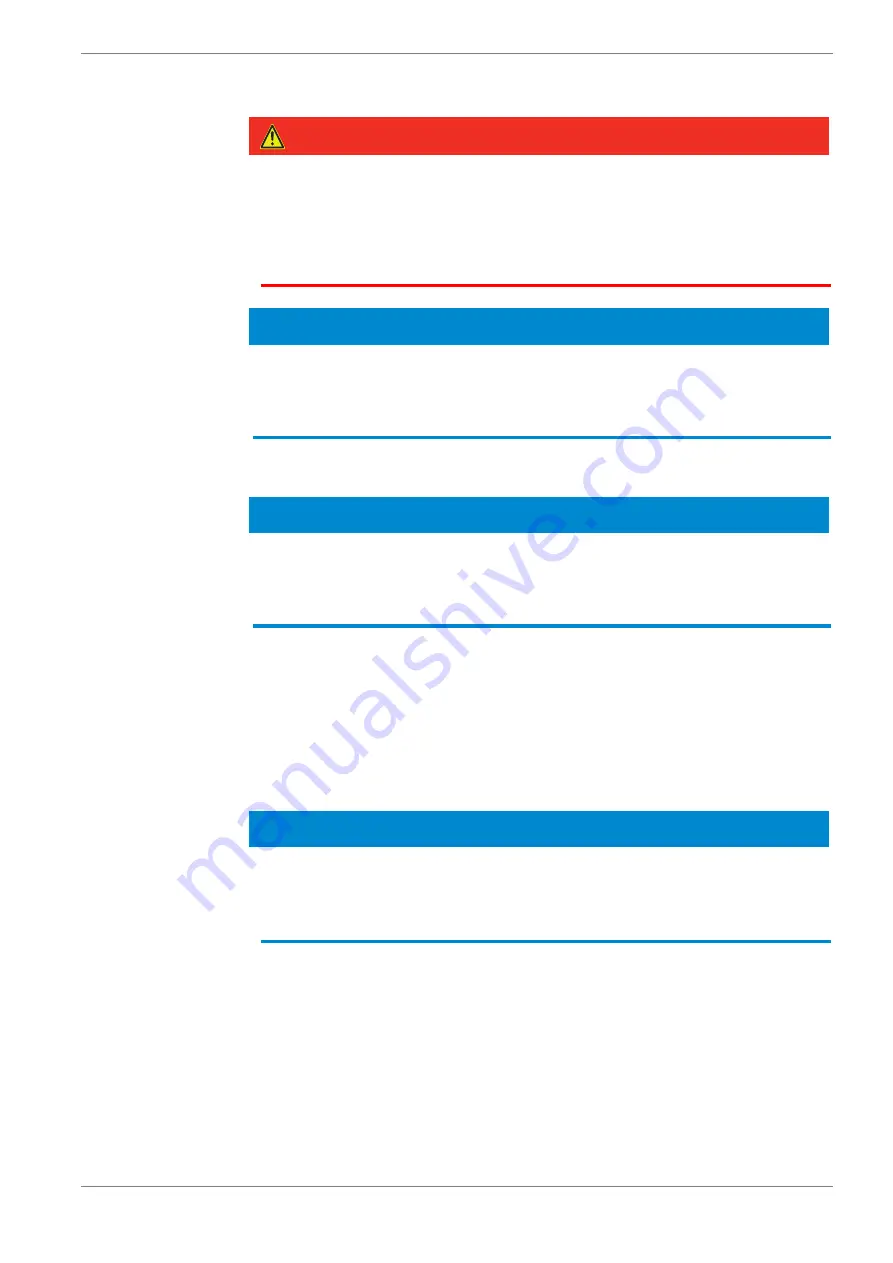
6
|
Installation
0870169324
_VD
0025
‐
0100G_
‐
0006_IM_en
17
/
46
6.3
Electrical
connection
DANGER
Danger
from
electric
shock!
Electric
shock
will
cause
death
or
serious
injury.
•
All
live
lines
must
be
powered
down
before
the
electrical
installation!
•
Before
any
electrical
work,
ensure
that
the
vacuum
pump
is
disconnected
from
the
power
supply
and
secured
against
accidental
activation.
•
Electrical
installation
work
must
only
be
performed
by
trained
specialists.
ATTENTION!
Incorrect
rotation
of
drive
motors
can
seriously
damage
the
vacuum
system!
Switch
vacuum
pumps
briefly
on
and
off
again
to
check
the
rotational
direction
of
the
motor.
The
rotational
direction
is
marked
by
a
direction
of
rotation
arrow
on
the
motor.
If
the
direction
is
wrong,
reverse
two
connection
phase
poles.
6.3.1
Connection
of
the
power
supply
ATTENTION!
Danger
of
damage
to
the
vacuum
system.
Wrong
connection.
Wire
the
vacuum
system
according
to
the
circuit
diagram
in
the
switch
and
control
cabinet.
Procedure:
Ensure
that
the
power
supply
for
the
vacuum
system
corresponds
to
the
specifications
in
the
circuit
diagram.
Ensure
that
the
vacuum
system
is
not
impaired
by
electrical
or
electromagnetic
impulses
of
the
power
supply.
Contact
Busch
if
necessary.
Connect
the
switch
and
control
cabinet
to
the
power
supply
(connection
values,
see
chap.
14).
ATTENTION!
Danger
of
damage
to
the
motor
Wrong
rotating
direction.
•
Operation
in
the
wrong
rotating
direction
may
damage
the
vacuum
system
after
a
very
brief
time.
Ensure
that
the
rotating
direction
is
correct
before
commissioning.
Use
the
glued
‐
on/cast
‐
in
arrow
to
determine
the
intended
rotating
direction.
Switch
on
the
vacuum
pump
for
a
fraction
of
a
second.
Observe
the
fan
wheel
and
determine
the
rotating
direction
just
before
standstill.
To
change
the
rotating
direction:
Swap
any
two
phases
of
the
power
supply.