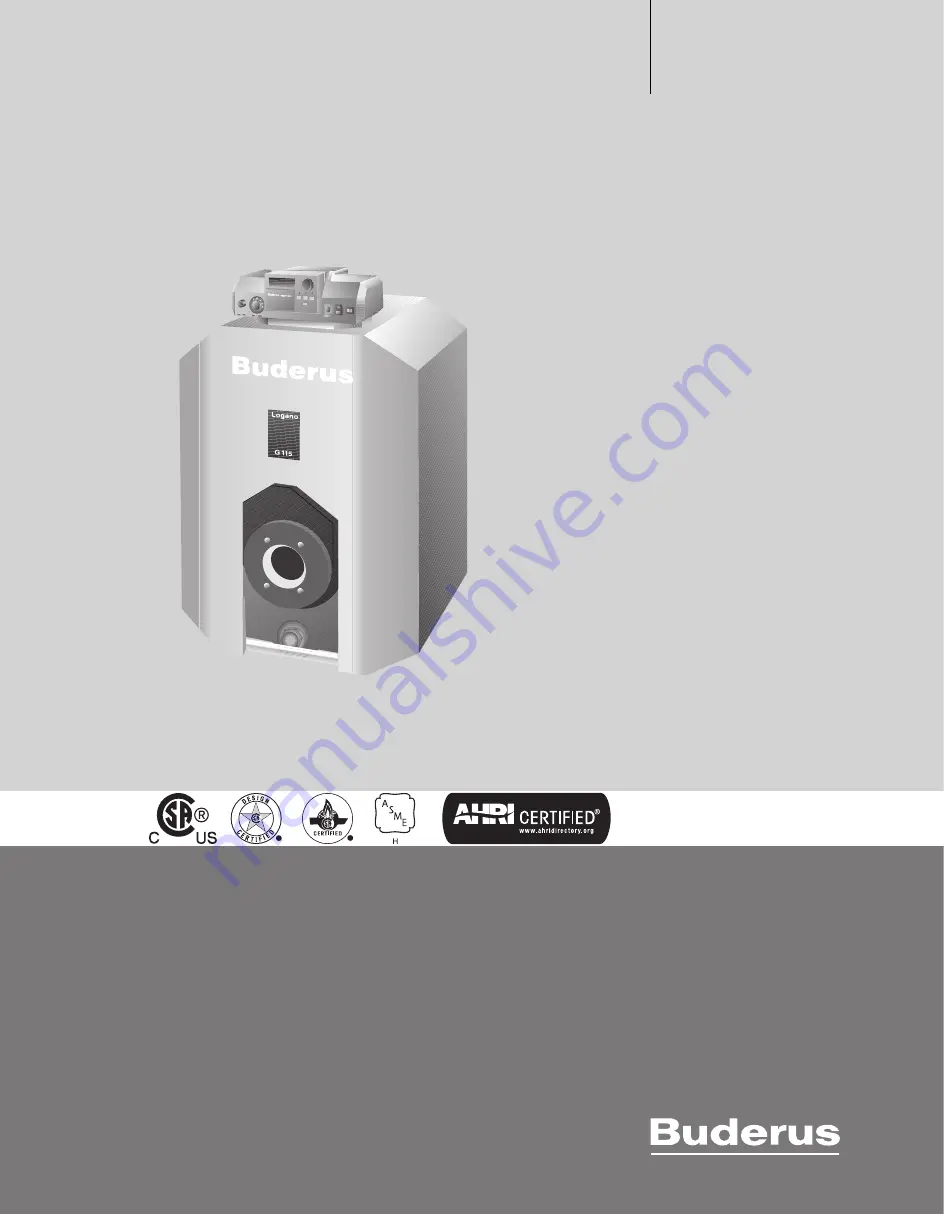
Read carefully before carrying out installation and maintenance.
Installation and Service Instructions
Low-temperature oil boiler
Logano
Caution!
Observe the safety instructions of this
installation and maintenance manual before
placing the boiler in operation.
Danger!
If installation, adjustment, modification,
operation or maintenance of the heating
system is carried out by an unqualified person,
this may result in danger to life and limb or
property damage.
The directions of this installation and
maintenance manual must be followed
precisely.
Contact a qualified service company or service
provider if support or additional information is
required.
Caution!
The operating manual is a component of the
technical documentation and must be handed
over to the operator of the heating system.
Discuss the content of this manual with the
owner or operator of the heating system to
ensure that they are familiar with all
information required for operation of the
heating system.
6 720 804 872-00.2T
G115 WS US/CA
6 720 813 418 (2019/09)US/CA