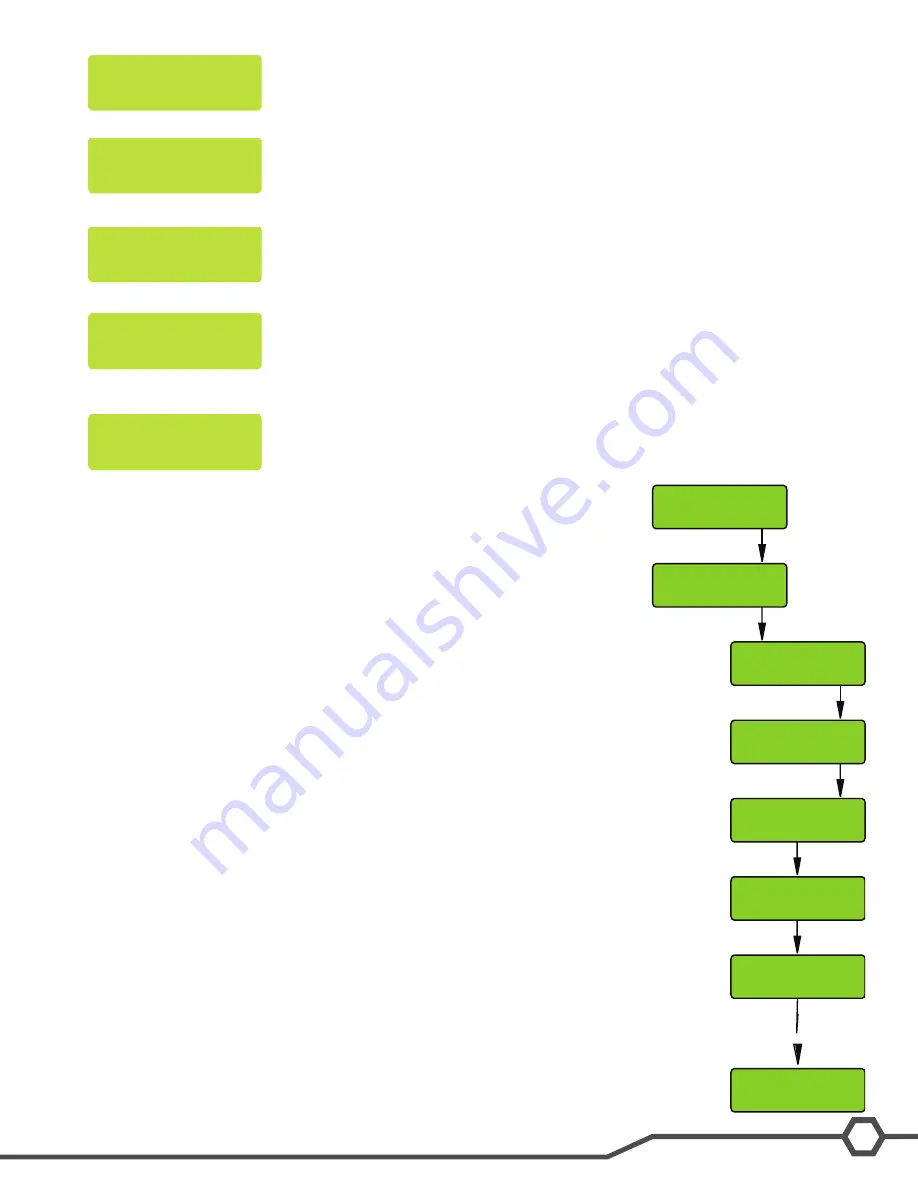
Bunn-O-Matic Corporation
19
Sets the inability to initiate a brew cycle if the funnel is not properly inserted into the
funnel rails.
By selecting yes to this option, a message will display alerting the operator that the
machine is currently in a brew process. If enabled, the message will only display while
the machine is brewing.
This function allows the operator to enter in the telephone number to call if service is
needed. The service number will be displayed anytime there is a fault message dis-
played.
(For Authorized Service Personnel Only)
This function allows the testing of individual components and the ability to check switch-
es for proper function. This function also tests the funnel sensor coil’s frequency (diag-
nostic tool for troubleshooting purposes only).
Refer to Service Manual for in depth procedures.
This function allows the operator to erase
all
of the previously entered recipes and ad
messages. Factory-set default values will replace All previous settings.
Calibrating the Sprayhead Flow Rate
Step 1:
Place a measuring container with a minimum capacity of 60 ounces
beneath the funnel of the brewer. Water can also be dispensed into the server and
then into the measuring container.
Step 2:
Press and hold the right hidden switch to enter level 2 programming.
Continue to press the right hidden switch until the display reads “Calibrate Flow?”.
Step 3:
Press YES to advance to the “Spray Head Cal?” function screen.
Step 4:
Press YES. The display will read “Container Ready?” If the container is
under the funnel, press YES. The display will read “Calibrate Spray…Press Brew to
Start”.
Step 5:
Press and release the BREW switch. The display will read “Calibrate
Spray…60 Sec to Finish”. The 60 second timer on the display will count down to
zero. When the counter reaches zero, the display will change to OZ, along with the
existing ounces per minute.
Step 6:
Measure the amount of water in the container and using the (-) or (+),
adjust the amount on the display to match the amount in the container. Then press
DONE.
Step 7:
The display should now read “New Spray Flow” along with the correct flow
rate of the sprayhead in ounces per minute. After 5 seconds, the display will return
to the “Calibrate Flow?” screen.
SERVICE TOOLS
NO
YES
FACTORY DEFAULTS
NO
YES
SPRAYHEAD CAL
NO YES
CALIBRATE FLOW?
NO YES
CONTAINER READY?
QUIT YES
CALIBRATE SPRAY
QUIT START
CALIBRATE SPRAY
60 SEC TO FINISH
SPRAYHD OZ XX.X
(-) DONE (+)
NEW SPRAY FLOW
XX.X OZM
CALIBRATE FLOW?
NO YES
5 sec
ENTER SERVICE #
NO
YES
FUNNEL DETECT?
NO DONE YES
BREW ALERT?
NO DONE YES
Summary of Contents for ITCB TWIN HV
Page 1: ...BUNN TECHNICAL TRAINING ITCB High Volume...
Page 27: ......