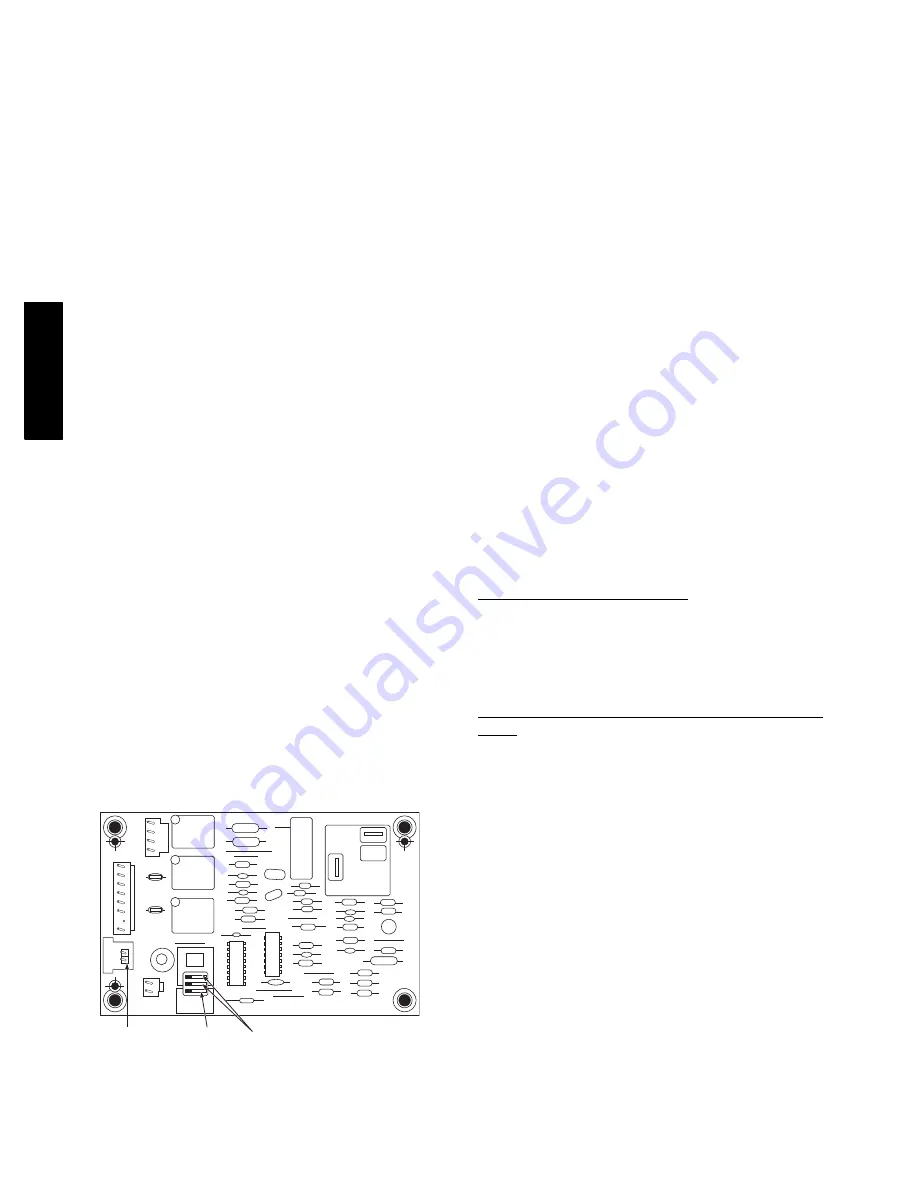
8
The compressor will always start unloaded and stay unloaded for
five seconds even when the thermostat is calling for high stage
capacity.
Quiet Shift
−
2
Quiet shift
−
2 is a field selectable defrost mode (factory set to OFF),
which will reduce the occasional noise that could be heard at the
start of defrost cycle and restarting of heating cycle. It is selected
by placing DIP switch 3 on defrost board in the ON position.
When Quiet Shift
−
2 switch is placed in ON position, and defrost is
initiated, the following sequence of operation will occur: The
compressor will be de
−
energized for approximately 1 minute, then
the reversing valve will be energized. A few seconds later, the
compressor will be re
−
energized and the normal defrost cycle
starts.
Once defrost termination conditions have been met, the following
sequence will occur: The compressor will be de
−
energized for
approximately 1 minute, then the reversing valve will be
de
−
energized. A few seconds later, the compressor will be
re
−
energized and the normal heating cycle starts.
