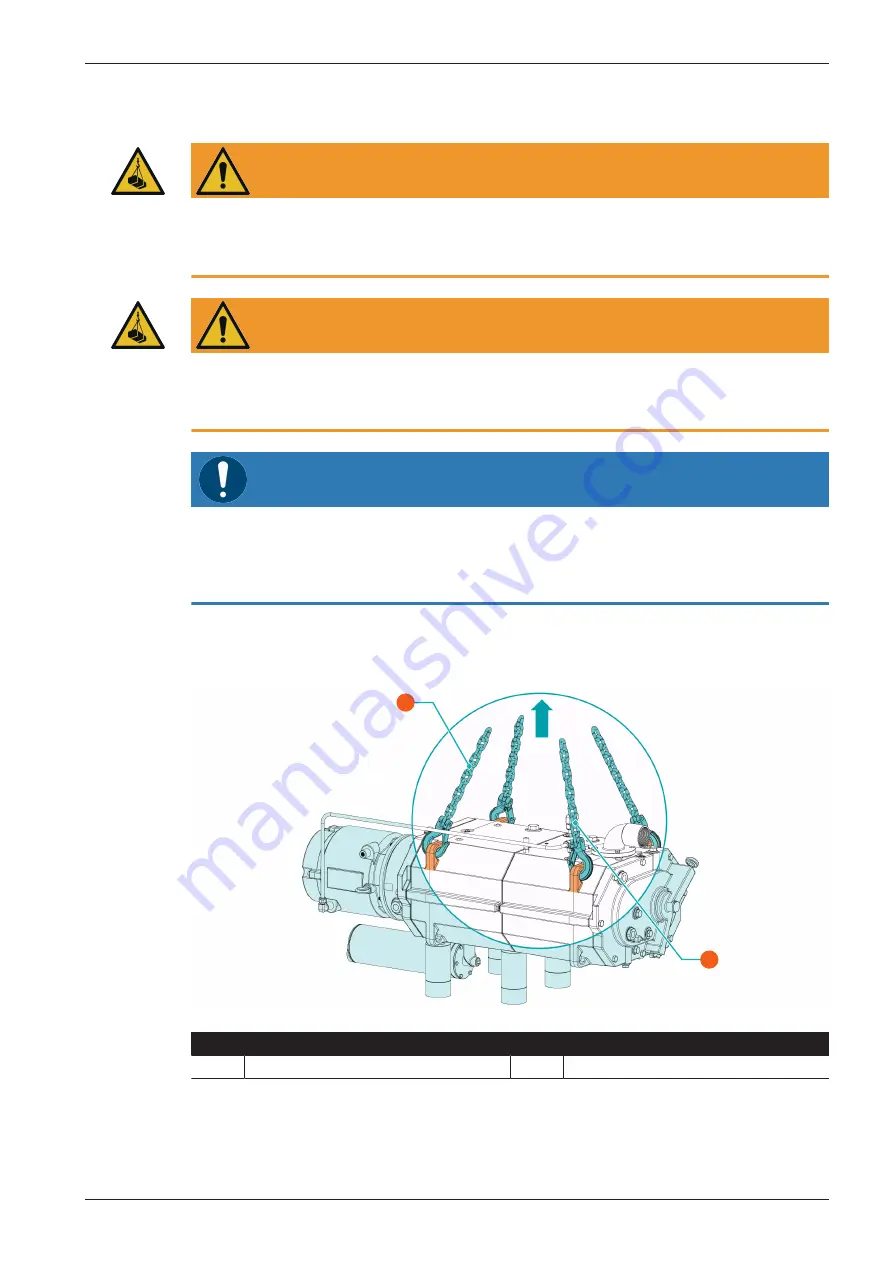
Transport | 3
Instruction Manual COBRA NC 0500 B_EN_en
7 | 36
3
Transport
WARNING
Suspended load.
Risk of severe injury!
●
Do not walk, stand or work under suspended loads.
WARNING
Lifting the machine using the motor eye bolt.
Risk of severe injury!
●
Do not lift the machine using the eye bolt fitted to the motor. Only lift the machine as shown.
NOTICE
In case the machine is already filled with oil.
Tilting a machine that is already filled with oil can cause large quantities of oil to ingress into
the cylinder.
●
Drain the oil prior to every transport or always horizontally transport the machine.
●
To find out the weight of the machine, refer to the chapter
29] or the
nameplate (NP).
1
2
Description
1
Length of slings: 3x 600 mm
2
Optional sling
●
Check the machine for transport damage.
If the machine is secured to a base plate:
●
Remove the machine from the base plate.