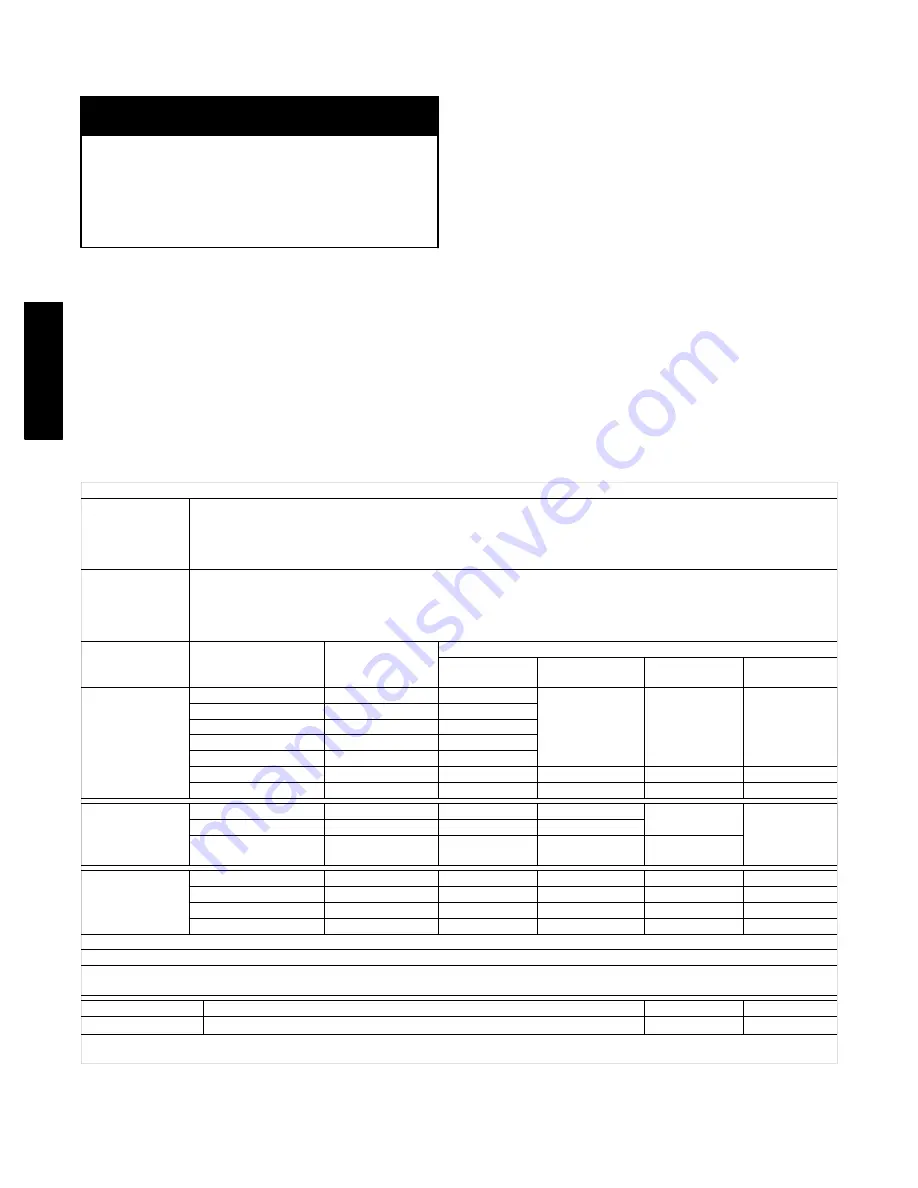
48
2-Pipe and 1-Pipe Vent Termination
NOTE
: Follow the instructions of the vent terminal manufacturer.
These instructions are provided as a reference, only.
RECOMMENDED SUPPORT FOR VENT
TERMINATIONS
It is recommended that sidewall vent terminations in excess of
24 inches (0.6 M) in vertical length be supported by
EITHER
the Direct Vent Termination Kit shown in Table 13 or by
field
−
supplied brackets or supports fastened to the structure.
NOTICE
Determine an appropriate location for termination kit using the
guidelines provided in section “Locating The Vent Termination” in
this instruction.
1. Cut two holes, one for each pipe, of appropriate size for
pipe size being used.
