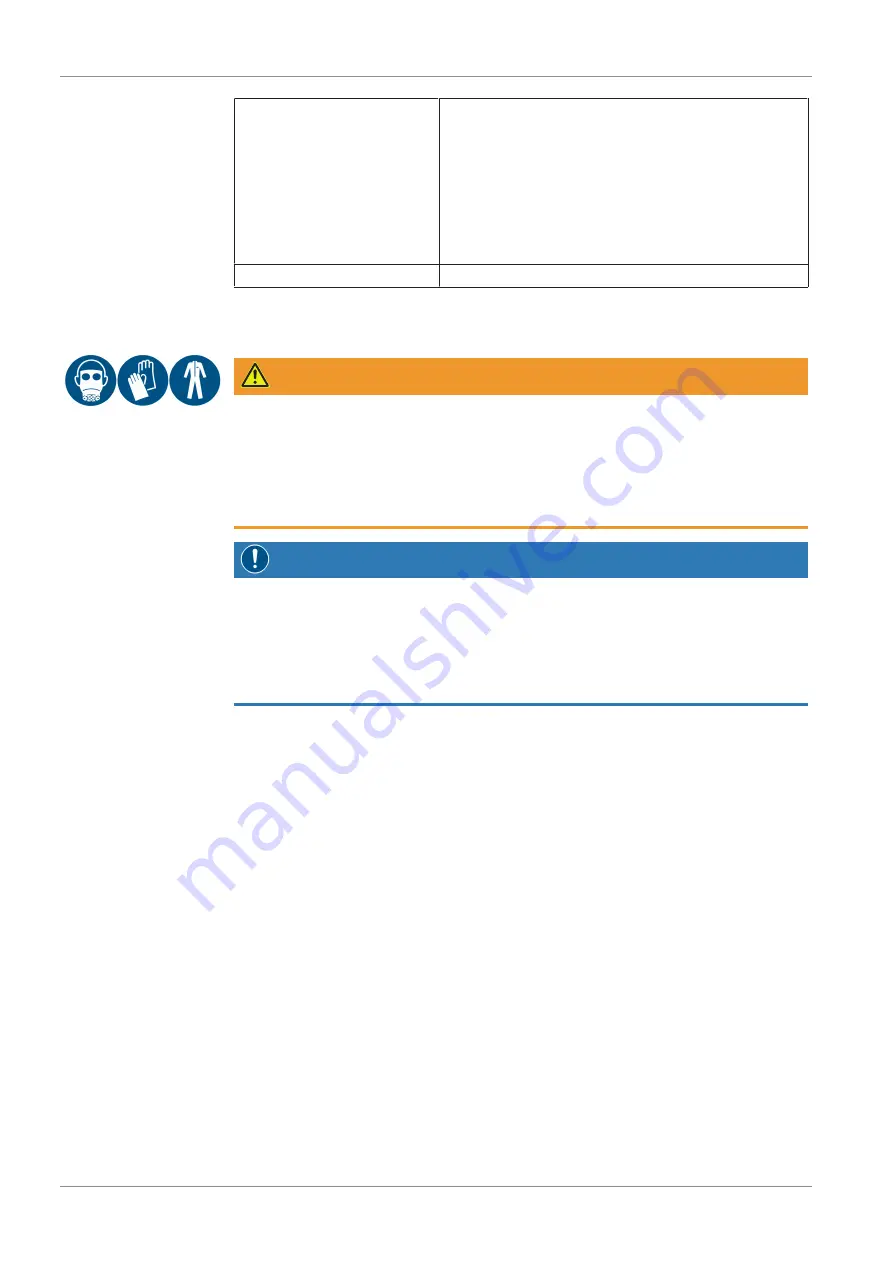
8 | Overhaul
20 / 32
0870237638_LR0110-0580A_-_IM_en
Every year
• Carry out a visual inspection on the machine to check
for dust and dirt. Avoid using any cleaning products
which may result in damage to the pump label or
paint.
• If applicable, gland packing has to be replaced annu-
ally or sooner if readjustment is no longer possible.
If an inlet screen or filter is installed:
• Check it and clean if necessary.
Every 5 years
• Have a major overhaul (contact Busch).
8
Overhaul
WARNING
Machines contaminated with hazardous material.
Risk of poisoning!
Risk of infection!
If the machine is contaminated with hazardous material:
• Wear appropriate personal protective equipment.
NOTICE
Improper assembly.
Risk of premature failure!
Loss of efficiency!
• It is highly recommended that any dismantling of the machine that goes beyond any-
thing that is described in this manual should be done through Busch.
In case of the machine having conveyed gas that was contaminated with foreign materi-
als which are dangerous to health:
• Decontaminate the machine as much as possible and state the contamination
status in a ‘Declaration of Contamination’.
Busch will only accept machines that come with a completely filled in and legally binding
signed ‘Declaration of Contamination’ (form downloadable from
).
9
Decommissioning
• Shut down the machine and lock against inadvertent start up.
• Vent the connected lines to atmospheric pressure.
• Disconnect all connections.
If the machine is going to be stored:
• See Storage.
9.1 Dismantling and Disposal
• Separate special waste from the machine.
• Dispose of special waste in compliance with applicable regulations.
• Dispose of the machine as scrap metal.