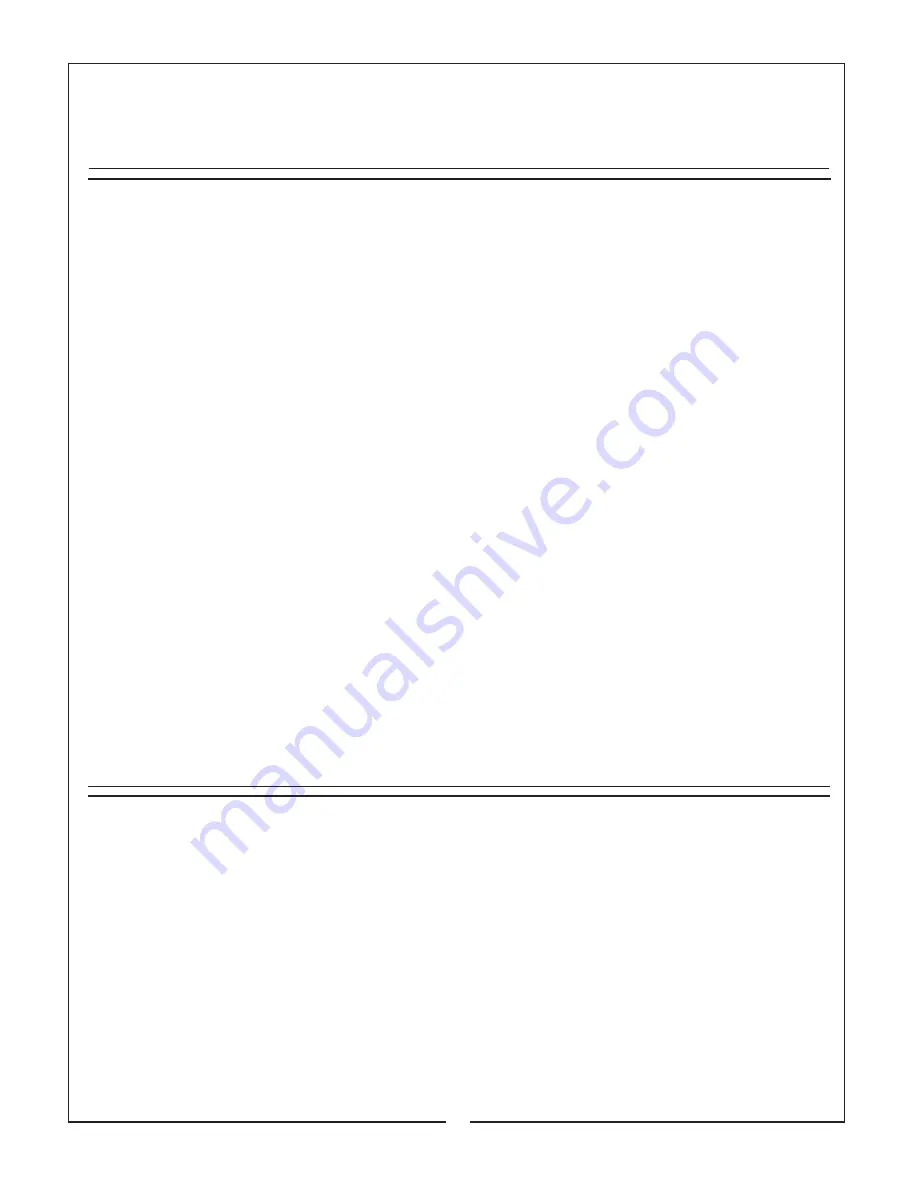
3545 / 4045 / 5045 / 6045
TABLE OF CONTENTS
SECTION/PARA
PAGE
Warranty .....................................................................2
Dealer Preparation Check List....................................3
Safety Alert Symbols ..................................................4
Safety Precautions .....................................................5
Federal Laws & Regulations.......................................7
I
INTRODUCTION & DESCRIPTION ...........................8
1-1 Introduction...........................................................8
1-2 Description ...........................................................8
II
LOADER MOUNTING & DISMOUNTING ................10
2-1 Preparing Tractors..............................................10
2-2 Mounting Loader ................................................10
2-3 Dismounting Loader ..........................................12
III
OPERATING INSTRUCTIONS ................................13
3-1 General Safety ...................................................13
3-2 Pre Operation .....................................................13
3-3 Initial Loader Operation ......................................13
3-4 External Loader and/or Tractor Valve ................14
3-5 Loader Mounted or Tractor Mounted
Single Lever Control Handle.....................................14
3-6 Loader Mounted Series Control Valve With Single
Lever Control Handle................................................14
3-7 Neutral Position ..................................................14
3-8 Float Position......................................................14
3-9 Regenerative Valve Position ..............................14
3-10 Load Sense Loader Valve ................................14
3-11 Loader Operation .............................................14
1
RETAIL CUSTOMER’S RESPONSIBILITY
UNDER THE BUSH HOG WARRANTY
It is the Retail Customer and/or Operator’s responsibility to read the Operator’s Manual, to operate, lubricate,
maintain and store the product in accordance with all instructions and safety procedures. Failure of the opera-
tor to read the Operator’s Manual is a misuse of this equipment.
It is the Retail Customer and/or Operator’s responsibility to inspect the product and to have any part(s) repaired
or replaced when continued operation would cause damage or excessive wear to other parts or cause a safety
hazard.
It is the Retail Customer’s responsibility to deliver the product to the authorized Bush Hog Dealer, from whom
he purchased it, for service or replacement of defective parts which are covered by warranty. Repairs to be
submitted for warranty consideration must be made within forty-five (45) days of failure.
It is the Retail Customer’s responsibility for any cost incurred by the Dealer for traveling to or hauling of the
product for the purpose of performing a warranty obligation or inspection.
3-12 Removing Air From Hydraulic System ...............15
3-13 Hose Identification............................................15
3-14 Bucket Level Indicator Rod ..............................15
3-15 Bale Spear Operation.......................................20
3-16 Fork Lift Operation............................................21
3-17 Transporting .....................................................21
3-18 Skid Steer Quick Hitch Operation.....................22
IV
MAINTENANCE .....................................................23
4-1 Maintenance Check List ....................................23
4-2 Lubrication .........................................................23
4-3 Hydraulic System
Pressure Requirements .....................................24
4-4 Troubleshooting .................................................24
V
ASSEMBLY ..............................................................26
5-1 Tractor Preparation ............................................26
5-2 Tractor Ballast ....................................................27
5-3 Installation ..........................................................27
5-4 Hydraulic Hookup ...............................................27
5-5 Bucket Level Indicator Rod ................................27
5-6 Fork Lift Option...................................................28
5-7 Bale Spear Option ..............................................28
5-8 Optional Bucket Items ........................................29
Torque Specifications ...............................................30
Safety Decals ...........................................................31
SECTION/PARA
PAGE
OPTIONAL EQUIPMENT INSTRUCTIONS AT END OF MANUAL
NOTE: Some optional equipment information may not apply to your particular loader.