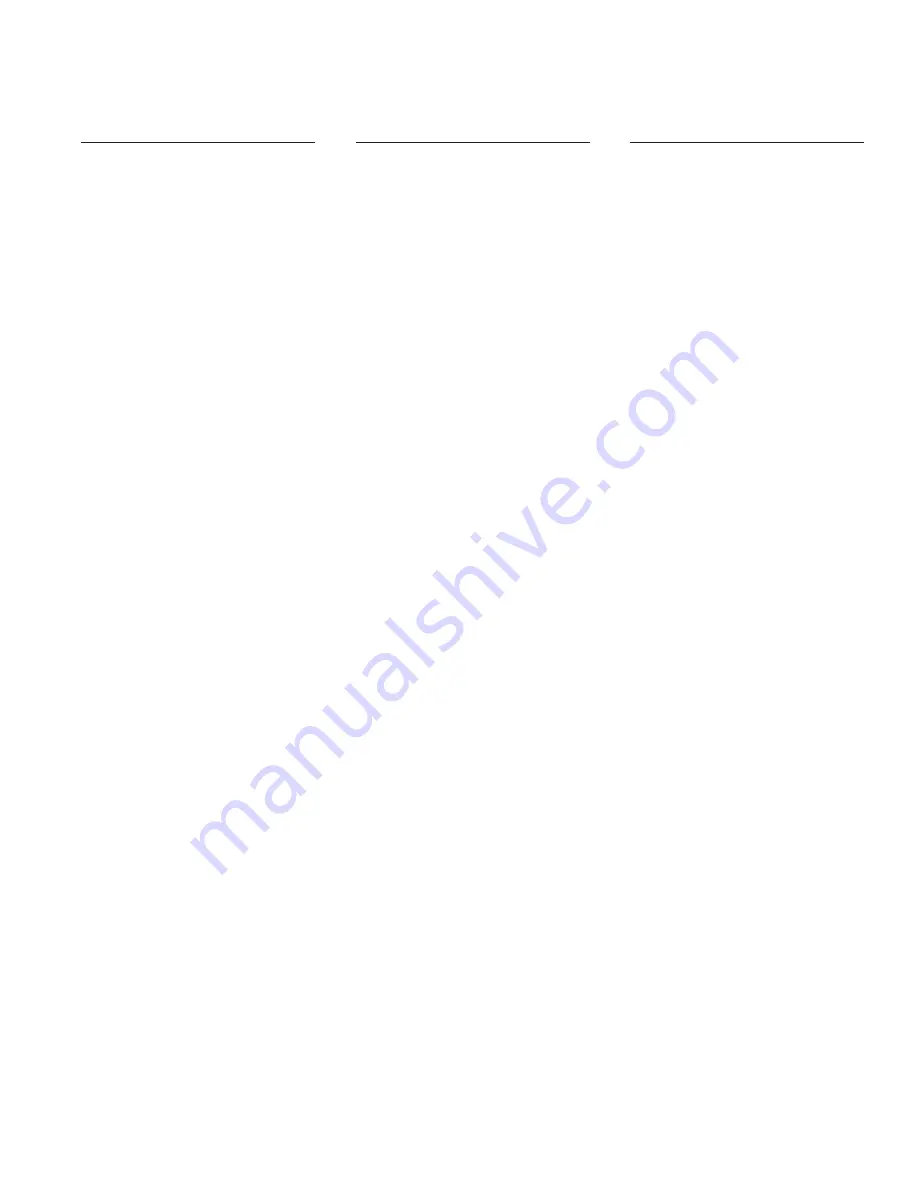
Page 17
TROUBLESHOOTING (cont.)
PROBLEM
PROBABLE CAUSE
REMEDY
BREWING CIRCUIT (cont.)
Dripping from sprayhead
Weak beverage
1. Lime build up
2. Dispense valve
1. Sprayhead
2. Water temperature
3. Filter type
4. Coffee grind
5. Funnel loading
Inspect the tank assembly for ex-
cessive lime deposits. Delime as
required.
Remove the dispense valve and
clear any obstructions. Rebuild or
replace the valve if necessary.(See
page 26)
A six-hole stainless steel spray-
head must be used for proper
extraction.
Place an empty brew funnel on an
empty server beneath the spray-
head. Initiate brew cycle and check
the water temperature immedi-
ately below the sprayhead with a
thermometer. The reading must
not be less than 195
°
F(91
°
C). Ad-
just the temperature setting to in-
crease the water temperature.
Refer to
Initial Set-up instructions.
BUNN
®
paper filters must be used
for proper extraction.
A fine drip or grind must be used
for proper extraction.
The BUNN
®
paper filter must be
centered in the funnel and the bed
of grounds leveled by shaking
gently.
29253 030101