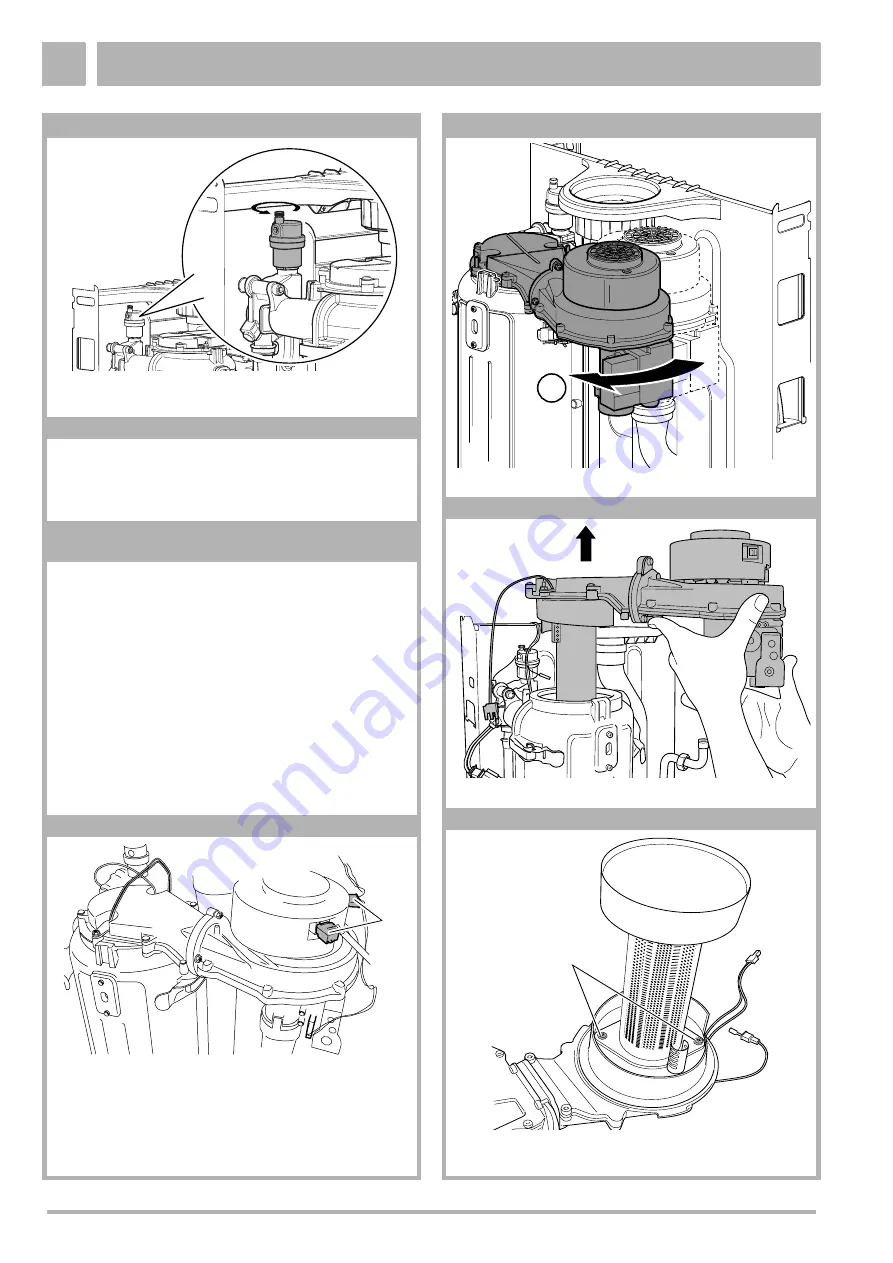
Actions
7
We reserve the right to make technical modifications
Buderus Ltd. • http://www.buderus-domestic.co.uk
68
Servicing manual Gas condensing boiler Buderus 500-24/S, 500-24/C and 500-28/C • Issued 02/2006
box 243
z
Twist the automatic air vent in the direction of the arrow to
remove.
box 244
z
Fit the new automatic air vent by following the above
procedure in reverse order.
z
Fill the heating system, vent it of air and place the boiler
into operation, see box 52 to 58.
box 245 Replace the burner
H
DANGER OF FATAL ACCIDENT
due to electric shock
A
DANGER OF FATAL ACCIDENT!
All work on gas supply pipes and gas-fitting
components must be carried out by a company
registered and authorised for this purpose.
z
Take the boiler out of operation and close the gas tap,
z
Remove the power supply plug of the glow ignitor,
z
Remove the plug of the ionisation electrode, see box 144.
z
Remove the power supply plug of the gas valve, union nut
and air silencer tube, see box 77.
box 246
z
Pull out both fan plugs (item 1).
1
box 247
z
Turn the gas/air unit clockwise by about 10°.
box 248
z
Remove the gas/air unit along with the burner.
box 249
z
Loosen both screws (item 1).
z
Remove the burner.
1
1