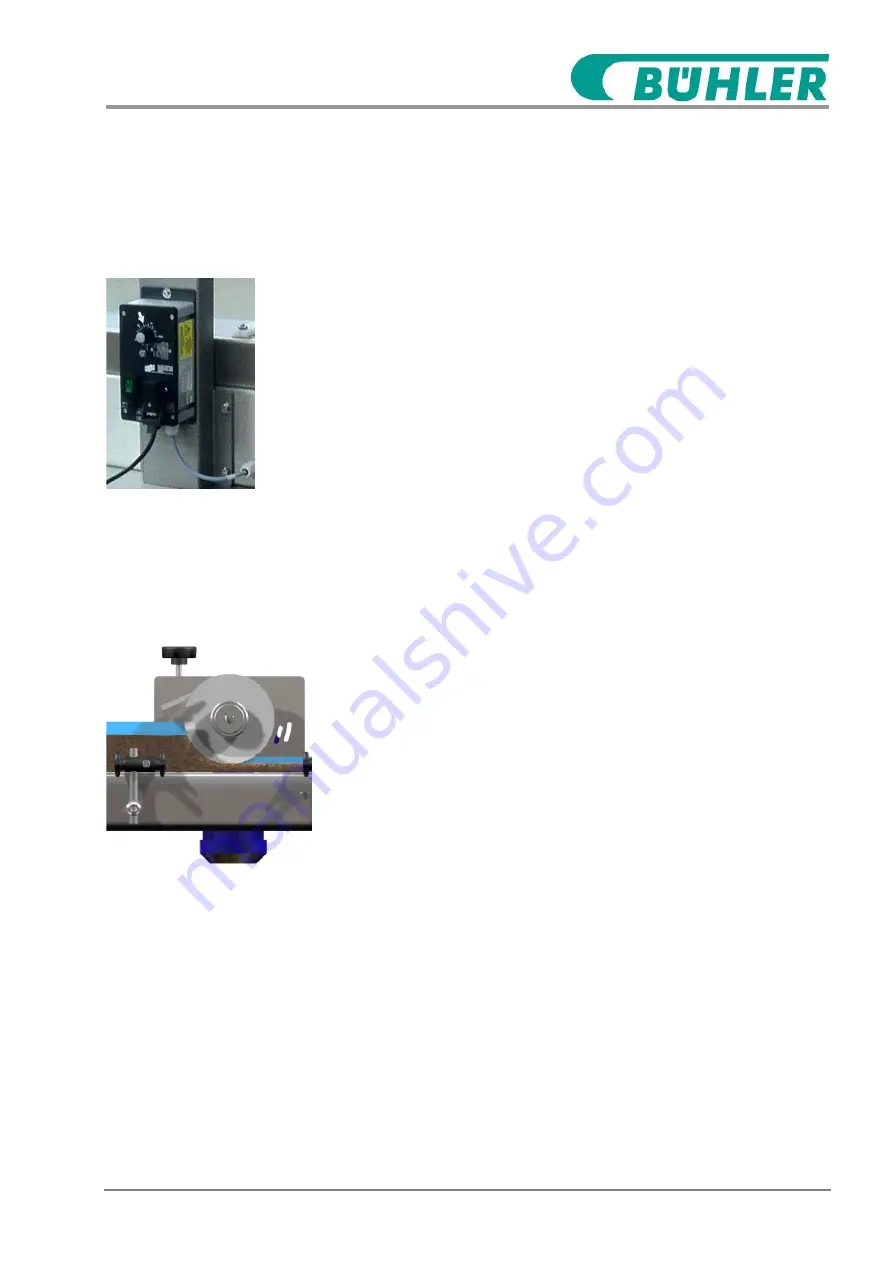
Operation
62
SnackFix
2016-08
7.4.2
Adusting the vibration unit
The amount of cereals (kg/min) depends of the creal mix and the in-
tensity of the vibration. The correct flowrate has to be found out via
measurement. Use a scale and set the correct vibration speed.
Fig. : Adjustment vibration
Adjusting the vibration
1.
Turn left
– less cereals. Turn right – more cereals.
7.4.3
Adjusting the working position at the EGW
Lifting and lowering devices for adjusting the working positions are
located on the equalizing rollers EGW.
Fig. 4: Lifting and lowering device on
the EGW
Adjusting the working position
1.
Turn the hand crank and adjust the required height. Use the
thickness gauge (accessories).