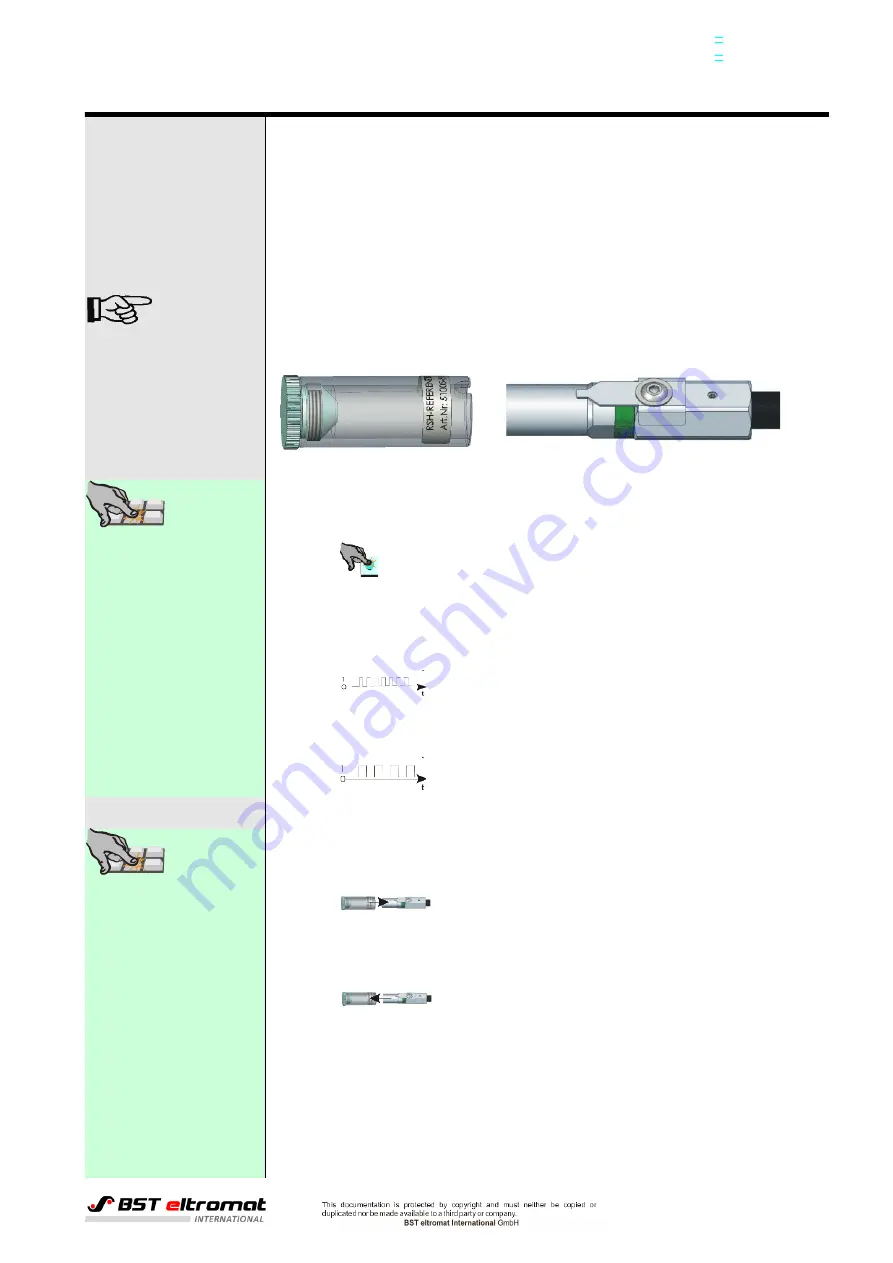
register
25
RSH-EC_Cap_10_en
Rev. 1.0 - 02/2012
10
Adjustment of the register sensor
Review
The register sensor can only operate fault free when adjusted. During
the adjustment, internal parameters are adjusted so that the measured
results are optimised. This compensate for lighting wear. Adjustment is
started in the register controller.
Required aids
Mirror tube (Art.No.: 5100581000).
Ensure cleanliness. Immediately remove soiling/particles from the lens
and the mirror tube.
Fig. 10.1
Preparatory work:
Perform the following operating steps to adjust the register sensor:
Start adjustment in the user interface of the connec-
ted register controller.
•
Only carry out adjustment, wenn the sensing head
has been removed from the holder and does not
point onto the printed web.
Fast flashing signals that the sensing head is not
ready for adjustment. Do not point to reflecting
surfaces with the sensing head.
The lens system flashes at medium frequency to
signal readiness for adjustment.
Tightly place the mirror tube on the lenses (channel
1: green). Flashing continues. Adjustment is carried
out. Do not move the mirror tube during adjustment.
Adjustment end is signalled by fast flashing.
Remove the mirror tube again from the sensing
head.