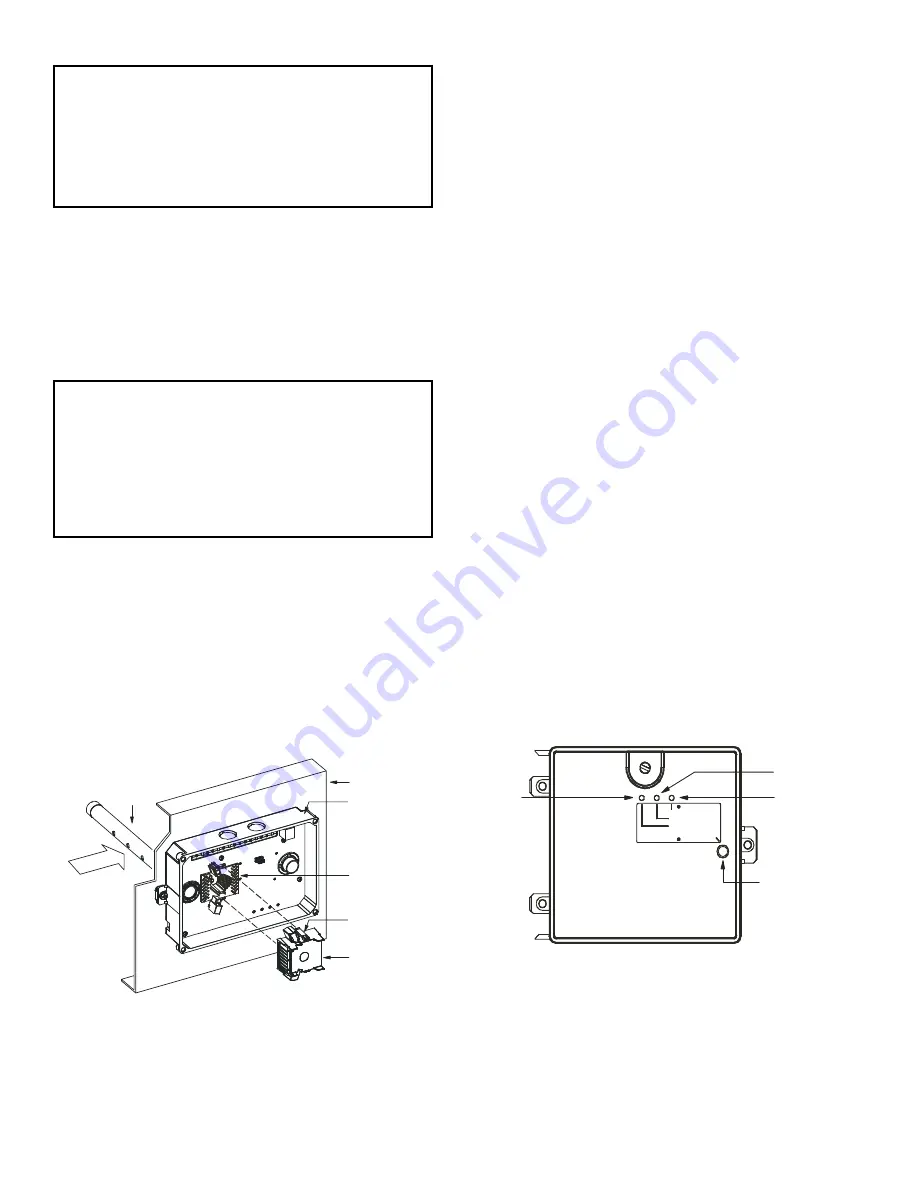
26
Dirty Sensor Test Using an SD-TRK4
1. Turn the key switch to the RESET/TEST position for two
seconds.
2. Verify that the test/reset station’s Trouble LED flashes.
Detector Cleaning
CLEANING THE SMOKE DETECTOR
Clean the duct smoke sensor when the Dirty LED is flashing
continuously or sooner if conditions warrant.
1. Disconnect power from the duct detector, then remove the
sensor’s cover (see Fig. 44).
2. Using a vacuum cleaner, clean compressed air, or a soft
bristle brush, remove loose dirt and debris from inside the
sensor housing and cover. Use isopropyl alcohol and a
lint-free cloth to remove dirt and other contaminants from
the gasket on the sensor’s cover.
3. Squeeze the retainer clips on both sides of the optic housing.
4. Lift the housing away from the printed circuit board.
5. Gently remove dirt and debris from around the optic plate
and inside the optic housing.
6. Replace the optic housing and sensor cover.
7. Connect power to the duct detector, then perform a sensor
alarm test.
Fig. 44 — Sensor Cleaning Diagram
Indicators
NORMAL STATE
The smoke detector operates in the normal state in the absence
of any trouble conditions and when its sensing chamber is free
of smoke. In the normal state, the Power LED on both the sen-
sor and the controller are on and all other LEDs are off.
ALARM STATE
The smoke detector enters the alarm state when the amount of
smoke particulate in the sensor’s sensing chamber exceeds the
alarm threshold value. (See Table 8.) Upon entering the alarm
state:
• The sensor’s Alarm LED and the controller’s Alarm LED
turn on.
• The contacts on the controller’s two auxiliary relays switch
positions.
• The contacts on the controller’s alarm initiation relay
close.
• The controller’s remote alarm LED output is activated
(turned on).
