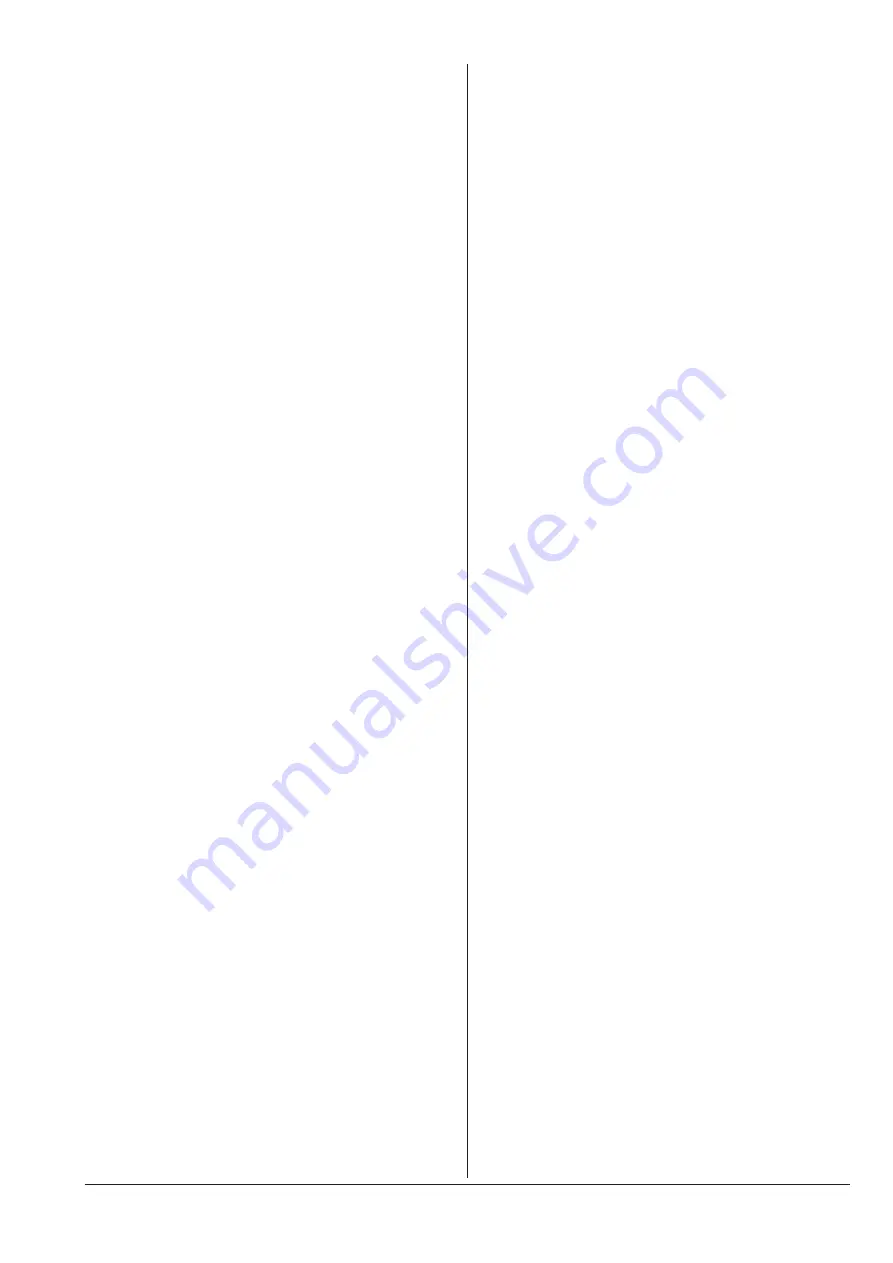
the order documentation for the specified operating liquid temper-
ature)
●
Check the bearing temperature
(with a hand held probe or a permanent gauge, if fitted; at 25 °C
ambient temperature the bearing temperature should not exceed
60 °C (operating liquid = water) or 80 °C (operating liquid = oil);
for other ambient temperatures adjust accordingly)
●
Check that the vacuum pump achieves the usual/specified vacuum
level
●
Check all pipe work for leakage
Version with mechanical seals:
●
Check the mechanical seals for leakage
●
Make sure that the vacuum pump is shut down and locked against
inadvertent start up
In case of operation in a dusty environment:
◆
Clean as described under
Ú
page 11: Every 6 Months:
Every 4 Months or 3000 Operating Hours:
Larger units (size 6 and above):
●
Regrease the bearings (lithium based grease NLGI class 2)
Smaller units up to and including size 5 are greased for life
Every 6 Months:
●
Make sure that the housing is free from dust and dirt, clean if nec-
essary
●
Make sure that the vacuum pump is shut down and locked against
inadvertent start up
●
Clean the fan cowling, the fan wheel, the ventilation grille and the
cooling fins
Every Year:
●
Make sure that the vacuum pump is shut down and locked against
inadvertent start up
In case an inlet screen is installed:
◆
Check the inlet screen, clean if necessary
●
Remove the fan cowling of the drive motor, turn the shaft by hand
and check for ease of rotation
(seizure or binding could indicate ingress of foreign material, mis-
alignment or the vacuum pump bed plate out of flatness)
Version with relubricatable bearings:
◆
Check the grease condition of the bearings (e.g. water or de-
bris contamination)
Version with mechanical seal:
◆
Disassemble the mechanical seal and check for signs of wear,
scratches of cracks on the faces. Check also the o-rings for
damage and replace if necessary.
●
Replace the bearings
Version with mechanical seal:
●
Replace the mechanical seals
Dismantling and Reassembly
Note
: Complete disassembly is seldom necessary and the vacuum
pump need only be disassembled to the point required to repair or ser-
vice it.
See the sectional drawings for cross-reference.
Series 1 = Gland packing or cartridge mechanical seal
Series 2 & 3 = Mechanical seal
