose lines as well as the
hydraulic sockets before coupling them to
one another. Make sure that no dirt can
enter the hydraulic system!
4. Couple the plugs of the hydraulic hose
lines to the hydraulic sockets. You need to
feel the plugs lock into place
4.1 Return line (blue dust cap) to the
return (T).
4.2 Pressure line (red dust cap) to the
flow (P).
Fig. 7.3-1
7.4
Uncoupling the hydraulic hose lines
WARNING
Risks to a person's health from infections may arise if hydraulic
oil escapes under high pressure and enters the body!
Before uncoupling the hydraulic hose lines, make sure that the
hydraulic system on the tractor and the accessory equipment has
been depressurized. Always set the actuators on the tractor's control
unit to the neutral position.
Seek immediate medical attention if injury from hydraulic oil has
occurred! Risk of infection!
1. Always set the actuator levers / switches on
the tractor's control unit to the neutral
position.
2. Release the hydraulic plugs and pull them
out of the hydraulic sockets.
3. Use the protective dust caps to protect the
hydraulic plugs and hydraulic sockets
against dirt.