• The controller’s high impedance multiple fan shutdown
control line is pulled to ground Trouble state.
The SuperDuct smoke detector enters the trouble state under
the following conditions:
• A sensor’s cover is removed and 20 minutes pass before it
is properly secured.
• A sensor’s environmental compensation limit is reached
(100% dirty).
• A wiring fault between a sensor and the controller is detected.
An internal sensor fault is detected upon entering the trouble
state:
• The contacts on the controller’s supervisory relay switch
positions (see Fig. 45).
• If a sensor detects trouble, the sensor’s Trouble LED the
controller’s Trouble LED turns on.
• If 100% dirty, the sensor’s Dirty LED turns on and the
controller’s Trouble LED flashes continuously.
• If there is a wiring fault between a sensor and the control-
ler, the controller’s Trouble LED turns on, but not the sen-
sor’s LED.
Fig. 45 — Controller Assembly
NOTE: All troubles are latched by the duct smoke detector. The
trouble condition must be cleared and then the duct smoke detec-
tor must be reset in order to restore it to the normal state.
IMPORTANT: OPERATIONAL TEST ALERT
Failure to follow this ALERT can result in an unnecessary
evacuation of the facility.
Holding the test magnet against the sensor housing for
more than seven seconds will put the duct detector into the
alarm state and activate all automatic alarm responses.
IMPORTANT: OPERATIONAL TEST ALERT
Failure to follow this ALERT can result in an unnecessary
evacuation of the facility.
If the smoke detector is connected to a fire alarm system,
first notify the proper authorities that the detector is under-
going maintenance, then disable the relevant circuit to
avoid generating a false alarm.
HVAC DUCT
SAMPLING
TUBE
RETAINER
CLIP
OPTIC
PLATE
OPTIC
HOUSING
SENSOR
HOUSING
AIRFLOW
ALARM
POWER
TEST/RESET
SWITCH
TROUBLE
RESET
ALARM
TROUBLE
POWER
Summary of Contents for Preferred 581J04-14
Page 36: ...36 Fig 60 Integrated Gas Control IGC Board RED LED STATUS ...
Page 44: ...44 Fig 65 RTU Open Overlay for Economizer Wiring ...
Page 45: ...45 Fig 66 VFD Overlay for W2770 Controller Wiring ...
Page 100: ...100 Fig F 581J 08 09 YAC Control Diagram 208 230 3 60 460 575 3 60 APPENDIX D WIRING DIAGRAMS ...
Page 101: ...101 Fig G 581J 11YAC Control Diagram 208 230 3 60 460 575 3 60 APPENDIX D WIRING DIAGRAMS ...
Page 102: ...102 Fig H 581J 12 YAC Control Diagram 208 230 3 60 460 575 3 60 APPENDIX D WIRING DIAGRAMS ...
Page 103: ...103 Fig I 581J 04 06 YAC Power Diagram 208 230 1 60 APPENDIX D WIRING DIAGRAMS ...
Page 104: ...104 Fig J 581J 04 06 YAC Power Diagram 208 230 3 60 460 3 60 APPENDIX D WIRING DIAGRAMS ...
Page 105: ...105 Fig K 581J 04 06 YAC Power Diagram 575 3 60 APPENDIX D WIRING DIAGRAMS ...
Page 108: ...108 Fig N 581J 07 12A B C YAC Power Diagram 208 230 3 60 460 3 60 APPENDIX D WIRING DIAGRAMS ...
Page 109: ...109 Fig O 581J 07 12A B C YAC Power Diagram 575 3 60 APPENDIX D WIRING DIAGRAMS ...
Page 110: ...110 Fig P 581J 08 09 YAC Power Diagram 230 460 3 60 APPENDIX D WIRING DIAGRAMS ...
Page 111: ...111 Fig Q 581J 08 09 YAC Power Diagram 575 3 60 APPENDIX D WIRING DIAGRAMS ...
Page 112: ...112 Fig R 581J 11 YAC Power Diagram 208 230 3 60 APPENDIX D WIRING DIAGRAMS ...
Page 113: ...113 Fig S 581J 11 YAC Power Diagram 460 3 60 APPENDIX D WIRING DIAGRAMS ...
Page 114: ...114 Fig T 581J 11 YAC Power Diagram 575 3 60 APPENDIX D WIRING DIAGRAMS ...
Page 115: ...115 Fig U 581J 12 YAC Power Diagram 230 460 3 60 APPENDIX D WIRING DIAGRAMS ...
Page 116: ...116 Fig V 581J 12 YAC Power Diagram 575 3 60 APPENDIX D WIRING DIAGRAMS ...
Page 117: ...117 Fig W 581J 14 YAC Control Diagram 208 230 3 60 460 575 3 60 APPENDIX D WIRING DIAGRAMS ...
Page 118: ...118 Fig X 581J 14 YAC Power Diagram 208 230 3 60 APPENDIX D WIRING DIAGRAMS ...
Page 119: ...119 Fig Y 581J 14 YAC Power Diagram 460 3 60 APPENDIX D WIRING DIAGRAMS ...
Page 120: ...120 Fig Z 581J 14 YAC Power Diagram 575 3 60 APPENDIX D WIRING DIAGRAMS ...
Page 143: ...143 Fig AW RTU Open Wiring Diagram APPENDIX D WIRING DIAGRAMS ...