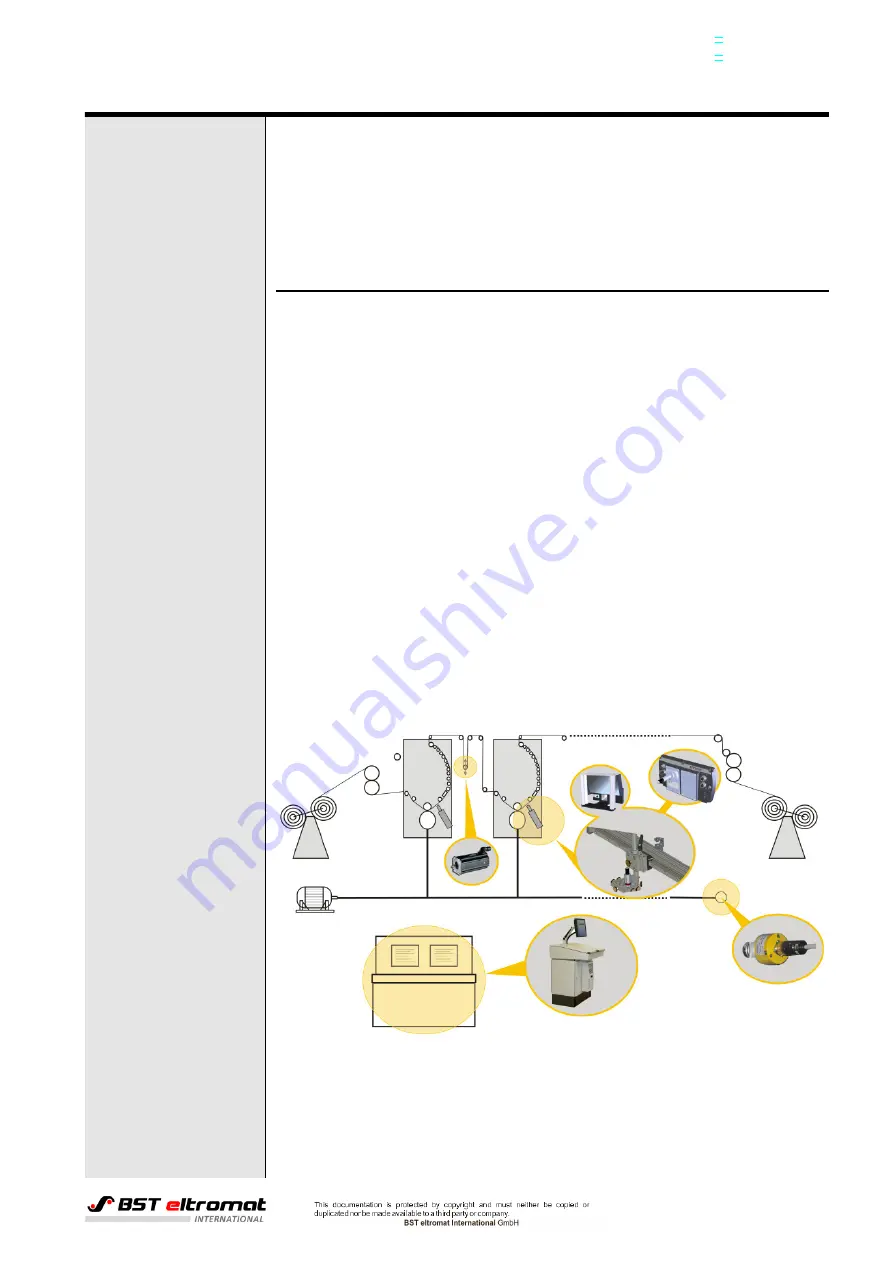
register
6
regi_star_MA_Kap_2_en
Rev. 1.2.1 - 08/2014
2
System overview and safety instructions for register control systems
Review
This chapter gives an overview about the register control components.
Moreover, this chapter contains a summary off all safety instructions
and which need to be observed for register control assembly works.
2.1 Components of a Register Control System
A register control system consists of the following components:
• control unit,
• register sensor (fibre optic/measuring on the traverse bar and elec-
tronics in the housing),
• traverse bar,
• shaft encoder,
• drive for the positioning of linear rollers (optional)
If the register control system is used in an explosive area, different
terminal boxes for connecting the cables will be delivered as well. It is
possible to have the components delivered on a mounting plate instead
of a control unit. The following image shows an example of the different
assembly / installation locations of a web monitoring system. The
displayed printing press is a general example and must in no case
conform to your model.
Fig. 2.1