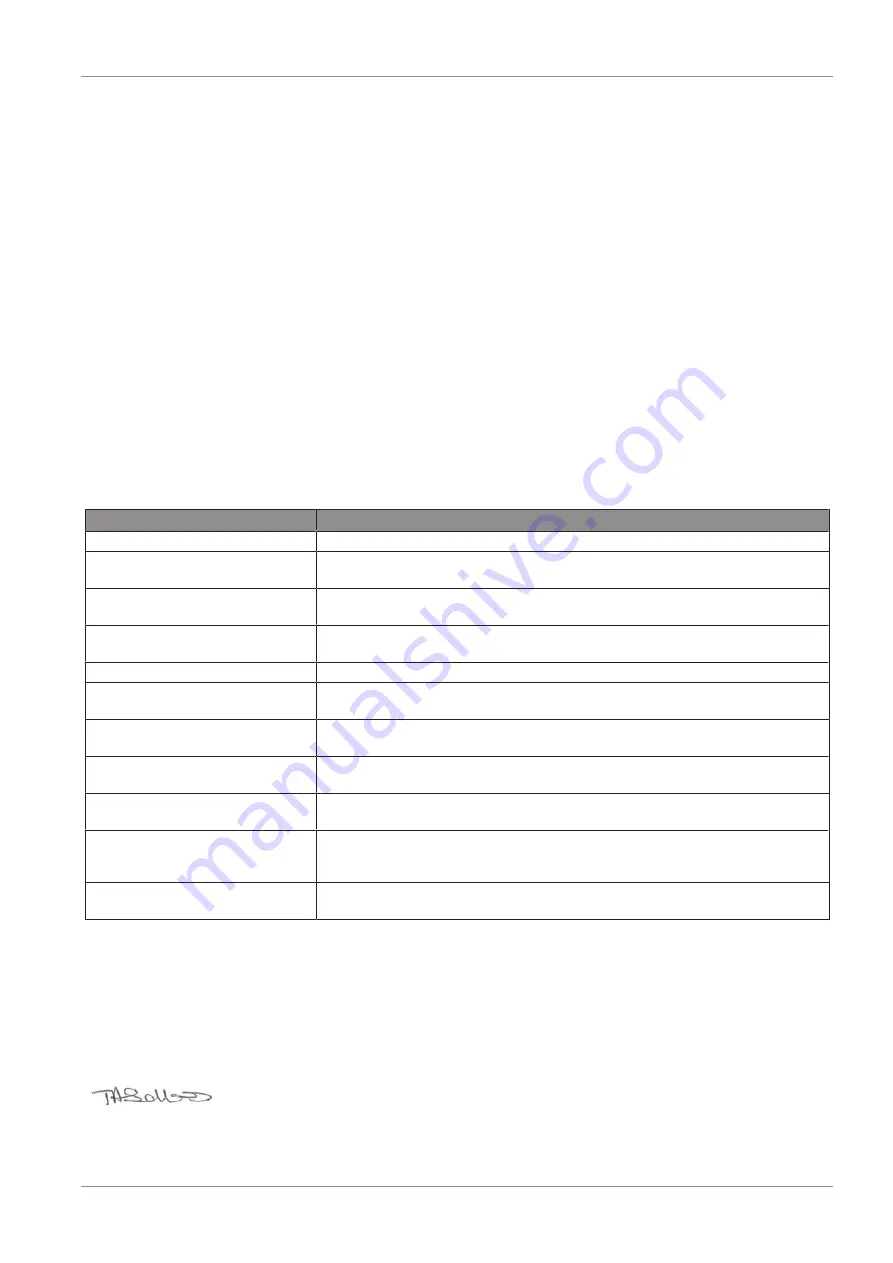
EU Declaration of Conformity | 13
Instruction Manual Supplement DOLPHIN VL Systems ATEX_EN_en
33 / 36
13 EU Declaration of Conformity
This Declaration of Conformity and the CE-mark affixed to the nameplate are valid for the machine within the Busch scope of
delivery. This Declaration of Conformity is issued under the sole responsibility of the manufacturer.
When this machine is integrated into a superordinate machinery the manufacturer of the superordinate machinery (this can be
the operating company, too) must conduct the conformity assessment process for the superordinate machine or plant, issue the
Declaration of Conformity for it and affix the CE-mark.
The manufacturer
Busch GVT Ltd.
Westmere Drive, Crewe Business Park
Crewe, Cheshire, CW1 6ZD
United Kingdom
declares that the machine(s)
DOLPHIN
‘
ATEX
’
VL 0100 A; VL 0130 A; VL 0170 A; VL 0180 A; VL 0220 A; VL 0270 A; VL 0320
A; VL 0430 A; VL 0510 A; VL 0530 A; VL 0630 A; VL 0750 A; VL 0800 A
fulfil(s) all the relevant provisions from European directives:
– ‘Machinery’ 2006/42/EC
– ‘ATEX Directive’ 2014/34/EU, for use in potentially explosive areas according to classification written on the machine
nameplate
– ‘Electromagnetic Compatibility’ 2014/30/EU
– ‘RoHS’ 2011/65/EU Restriction of the use of certain hazardous substances in electrical and electronic equipment (incl. all
related applicable amendments)
and comply(-ies) with the following designated standards that have been used to fulfil those provisions:
Standard
Title of the Standard
EN ISO 12100 : 2010
Safety of machinery - Basic concepts, general principles of design
EN ISO 13857 : 2019
Safety of machinery - Safety distances to prevent hazard zones being reached by the
upper and lower limbs
EN 1012-1 : 2010
EN 1012-2 : 1996 + A1 : 2009
Compressors and vacuum pumps - Safety requirements - Part 1 and Part 2
EN ISO 2151 : 2008
Acoustics - Noise test code for compressors and vacuum pumps - Engineering method
(grade 2)
EN 60204-1 : 2018
Safety of machinery - Electrical equipment of machines - Part 1: General requirements
EN IEC 61000-6-2 : 2019
Electromagnetic compatibility (EMC) - Generic standards. Immunity for industrial envi-
ronments
EN IEC 61000-6-4 : 2019
Electromagnetic compatibility (EMC) - Generic standards. Emission standard for indus-
trial environments
EN ISO 13849-1 : 2015
(1)
Safety of machinery - Safety-related parts of control systems - Part 1: General principles
for design
EN ISO 80079-36 : 2016
Explosive atmospheres - Part 36: Non-electrical equipment for explosive atmospheres -
Basic method and requirements
EN ISO 80079-37 : 2016
Explosive atmospheres - Part 37: Non-electrical equipment for explosive atmospheres -
Non electrical type of protection constructional safety ‘c’, control of ignition source ‘b’,
liquid immersion ‘k’
EN 1127-1 : 2019
Explosive atmospheres - Explosion prevention and protection - Part 1: Basic concepts
and methodology
For all category 1 products the following applies:
Intertek Italia Spa, notified body number 2575 issued an EU-type examination certificate for the above equipment N° ITS09AT-
EX16362X.
Legal person authorized to compile the technical file
and authorized representative in the EU
(if the manufacturer is not located in the EU):
Busch Dienste GmbH
Schauinslandstr. 1
DE-79689 Maulburg
Crewe, 16.04.2021
Tracey Sellars, General Director
Summary of Contents for DOLPHIN VL 0100 A
Page 34: ...Note...
Page 35: ...Note...