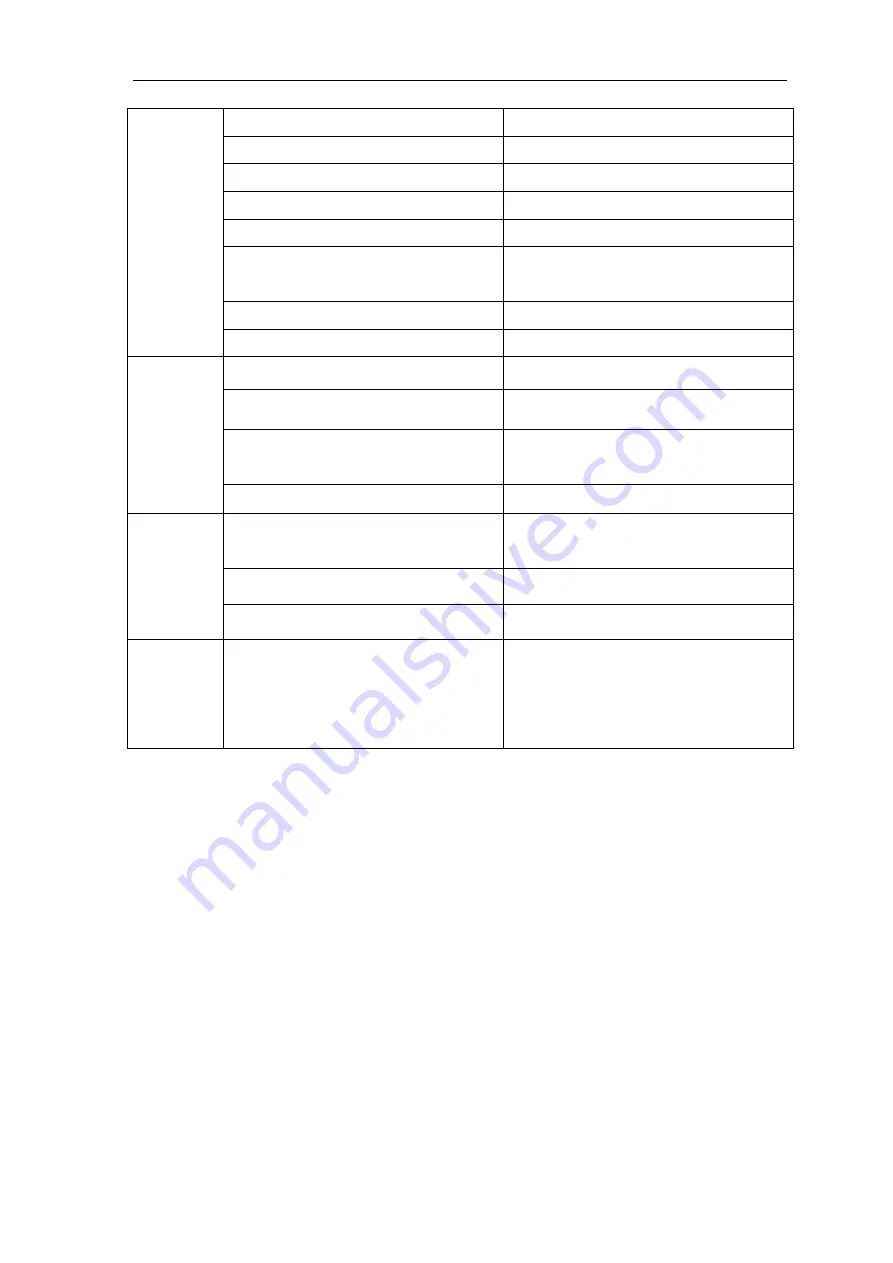
Pump gets
too hot
Ambient temperature is too high
Set pump up correctly
Process gas is too hot
Change the process
Oil level is too low
Add oil to reach the correct oil level
Oil is unsuitable
Change the oil
Oil cycle is obstructed
Clean or repair the oil lines
Exhaust filter / exhaust line is
obstructed
Replace the exhaust filter, clean the
exhaust line
Exhaust valve is malfunctioning
Repair the valve
Pump module is no longer usable
Replace the pump module
Oil in intake
line or in
vacuum
vessel
Oil comes from the vacuum system
Check the vacuum system
Anti-suck back valve is obstructed
Clean or repair the valve
Sealing surfaces or anti-suck back valve
are damaged or dirty
Clean or repair the intake port and valve
Oil level is too high
Drain the excess oil
Pump is
excessively
noisy
Oil level is very low (oil is no longer
visible)
Add oil
Coupling element is worn
Install new coupling element
Large vacuum leak in system
Repair vacuum leak
Oil is turbid
Condensation
Degas the oil or change the oil and clean
the pump. Precaution : open the gas
ballast valve or insert a condensate trap.
Clean the gas ballast intake filter
21