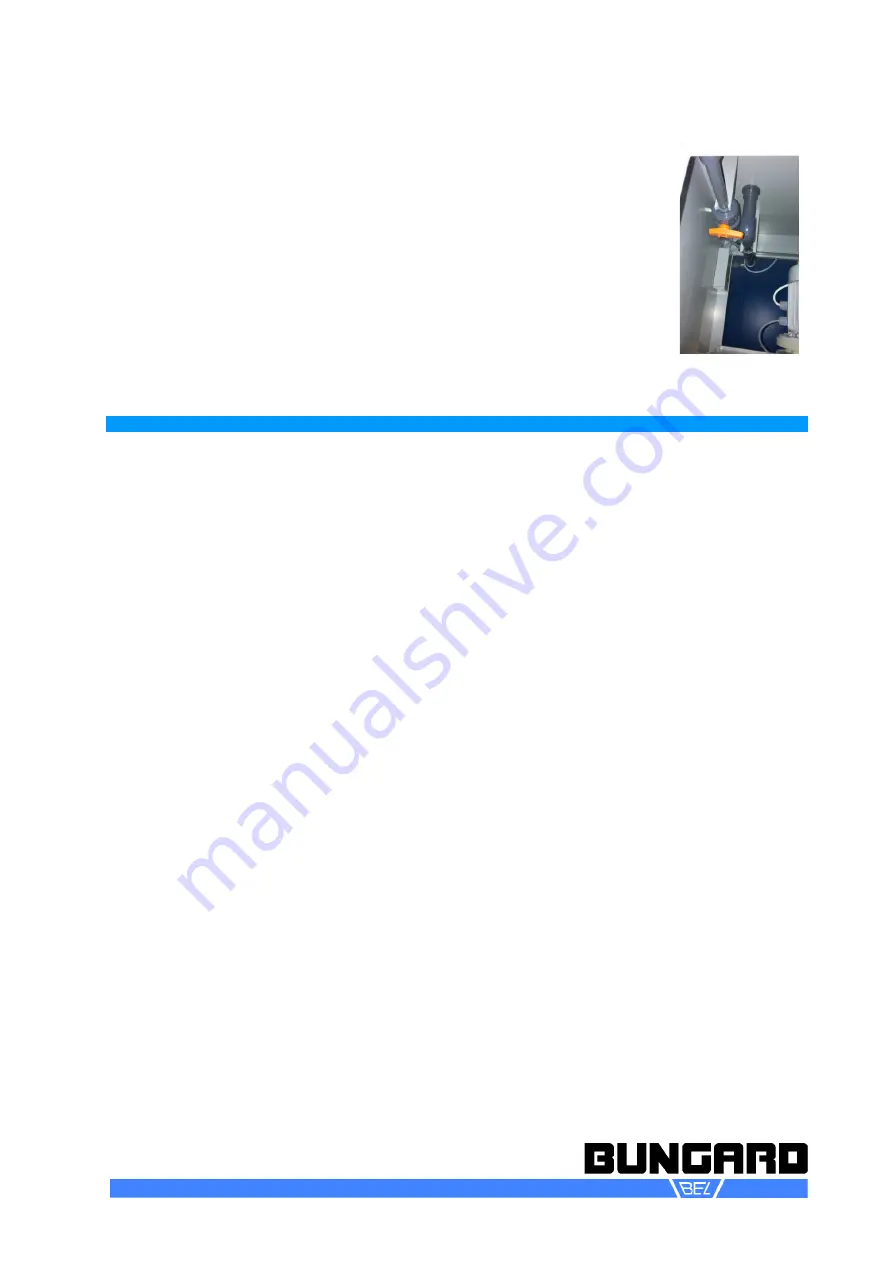
DL500-Manuel-E
Page 12 / 20
If you use the DL500 with fresh water rinse, you need to connect the machine with
a pressure resistant hose to the wall-mounted valve. In addition, the flow capacity
can be manually set by a valve located below the rinsing compartment. Set the ball
valve approx. to ¾ open and then open the cock valve so much, that the spray of
the lower manifold just reaches the height of the upper manifold.
Attention: A too high flow rate might cause the water to mount in the compartment
instead of passing into the drain!
When the etching pump has stopped, the magnetic valve also interrupts the rinse.
When you have finished work, hclose the wall-mounted valve to prevent excessive
stress to the hose.
If the optional closed-loop rinse system is installed, the valve below the rinse com-
partment should always be fully opened. See amendment for the closed loop rinse
and remarks in chapter
Waste Water
.
Cleaning and Maintenance
The machine requires almost no maintenance. The main service labour is the periodical exchange of the
etching medium and a thorough cleaning of the machine. When doing such service, you may easily check
the conveyor system for wear or use.
Detailed information as for changing the
tooth belt
, the adjustment of the nozzle and the
diassembly of
the pump
, refer to the corresponding
disassembly instructions
. This is available from us on request.
Cleaning
Except for the transparent cover, all PVC parts of the machine can be cleaned using liquid abrasive
products known from the household. If ferric chloride was used with the machine, we recommend to use
our special stain remover RX3. A thorough rinsing of the appropriate parts is necessary after each clean-
ing process.
To clean the tank, remove it from the pedestal, as described above. To have better access, you may re -
move the heater element by unscrewing it's fitting. If you use flowing water, be careful not to moisten elec-
tric parts. Remember your anti-pollution responsibility! The nozzles can be removed from the manifolds for
cleaning. Just rinse them and blow them out with compressed air. The sponge cloths on the squeegee
rollers must be treated carefully. Just wash them without rubbing them. You can wring them by rolling
them on a piece of carton. Damaged sponge cloths should be replaced by new ones. You may have such
spare cloths together with a special adhesive from us. The sifter of the suction zone of the motor can be
mechanically cleaned when mounted.
Cleaning of the machine in use of FeCl3:
Equipment:
Apron, eye protector, (Latex) gloves, 2 plastic scrapers, 2 plastic sponges, 2 buckets, paper cleaning
cloths, plastic foil, container from plastic for used etching agent
Chemicals:
Hydrochloric acid HCl technically, concentration approx. 15%, quantity approx.: DL500 55l, stain remover
RX3
Proceed:
Cut the plastic foil in the double size of the utility space of the machine. Put on protective clothing. Dis -
charge etching agents from the machine into suitable container. Take up existing sludges with scraper
mechanically and give it to the etching agent. Lift the machine and set it on the foil. If you do not have an
exhaust move the machine to proper ventilated room or outside.
Fill the machine with 15% HCl. Close the cover. Run the machine with heating switched on for several
hours. Repeat if necessary the cleaning run the next day.
Bungard Elektronik GmbH & Co. KG, Rilkestraße 1, 51570 Windeck – Germany
Tel.: +49 (0) 2292/5036, Fax: +49 (0) 2292/6175, E-mail: [email protected]
Ball Valve for the
rinsing zone