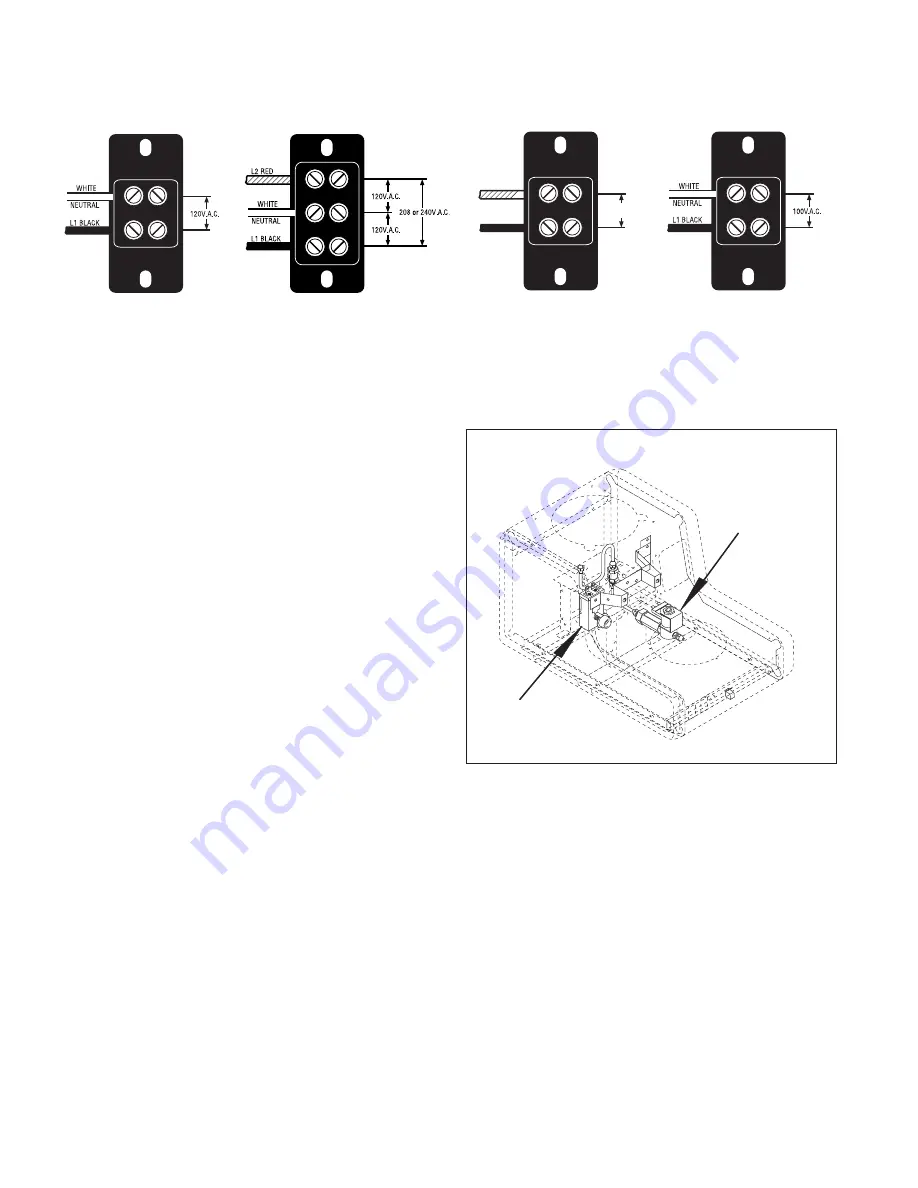
Page 4
ELECTRICAL REQUIREMENTS
CAUTION - Do not connect the brewer to the power source until specified in Initial Set-Up.
MODELS OT15 & 20 require
2-wire, grounded service rated
120 volts ac, 15 or 20 amp
respectively, single phase, 60
Hz. Model 15 has an attached
cordset.
MODELS OT35 & RT35 require
3-wire, grounded service rated
120/208 or 120/240 volts ac, 20
amp, single phase, 60 Hz.
Electrical Hook-Up
Model OT15 has an attached cordset.
Models OT20, OT35, & RT35, proceed as follows:
CAUTION – Improper electrical installation will damage
electronic components.
1.
An electrician must provide electrical service as
specified.
2. Using a voltmeter, check the voltage and
color coding of each conductor at the electrical
source.
3.
Remove the front panel beneath the sprayhead
and rotate the control thermostat knob fully
counterclockwise to the “OFF” position and re-
place the panel.
4. Remove the rear panel, feed the cord through
the strain relief, and connect it to the terminal
block.
5. Connect the brewer to the power source and
verify the voltage at the terminal block before
proceeding. Replace the rear panel.
6.
If plumbing is to be hooked-up later be sure the
brewer is disconnected from the power source.
If Plumbing has been hooked-up, the brewer is
ready for Initial Set-Up.
MODELS OTA, RTA & RT35B
require 2-wire, grounded ser-
vice rated 240 volts ac or 200
volts ac, 20 amp single phase,
50 Hz.
MODEL RT requires
2-wire, grounded service
rated 120 volt ac, 25 amp
single phase, 50 Hz.
P1709
32440 010308
L2 RED
L1 BLACK
200, 230 or
240V A.C.