Dismantling
●
Disconnect from electrical supply and process piping
●
Drain as much operating liquid from the vacuum pump as possible
●
Stand the vacuum pump vertically with the drive end upwards
●
Mark the castings to ensure the correct reassembly and alignment
●
Remove the manifold or crossover part (147.1, as applicable)
●
Remove the bearing caps (360.0, 360.1)
Size 9 to 11:
◆
Slacken the locknuts (923.)
◆
Slacken the inner bearing caps (360.2, 360.3) and slide back
Sizes 3 to 8, series 1:
◆
Remove the drive end bearing housing (350) using bearing
pullers
Sizes 3 to 8, series 2:
◆
Remove the drive end bearing housing (357) using two jacking
screws
Size 9, 10, 11:
◆
Remove the drive end bearing housing (350) using bearing
pullers
◆
Remove the drive end bearing using pullers
Version with mechanical seal:
◆
Remove the drive end mechanical seal (433)
Version with gland packing:
◆
Remove the drive end gland follower (452)
Size 9, 10, 11 only:
◆
Refit the drive end bearing housing with a dummy bearing to
support the shaft
●
Stand the vacuum pump up in vertical position with the drive end
pointing down
Sizes 3 to 8, series 1:
◆
Remove the non drive end bearing housing (350) using bear-
ing pullers
Sizes 3 to 8, series 2:
◆
Remove the non drive end bearing housing (357) using two
jacking screws
Size 9, 10, 11:
◆
Remove the non drive end bearing housing (350) using bear-
ing puller
◆
Remove the non drive end bearing using pullers
Version with mechanical seal:
◆
Remove the non drive end mechanical seal (433)
Version with gland packing:
◆
Remove the non drive end gland follower (452)
●
Remove the tie rods (905)
●
Remove the non drive end end casing (107) complete with the side
plate (137.4) and the valve (741, if fitted)
●
Remove the impeller casing (110.1)
●
Remove the shaft assembly complete with the parts 210, 137.3,
137.2, 230, 521 and 921 (as applicable)
●
Secure the impeller assembly and remove the locknut (922) using a
C-spanner
●
Remove the impeller(s) and inter plates (two stage only) from the
shaft
Reassembly
The vacuum pump is built up in reversal of the dismantling instructions.
●
Clean all parts thorougly before commencing rebuild
LA 0053-1111 A, LB 0063-1011 A
Dismantling and Reassembly
0870150638 / 091222
page 11
Summary of Contents for DOLPHIN LA 0053-0143 A
Page 27: ......