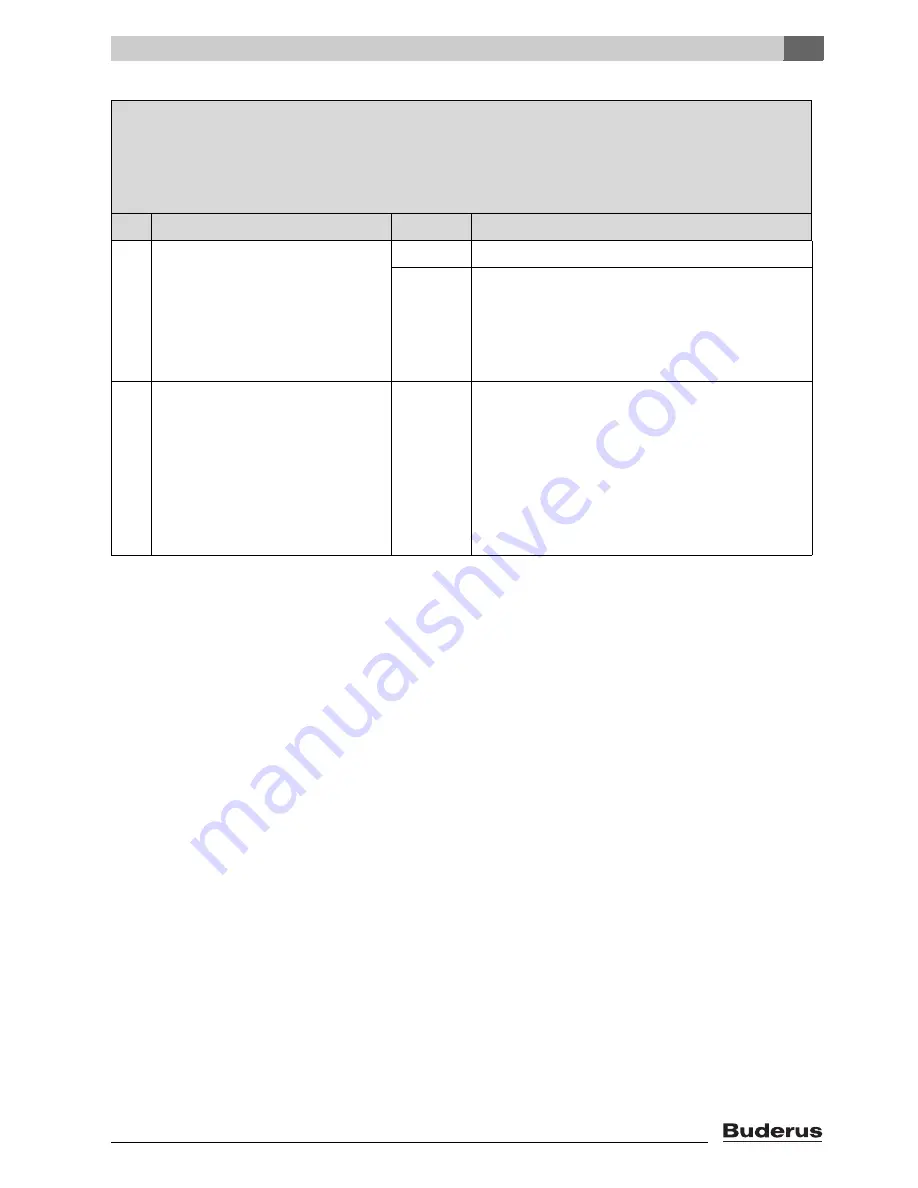
4
Fault finding
Logamax PLus GB062
29
9.
B
Switch off the boiler.
B
Check the flue gas 6Apipe/system
for blockage (In case of blockage,
due to high pressure the contacs of
diff. presure switch is opening--> 4C)
Is there a blockage in flue gas pipe ?
no:
4C ? --> 10.
yes:
B
Correct the flue gas installation (remove the blockage).
B
Switch on the boiler.
--> 10.
10
Electronic board (PCB) is defect.
B
Switch off the boiler.
B
Cut the main voltage supply.
B
Change the electronic board (PCB).
B
Switch on the main voltage supply.
B
Switch on the boiler.
B
END
4C
- Heat exchanger temperature limiter or flue gas temperature limiter has tripped.
- The differential pressure switch does open when the fan runs (after ignition) (only high modulation version).
Step
Step
Summary of Contents for Logamax GB062-24 KDE H V2
Page 57: ......