2. Loosely install elbow in bracket (if used) and place assem-
bly on combustion
−
air pipe.
3. Install bracket as shown in Fig. 54 and 56.
NOTE
: For applications using vent pipe option indicated by
dashed lines in Fig. 54 and 55, rotate vent elbow 90
from
position.
4. Disassemble loose pipe fittings. Clean and cement using
same procedures as used for system piping.
DO NOT CE-
MENT POLYPROPYLENE FITTINGS.
(Direct Vent / 2-Pipe System ONLY)
When two or more furnaces are vented near each other, two vent
terminations may be installed as shown in Fig. 54, but next vent
termination, or pair of vent terminations, must be at least 36 in.
(914 mm) away from the first two terminations. It is important that
vent terminations be made as shown in Fig. 54 to avoid
recirculation of vent gases.
Inducer Outlet Restrictor
To improve efficiency and operation of 40K, 60K, 100K or 120K
BTUH input models on very short vent systems, an inducer outlet
restrictor is required to be installed on the outlet of the inducer
assembly. The outlet restrictor is shown in the footnote of Table 17
−
Maximum Equivalent Vent Length. The outlet restrictor for the
40K models is shipped in the loose parts bag. See Table 17 for
usage, part numbers and sourcing of 60K, 100K and 120K inducer
outlet restrictors.
To determine if the outlet restrictor is required, see Table 17.
Failure to use an outlet restrictor on the 40K input model when
required may result in flame disturbance or flame sense
lockout.
Table 15 – Approved Combustion-Air and Vent Pipe, Fitting and Cement Materials (U.S.A. Installations)
MATERIALS
USA
1. All pipe, fittings, primers*, and solvents* must conform to American National Standards Institute (ANSI) standards and
American Society for Testing and Materials (ASTM) standards or ULC S636 where required by code.
2. See Table below for approved materials for use in the U.S.A.
3. ULC S636 vent systems must be composed of pipe, fittings, cements, and primers from the same supplier.
4. Factory accessory concentric vent kits are ULC S636 listed.
CANADA
1. Installation in Canada must conform to the requirements of CAN/CSA B149 code.
2. Vent systems must be composed of pipe, fittings, cements, and primers from the same supplier and listed to ULC S636.
3. Not all materials below may be approved or listed to ULC S636.
4. Royal Pipe and IPEX are approved suppliers of ULC S636 pipe, fittings, cements and primers*.
5. Factory accessory concentric vent kits are ULC S636 listed for use with Royal Pipe and IPEX venting systems
Material
Description
Type
ASTM or ULC Specification
Pipe
Solvents/
Primers**
Cements
PVC
Pressure Pipe
Schedule 40
D1785
D2466
or
D2665
F656
D2564
DWV
Schedule 40
D1785/D2665
Cellular Core
Schedule 40
F891
SDR 26
N/A
D2241
SDR 21
N/A
D2241
IPEX
Schedule 40
ULC S636
ULC S636
ULC S636
ULC S636
Royal Pipe
Schedule 40
ULC S636
ULC S636
ULC S636
ULC S636
ABS
ABS
Schedule 40
D1527
D2468
Clear Cleaner
For ABS†
D2235
DWV
−
IPS Sizes
Schedule 40
D2661
D2661
Cellular Core DWV
−
IPS
Sizes
Schedule 40
F628
CPVC
Pressure Pipe
Schedule 40
F441
F438
F656
F493
SDR
N/A
F442
N/A
IPEX
Schedule 40
ULC S636
ULC S636
ULC S636
ULC S636
Royal Pipe
Schedule 40
ULC S636
ULC S636
ULC S636
ULC S636
*PVC and ABS pipe may use either DWV or pressure rated fittings.
**Colored or tinted solvents or primers must be used where required by code in the USA
†ABS plastic does not require a primer before solvent cementing. A cleaner for ABS is recommended to remove any surface residue. ABS
cleaners are not subject to ASTM standards.
Polypropylene
Approved Manufacturer
Solvents Primers Cements
Poly
Pro
®
M & G Dura Vent
Not Permitted
Not Permitted
NOTE: Polypropylene vent systems are UL
*
1738 and ULC S636 listed and assembled using mechanical fastening systems
supplied by the vent manufacturer.
912S