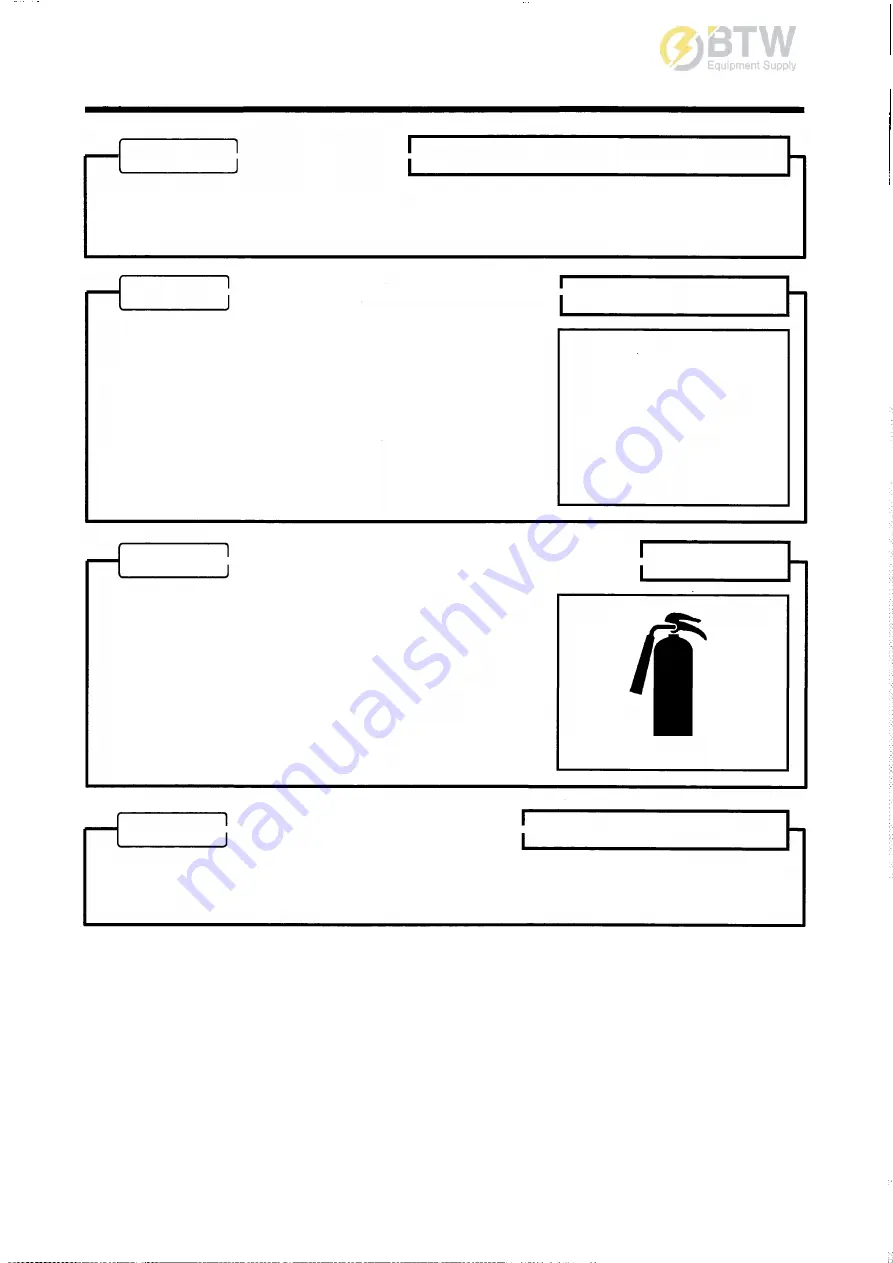
1.Safety
A
WARNING ----------
Maintain both physic/ and mental health
• Do not operate the machine when you are tired or drunk or under the influence of drugs. Otherwise, a
hasty conclusion or careless handling may cause unexpected injury or accident.
Manage your physical and mental health and be cautious in handling the machine.
A
CAUTION
i,.....-------------
• Please wear protection implements, such as a helmet,
protection glasses, earplugs, safety shoes, a glove, and a
protection-against-dust mask, according to the contents of
work for safety.
Protection equipments
e,o,,
SL�
TR0085
A
CAUTION..,..__ __________ ___
Safety fittings
• Have first-aid boxes and fire extinguishers near the machine
ready for emergency situations such as injuries and a fire.
• It is advisable to have a list of phone numbers of doctors,
ambulance and the fire department available in case of
emergency.
A
CAUTION i----------......
TR0096
Safety around the machine
• Such things as unnecessary equipment and tools, cables, hoods, covers and pieces of wood which
are a hindrance to the job, have to be cleaned and removed. This is because operators and/or
personnel nearby may stumble on them and may be injured.
1-4
BTW Equipment Supply • www.btwequipmentsupply.com • ORDER PARTS ONLINE