Defrost
The defrost control is a time/temperature control which has field
selectable settings of 30, 60, 90, or 120 minutes, factory set to 90
minutes. These settings represent the amount of time that must pass
after closure of the defrost thermostat before the defrost sequence
begins.
The defrost thermostat senses coil temperature throughout the
heating cycle. When the coil temperature reaches the defrost
thermostat setting of approximately 32
_
F (0
_
C), it will close,
which energizes the DFT terminal and begins the defrost timing
sequence. When the DFT has been energized for the selected time,
the defrost cycle begins. Defrost cycle is terminated when defrost
thermostat opens, or automatically after 10 minutes.
Defrost Speedup
To initiate a forced defrost, speedup pins (J1) must be shorted with
a flat head screwdriver for 5 seconds and
RELEASED
. If the
defrost thermostat is open, a short defrost cycle will be observed
(actual length depends on Quiet Shift
−
2 switch position). When
Quiet Shift
−
2 is off, only a short 30 second defrost cycle is
observed. With Quiet Shift
−
2 ON, the speedup sequence is
approximately 3 minutes; 1 minute compressor off period followed
by 30 seconds of defrost with compressor operation. When
returning to heating mode, the compressor will turn off for an
additional 1 minute.
If the defrost thermostat is closed, a complete defrost cycle is
initiated. If the Quiet Shift
−
2 switch is turned on, the compressor
will be turned off for two 1 minute intervals as explained
previously.
OF2
O
F1
ON
QUIET
SHIFT
120
30
60
60
30
90
INTER
V
AL
TIMER
OFF
P3
DFT
O R
W
2
Y C
T2 C C O
DFT
T1
Y
P1
J1
SPEEDUP
Speedup
Pins
Defrost interval
DIP switches
Quiet
Shift
A05378
Fig. 11
−
Defrost Control
Check Charge
NOTE
:
CHARGE IN HIGH STAGE ONLY.
Factory charge amount and desired subcooling are shown on unit
rating plate. Charging method is shown on information plate inside
unit. To properly check or adjust charge, conditions must be
favorable for subcooling charging. Favorable conditions exist
when the outdoor temperature is between 70
_
F and 100
_
F
(21.11
_
C and 37.78
_
C), and the indoor temperature is between
70
_
F and 80
_
F (21.11
_
C and 26.67
_
C). Follow the procedure
below:
Unit is factory charged for 15ft (4.57 m) of lineset. Adjust charge
by adding or removing 0.6 oz/ft (.018 kg/m) of 3/8 liquid line
above or below 15ft (4.57 m) respectively.
For standard refrigerant line lengths (80 ft/24.38 m or less), allow
system to operate in cooling mode at least 15 minutes. If conditions
are favorable, check system charge by subcooling method. If any
adjustment is necessary, adjust charge slowly and allow system to
operate for 15 minutes to stabilize before declaring a properly
charged system.
If the indoor temperature is above 80
_
F (26.67
_
C), and the
outdoor temperature is in the favorable range, adjust system charge
by weight based on line length and allow the indoor temperature to
drop to 80
_
F (26.67
_
C) before attempting to check system charge
by subcooling method as described above.
If the indoor temperature is below 70
_
F (21.11
_
C), or the outdoor
temperature is not in the favorable range, adjust charge for line set
length above or below 15ft (4.57 m) only. Charge level should then
be appropriate for the system to achieve rated capacity. The charge
level could then be checked at another time when the both indoor
and outdoor temperatures are in a more favorable range.
NOTE
: If line length is beyond 80 ft (24.38 m) or greater than 20
ft (6.10 m) vertical separation, See Long Line Guideline for
special charging requirements.
Heating Check Chart Procedure
To check system operation during heating cycle, refer to the
Heating Check Chart on outdoor unit. This chart indicates whether
a correct relationship exists between system operating pressure and
air temperature entering indoor and outdoor units. If pressure and
temperature do not match on chart, system refrigerant charge may
not be correct. Do not use chart to adjust refrigerant charge.
Verify units for proper switching between low & high
stages
Check the suction pressures at the service valves. Suction pressure
should be reduced by 3
−
10% when switching from low to high
capacity.
Compressor current should increase 20
−
45% when switching from
low to high stage. The compressor solenoid when energized in
high stage, should measure 24vac at leads inside control box.
When the compressor is operating in low stage the 24v DC
compressor solenoid coil is de
−
energized. When the compressor is
operating in high stage, the 24v DC solenoid coil is energized. The
solenoid plug harness that is connected to the compressor HAS an
internal rectifier that converts the 24v AC signal to 24v DC.
DO
NOT INSTALL A PLUG WITHOUT AN INTERNAL
RECTIFIER.
226A