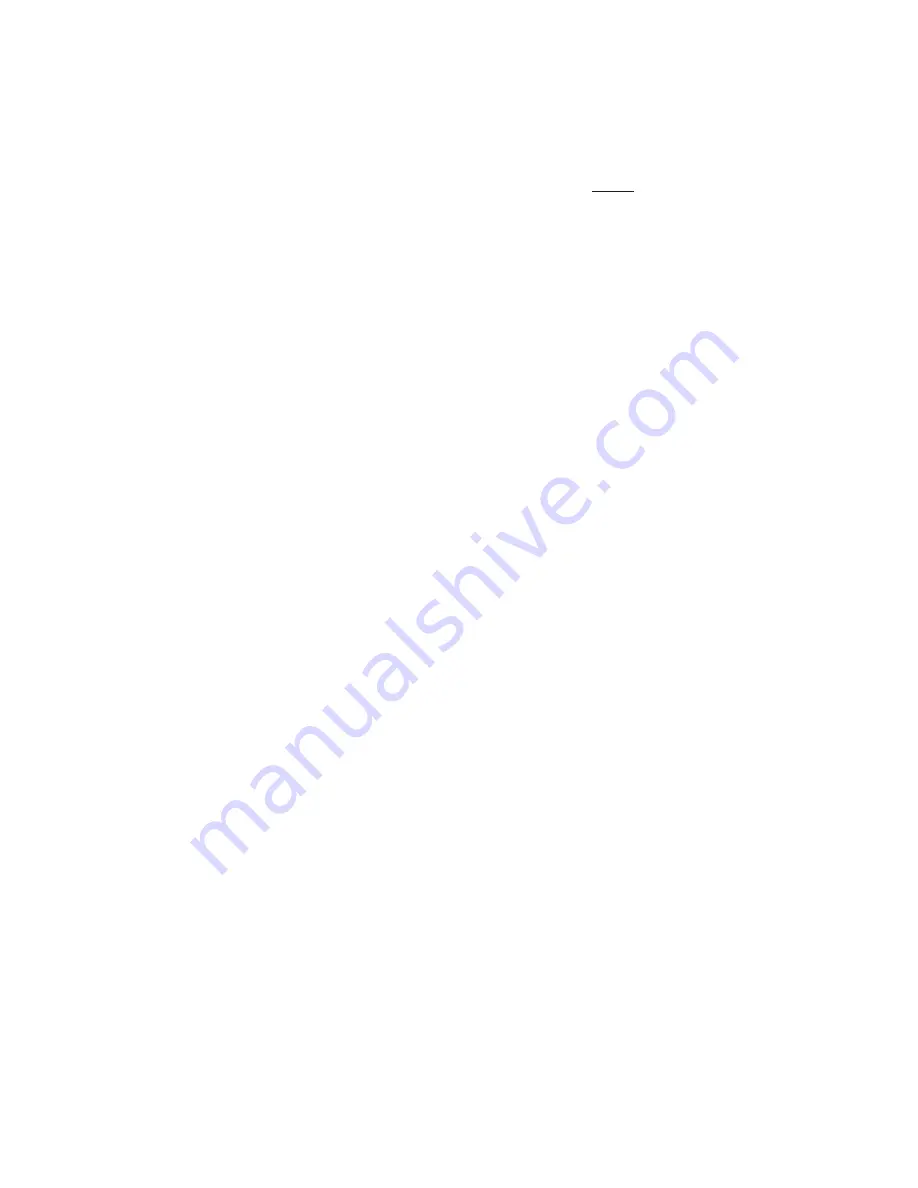
4
PLUMBING REQUIREMENTS
This dispenser must be connected to a COLD WATER system with operating pressure between 20 and 100 psi (138
and 690 kPa). This water source must be capable of producing a minimum flow rate of 3 fluid ounces (88.7 milliliters) per
second. A shut off valve should be installed in the line before the dispenser. Install a regulator in the line when pressure is
greater than 100 psi (690 kPa) to reduce it to 50 psi (345 kPa). Also if the install location experiences pressure fluctuations
greater than 20 psi (138kPa). The main water inlet is a 3/8” (9.52 mm) MFL connection.
Additionally, the dispenser’s rinse connection may be connected to a HOT WATER system.
Caution:
MAXIMUM RINSE WATER TEMPERATURE: 170 degrees F (76.6 degrees C)
Use BUNN-O-MATIC tubing, part number 34325.10_ _ (see Illustrated Parts Catalog for complete part number) for hot
water connection.
The rinse water operating pressure must be between 20 and 100 psi (138 and 690 kPa). A shut off valve should be
installed in the line before the dispenser. Install a regulator in the line when pressure is greater than 100 psi (690 kPa) to
reduce it to 50 psi (345 kPa). The rinse water inlet is a 1/4” (6.35 mm) MFL connection.
NOTE- At least 18 inches (457 mm) of an FDA approved flexible beverage tubing, such as reinforced braided
INITIAL SET-UP
CAUTION: The dispenser is very heavy! Use care when lifting or moving it. Use at least two people to lift or move the
dispenser. Place dispenser on a sturdy counter or shelf able to support at least 150 lbs. (68 kg). The JDF-2 is designed
for indoor use only.
Set the dispenser on the counter where it will be used. The JDF-2 requires a minimum of 4 inches (102 mm) of air
clearance at the rear and 8 inches (203 mm) of air clearance above the dispenser. Minimal clearance is required between
the dispenser sides and the wall or another appliance. For optimum performance, do not let warm air from surrounding
machines blow on the JDF-2. Leave some space so the dispenser can be moved for cleaning.
ELECTRICAL REQUIREMENTS
CAUTION: The dispenser must be disconnected from the power source until specified in Electrical Hook-Up.
The 120V rated dispensers have an attached cord set and require a 2-wire, grounded, individual branch circuit rated
120 volts ac, 15 amp, single phase, 60Hz. The mating connector must be a NEMA 5-15R. (Refer to the data plate for exact
electrical requirements.)
The 230V rated dispensers have an attached cord that requires an attachment plug cap rated at least 10a, 230V. The
attachment plug cap must meet with applicable national/local electrical codes.
ELECTRICAL HOOK-UP
CAUTION: Improper electrical installation will damage electronic components.
1. An electrician must provide electrical service as specified.
2. Using a voltmeter, check the voltage and color coding of each conductor at the electrical source.
3. Connect the dispenser to the power source.
4. If plumbing is to be hooked up later, be sure the dispenser is disconnected from the power source. If plumbing has
been hooked up, the dispenser is ready for Initial Fill.
38310 030308
CE REQUIREMENTS
• This appliance must be installed in locations where it can be overseen by trained personnel.
• For proper operation, this appliance must be installed where the temperature is between 0°C to 35°C.
• Appliance shall not be tilted more than 10° for safe operation.
• An electrician must provide electrical service as specified in conformance with all local and national codes
• This appliance must not be cleaned by water jet.
• This appliance is not intended for use by persons (including children) with reduced physical, sensory or mental capa-
bilities, or lack of experience and knowledge, unless they have been given instructions concerning use of this appli-
ance by a person responsible for its safety.
• If the power cord is ever damaged, it must be replaced by the manufacturer or authorized service personel with a special
cord available from the manufacturer or its authorized service personel in order to avoid a hazard.