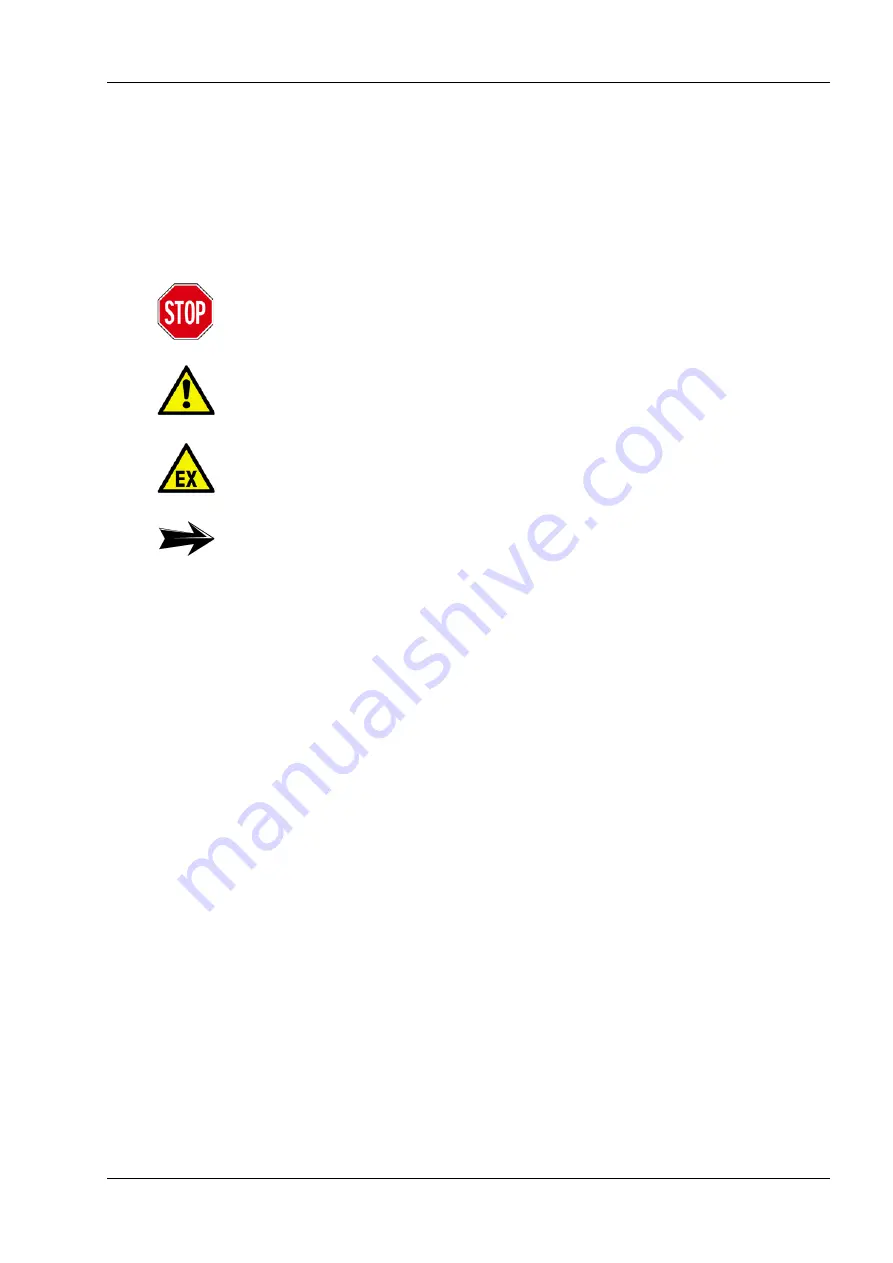
Throw sifter
Safety
5
© Copyright 2018 Bühler AG
DFTA-66620-2-en-1803
1
Safety
The machine was designed and manufactured in compliance with recognised safety
regulations. In spite of this, inappropriate use can put the user at risk of injury. For
this reason, safety has been given the highest priority.
1.1
Explanation of safety instructions
The corresponding safety instructions are indicated as follows:
1.2
Safety of personnel
•
Protective covers, hoods and gates must be installed and closed at all times.
Open or missing safety covers are danger spots for crush and cut injuries.
•
Always keep safety devices in good working condition. Never bypass or disable
any safety devices.
•
The system must be brought to a standstill before any maintenance work may
be carried out on the machine!
Make sure that all energy sources such as:
–
Electricity
–
Air
are switched off and disconnected. The lockable safety switch, which interrupts
the power at all poles, must be set to “0” and locked.
Danger!
Indicates an imminently hazardous situation which, if not avoided, can result
in death or grave injury.
Caution!
Indicates a potentially dangerous situation which, if not avoided, can result in prop-
erty damage and production failures.
Explosion hazard!
Indicates a potentially explosive situation which, if not avoided, can result in seri-
ous or fatal injuries and extensive property damage.
Note:
Indicates important information or instructions which, if not observed, can impair
the correct function of the machine and make it impossible to attain performance
parameters.
Summary of Contents for DFTA 12
Page 8: ...8 Safety Throw sifter DFTA 66620 2 en 1803 Copyright 2018 B hler AG...
Page 26: ...26 Commissioning Throw sifter DFTA 66620 2 en 1803 Copyright 2018 B hler AG...
Page 32: ...32 Operation Throw sifter DFTA 66620 2 en 1803 Copyright 2018 B hler AG...
Page 38: ...38 Maintenance Throw sifter DFTA 66620 2 en 1803 Copyright 2018 B hler AG...
Page 40: ...40 Decommissioning Throw sifter DFTA 66620 2 en 1803 Copyright 2018 B hler AG...
Page 42: ...42 After sales service Throw sifter DFTA 66620 2 en 1803 Copyright 2018 B hler AG...