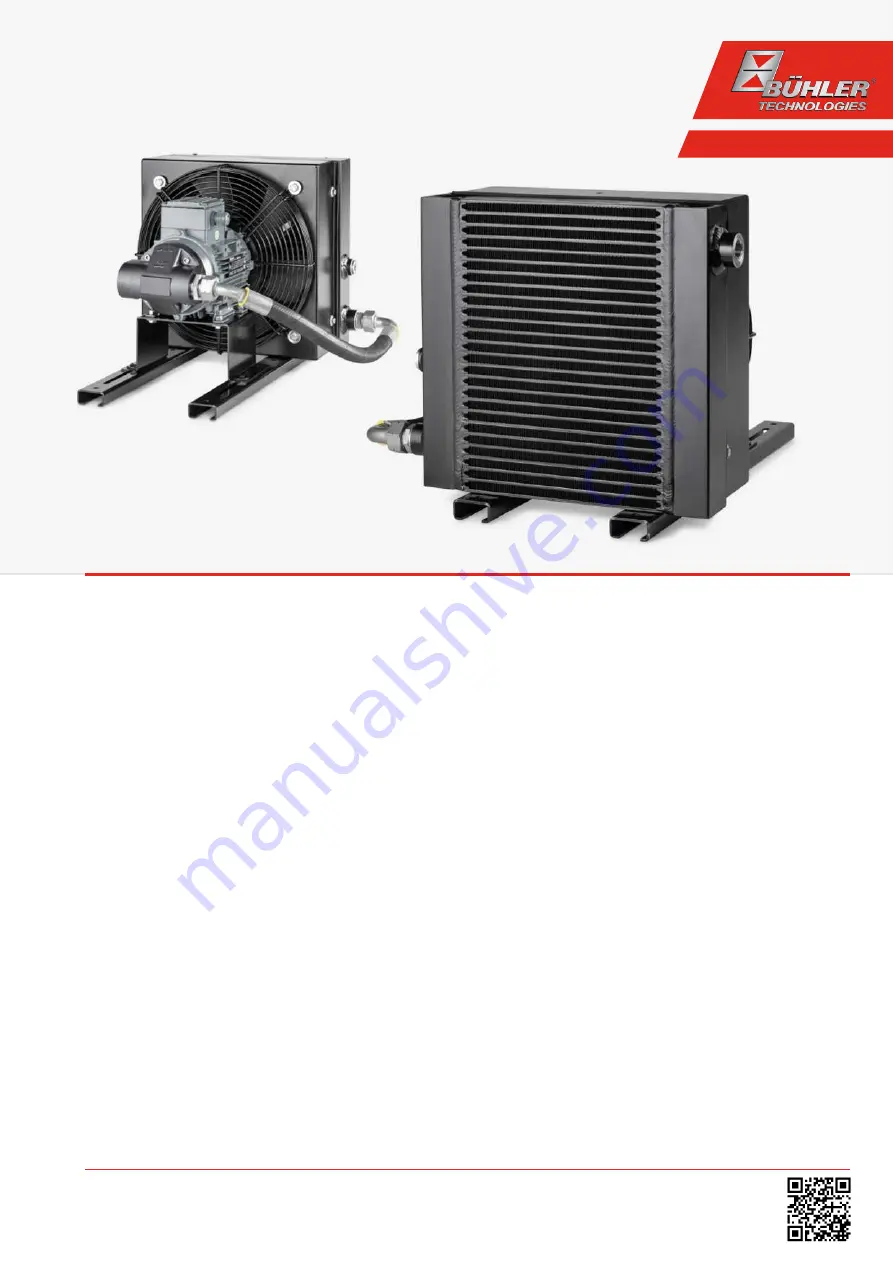
Fluidcontrol
Installation and Operation Instructions
Original instructions
Off-line cooler
ENK
BE360004
08/2022
Bühler Technologies GmbH, Harkortstr. 29, D-40880 Ratingen
Tel. +49 (0) 21 02 / 49 89-0, Fax: +49 (0) 21 02 / 49 89-20
E-Mail: [email protected]
Internet: www.buehler-technologies.com
Summary of Contents for ENK 300-15-4-0.75kW-50Hz
Page 23: ......