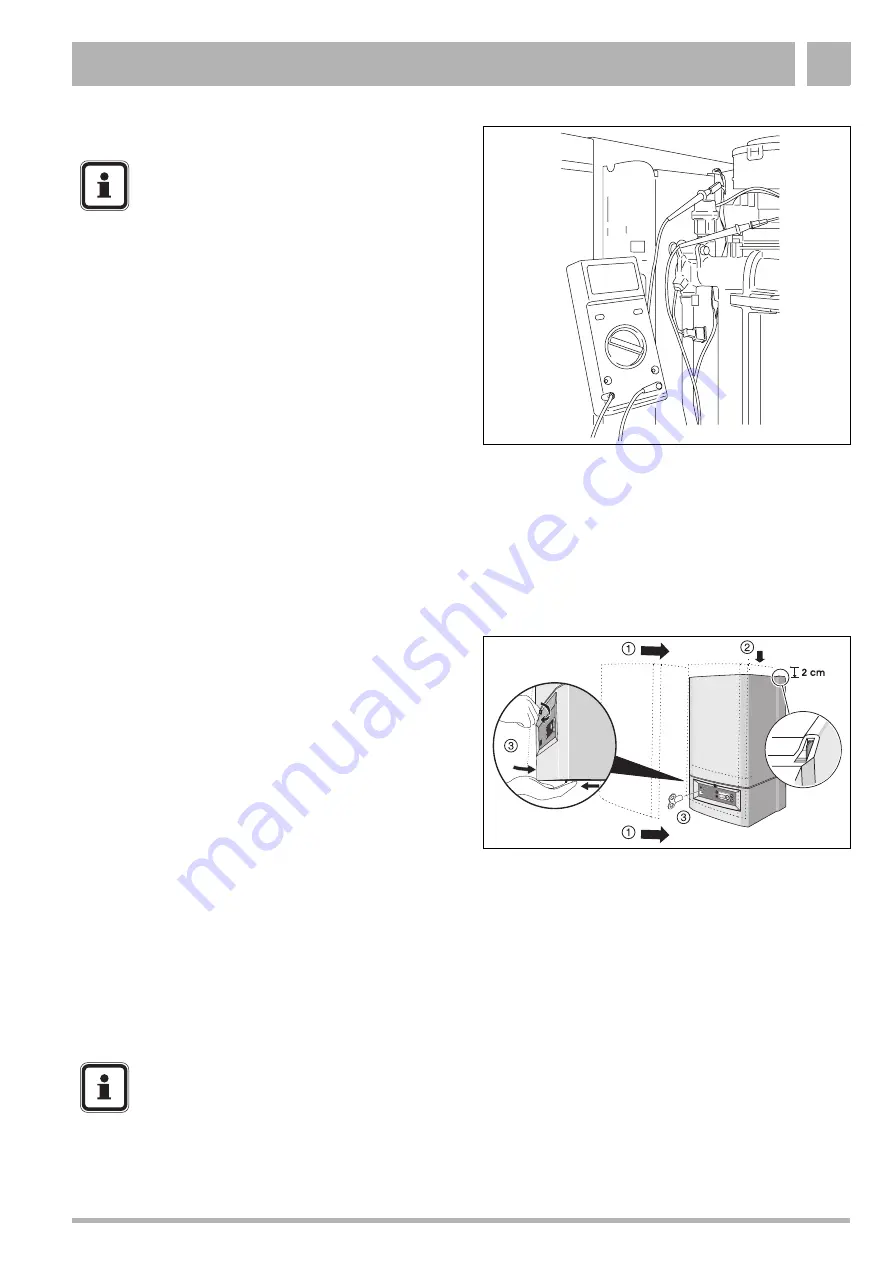
Commissioning
2
Installation and maintenance instructions for Buderus 500 - 24/S • 08/2006
39
Subject to modifications resulting from technical improvements!
Buderus • http://www.buderus-domestic.co.uk
2.1.9
Function testing
Measuring the ionisation current (fig. 58)
z
Turn the mains power switch to "
0
z
Remove the casing.
z
Loosen the connector-and-socket connection of the ionisa-
tion electrode and connect the multimeter in series.
z
On the measuring device, select the µ-direct current range.
The measuring device must have a resolution of at
least 1 µA (1 micro ampere).
z
Set mains power switch to "
1
z
Set the boiler in to partial load by pressing the service
button "
A
" once.
z
Measure the ionisation current. The ionisation current
being checked must measure >2 µA (>2 micro ampere)
direct current.
z
Enter the reading on the report form.
z
Set the mains power switch to "
0
z
Remove multimeter and restore the connector-and-socket
connection to its original state.
z
Refit the casing and secure the boiler with the radiator key
(see fig. 59).
z
Set the mains power switch to "
1
2.1.10 Handing over
After completing the installation and commissioning of the
system the installer should hand over to the householder by
the following actions:
z
Hand over all relevant documentation to the end user and
explain his/her responsibilities under the relevant national
and regional regulations.
z
Explain and demonstrate the lighting and shutting down
procedures.
fig. 58 Measuring the ionisation current
NOTE
During initial start-up and annual servicing,
make sure that all control, regulating and
safety devices are in full working order and, if
applicable, check for correct adjustment.
fig. 59 Refit casing
NOTE
Always keep the user manual and installation
and servicing instructions available for feed-
back.